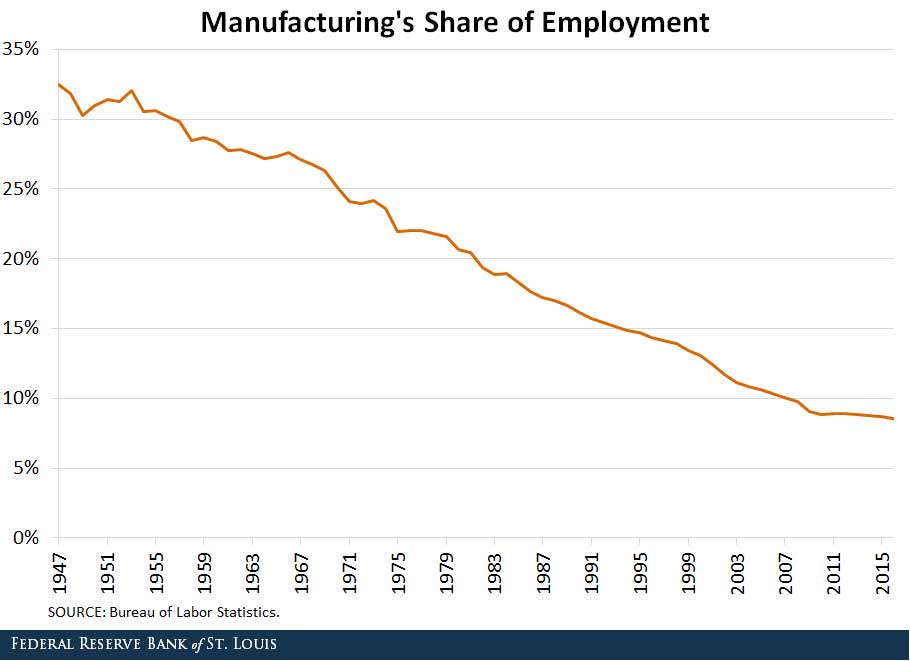
General managers are responsible for formulating strategy, hiring functional leaders, and communicating with the company's stakeholders. This article will discuss the responsibilities and skills required to excel in this position. Continue reading to learn more about the duties of a general manager. You will need to be able to communicate and present effectively in order for you to be a successful general manger. You must also be proficient in financial management. Your ability and persistence to manage your company's finances and ensure its success are key factors. You will need to be a leader in a team and able create trust with customers.
Strategy formulation is the responsibility of GMs
While it is true that GMs have responsibility for strategy formulation, there are risks to the process. An example of this is a GM who is driven by his own ambitions or a member a leadership group may exaggerate their role in formulating strategy. Managers are subject to their personal motivations and biases. Their decisions may not be based upon objective data but on their personal interpretations or assumptions.
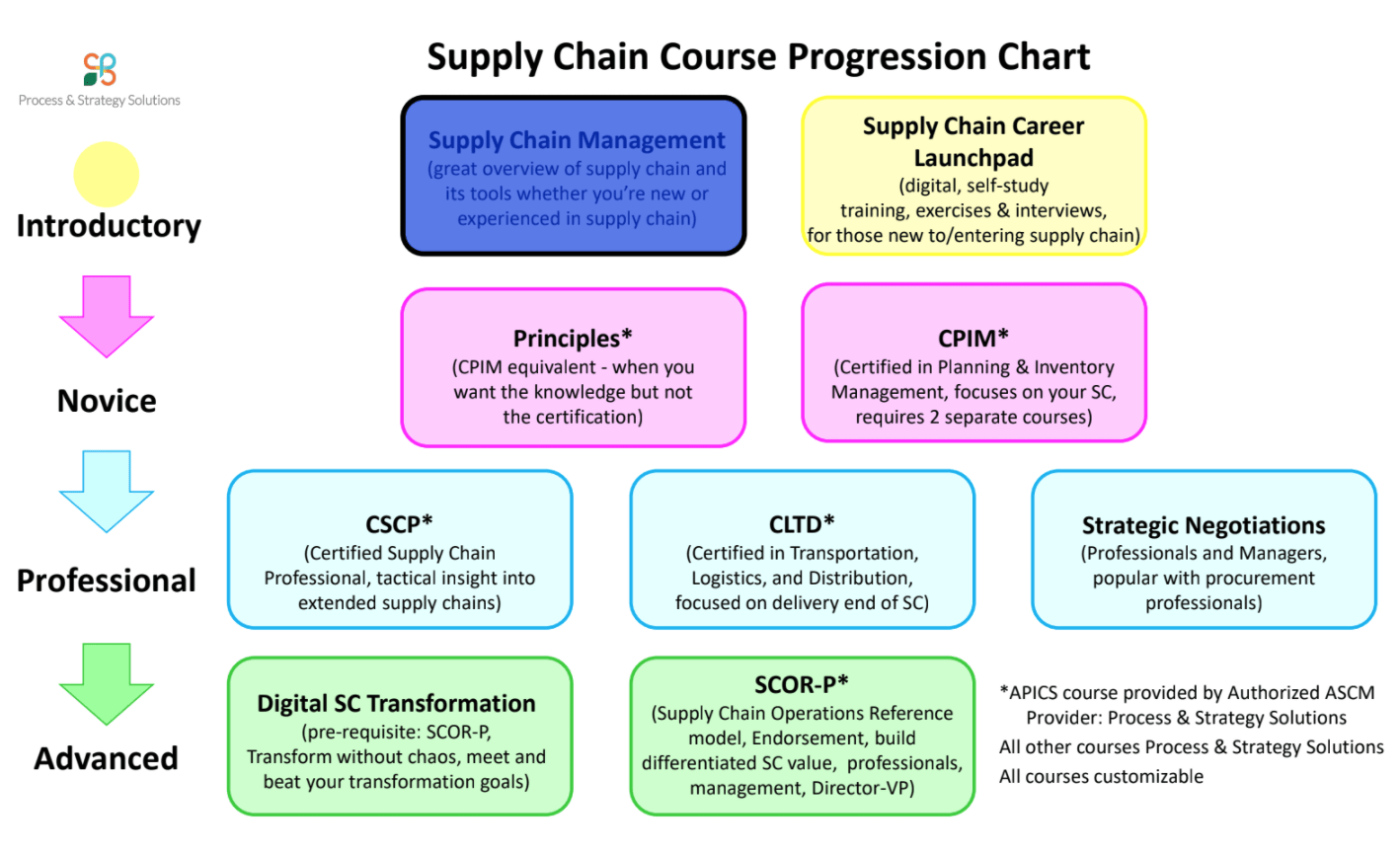
They are looking for functional leaders
The organization and its business units are under the general manager's control. They have to manage the entire business from strategy to structure to budgets and people. They are also responsible in the day to day operations of the business unit. In order to succeed in this role, they will need to understand the language of finance and human resources. The general manager role is complex, as it involves ensuring the success and growth of the entire organization.
They collaborate closely with their subordinates
General managers are responsible for understanding the organisation's internal workings and communicating with all departments. They should also be able analyze to find solutions and identify problems. General managers are expected to be strong leaders who can delegate tasks and ensure that employees are working to the best of their abilities. They must be able work with colleagues in other departments and give clear directions to their subordinates.
They communicate with each other
