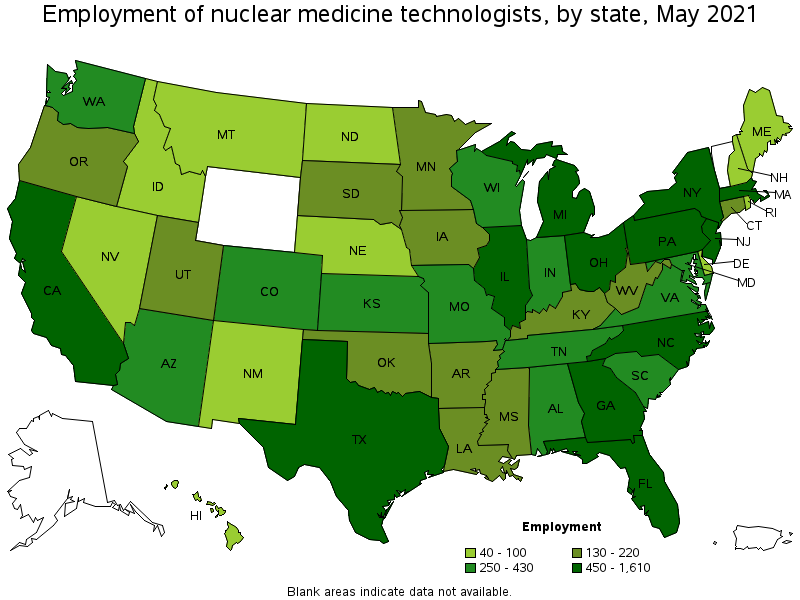
A nuclear engineer can expect to make six-figures to seven-figures. In addition to their normal duties, a nuclear engineer can oversee the construction of nuclear facilities as well as supervise work in closed facilities. The job may also require defending their work from the public. Nuclear engineers are in demand for a wide variety of reasons. Their leadership skills are also highly in demand. There are many factors that affect the salary of this profession, such as education and experience.
A bachelor's degree in nuclear engineering is equivalent to a median salary
The federal government has the highest number of nuclear engineers. Other prominent employers include the engineering and scientific research and design services sectors. The increased demand for nuclear engineers will drive growth in the engineering and research & development sectors over the next 10 years, due to the growing interest in nuclear power. While there are not currently any commercial nuclear power plants in operation, this technology could allow them to increase their production.
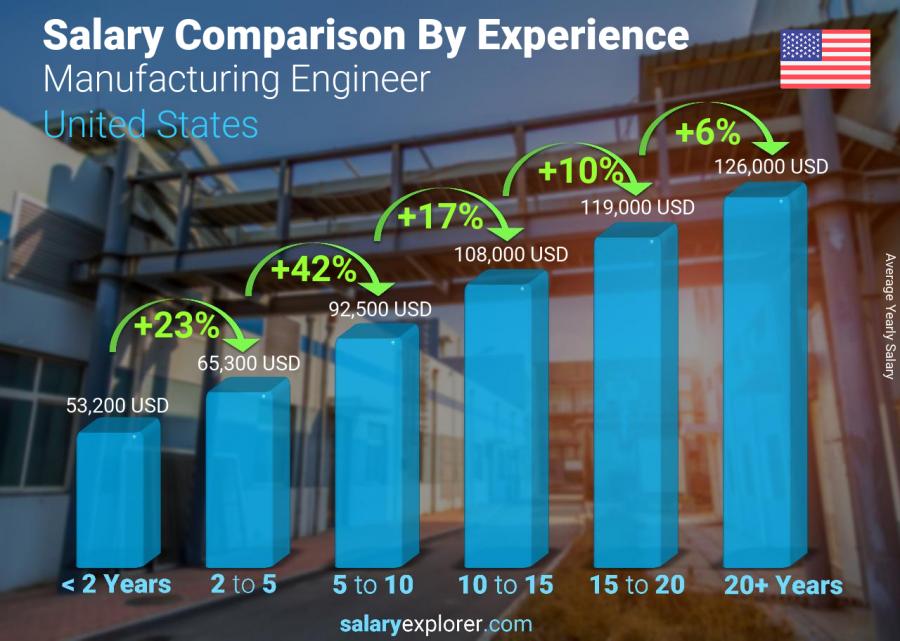
To become a Nuclear Engineer, you will need a Bachelor's Degree in Engineering or a closely related field. A bachelor's program in nuclear engineering may lead to entry-level jobs or a better career path after you have completed a masters program. Some jobs may also require licensure by the state. For their first few year, nuclear engineers usually work under an experienced engineer. They gain experience and take responsibility.