Many general manager tasks require good communication skills. General managers can help employees listen by hosting training sessions, or coaching them in effective communication techniques. They can host more meetings for their teams and organize social events to promote better communication. Here are some tips to improve general manager communication skills. All good managers should make themselves accessible to employees to help them succeed. This is a crucial part of their job description. They should also be available to answer questions and provide guidance when necessary.
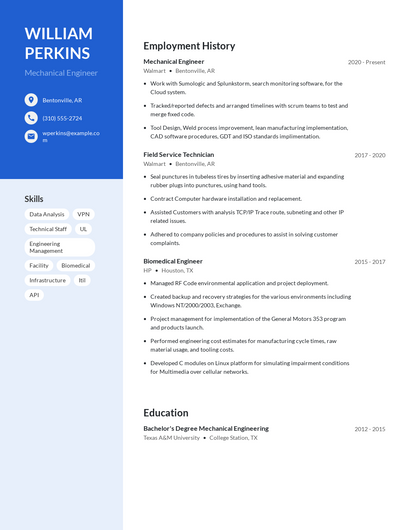
They are motivating
The top GMs are able and willing to motivate staff. They are willing and able to work overtime, demonstrate dedication to the company, and set an example for others. They also encourage their staff to live up to their high standards. These are just a few of the motivating methods that top managers use to motivate their employees:
FAQ
How important is automation in manufacturing?
Automating is not just important for manufacturers, but also for service providers. It allows them provide faster and more efficient services. They can also reduce their costs by reducing human error and improving productivity.
What are the four types of manufacturing?
Manufacturing is the process that transforms raw materials into useful products. It involves many different activities such as designing, building, testing, packaging, shipping, selling, servicing, etc.
What are the responsibilities of a logistic manager?
Logistics managers ensure that goods arrive on time and are unharmed. This is achieved by using their knowledge and experience with the products of the company. He/she should ensure that sufficient stock is available in order to meet customer demand.
How can manufacturing overproduction be reduced?
Improved inventory management is the key to reducing overproduction. This would reduce the time needed to manage inventory. This would allow us to use our resources for more productive tasks.
A Kanban system is one way to achieve this. A Kanban board is a visual display used to track work in progress. In a Kanban system, work items move through a sequence of states until they reach their final destination. Each state has a different priority level.
When work is completed, it can be transferred to the next stage. It is possible to keep a task in the beginning stages until it gets to the end.
This allows for work to continue moving forward, while also ensuring that there is no work left behind. With a Kanban board, managers can see exactly how much work is being done at any given moment. This allows them the ability to adjust their workflow using real-time data.
Another way to control inventory levels is to implement lean manufacturing. Lean manufacturing works to eliminate waste throughout every stage of the production chain. Anything that doesn't add value to the product is considered waste. These are some of the most common types.
-
Overproduction
-
Inventory
-
Unnecessary packaging
-
Excess materials
These ideas can help manufacturers improve efficiency and reduce costs.
What skills does a production planner need?
To become a successful production planner, you need to be organized, flexible, and able to multitask. Communication skills are essential to ensure that you can communicate effectively with clients, colleagues, and customers.
Can we automate some parts of manufacturing?
Yes! Yes! Automation has existed since ancient times. The Egyptians invent the wheel thousands of year ago. Robots are now used to assist us in assembly lines.
Robotics is used in many manufacturing processes today. These include:
-
Robots for assembly line
-
Robot welding
-
Robot painting
-
Robotics inspection
-
Robots that create products
There are many other examples of how manufacturing could benefit from automation. For example, 3D printing allows us to make custom products without having to wait for weeks or months to get them manufactured.
Statistics
- In the United States, for example, manufacturing makes up 15% of the economic output. (twi-global.com)
- [54][55] These are the top 50 countries by the total value of manufacturing output in US dollars for its noted year according to World Bank.[56] (en.wikipedia.org)
- Job #1 is delivering the ordered product according to specifications: color, size, brand, and quantity. (netsuite.com)
- According to a Statista study, U.S. businesses spent $1.63 trillion on logistics in 2019, moving goods from origin to end user through various supply chain network segments. (netsuite.com)
- According to the United Nations Industrial Development Organization (UNIDO), China is the top manufacturer worldwide by 2019 output, producing 28.7% of the total global manufacturing output, followed by the United States, Japan, Germany, and India.[52][53] (en.wikipedia.org)
External Links
How To
How to Use the Just In Time Method in Production
Just-intime (JIT), a method used to lower costs and improve efficiency in business processes, is called just-in-time. It's the process of obtaining the right amount and timing of resources when you need them. This means that you only pay the amount you actually use. Frederick Taylor was the first to coin this term. He developed it while working as a foreman during the early 1900s. He observed how workers were paid overtime if there were delays in their work. He decided to ensure workers have enough time to do their jobs before starting work to improve productivity.
JIT is about planning ahead. You should have all the necessary resources ready to go so that you don’t waste money. You should also look at the entire project from start to finish and make sure that you have sufficient resources available to deal with any problems that arise during the course of your project. You'll be prepared to handle any potential problems if you know in advance. You won't have to pay more for unnecessary items.
There are several types of JIT techniques:
-
Demand-driven JIT: This is a JIT that allows you to regularly order the parts/materials necessary for your project. This will enable you to keep track of how much material is left after you use it. This will allow you to calculate how long it will take to make more.
-
Inventory-based: You stock materials in advance to make your projects easier. This allows you to predict how much you can expect to sell.
-
Project-driven: This is an approach where you set aside enough funds to cover the cost of your project. Once you have an idea of how much material you will need, you can purchase the necessary materials.
-
Resource-based: This is the most common form of JIT. You allocate resources based on the demand. For example, if there is a lot of work coming in, you will have more people assigned to them. If you don’t have many orders you will assign less people to the work.
-
Cost-based : This is similar in concept to resource-based. But here, you aren't concerned about how many people your company has but how much each individual costs.
-
Price-based: This approach is very similar to the cost-based method except that you don't look at individual workers costs but the total cost of the company.
-
Material-based: This is very similar to cost-based but instead of looking at total costs of the company you are concerned with how many raw materials you use on an average.
-
Time-based JIT: This is another variant of resource-based JIT. Instead of focusing on how much each employee costs, you focus on how long it takes to complete the project.
-
Quality-based JIT: This is another variation of resource based JIT. Instead of worrying about the costs of each employee or how long it takes for something to be made, you should think about how quality your product is.
-
Value-based JIT : This is the newest type of JIT. In this scenario, you're not concerned about how products perform or whether customers expect them to meet their expectations. Instead, you are focused on adding value to the marketplace.
-
Stock-based: This stock-based method focuses on the actual quantity of products being made at any given time. It's used when you want to maximize production while minimizing inventory.
-
Just-in time (JIT), planning: This is a combination JIT/supply chain management. This refers to the scheduling of the delivery of components as soon after they are ordered. It reduces lead times and improves throughput.