Average salary of a nuclear engineer who has a master's degree
Consider the salaries for nuclear engineers if your career is in this field. You can work at any nuclear power facility, but it is more common to work as an office worker. Those interested in a career in nuclear power generation will work in power plants and are likely to work with electrical and mechanical engineers. They will need to integrate systems designed by these other professionals. Nuclear engineers are typically full-time workers and may even work more than their counterparts.
A nuclear engineer who has a Master's degree earns an average salary of $124,272 per annum, which is significantly more than the median income for all US workers. However, it is important to note that the salary ranges vary widely from position to position. For nuclear engineers with greater experience, the average annual salary can be $185,000. The average starting salary of nuclear engineers is $74,800. It is also among the highest in this field.
For a nuclear engineer, the starting salary is $40,000
To be a successful career in nuclear engineering you will need to understand the average starting pay. You need to have a strong education and a lot of work experience. Although nuclear engineers might experience steady career advancement, they have the option of switching to a related field. Nuclear engineers may also be involved in space exploration, manufacturing, and medical uses of radiological substances.
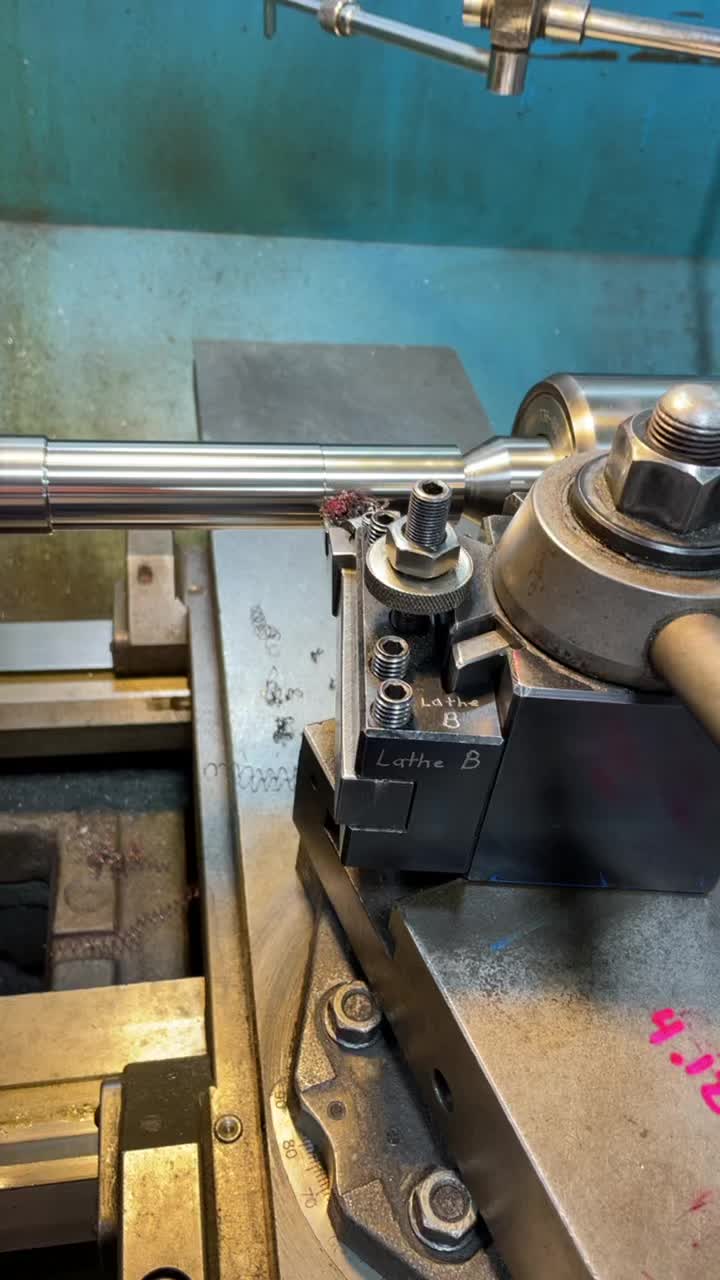
Although nuclear engineers are able to work in many different industries, their biggest employer is the federal government. These facilities are managed by the Office for Nuclear Regulation. Other employers in the field include construction, manufacturing, and scientific research and development. Future employment opportunities for nuclear engineers will increase as nuclear power is used more. However, the lack of graduates will reduce job prospects for those who have this degree. There are currently limited jobs available for nuclear engineers by the federal government, but many companies are now hiring these professionals.
FAQ
What does the term manufacturing industries mean?
Manufacturing Industries are businesses that produce products for sale. Consumers are those who purchase these products. These companies use various processes such as production, distribution, retailing, management, etc., to fulfill this purpose. They make goods from raw materials with machines and other equipment. This includes all types if manufactured goods.
What is the difference between a production planner and a project manager?
The main difference between a production planner and a project manager is that a project manager is usually the person who plans and organizes the entire project, whereas a production planner is mainly involved in the planning stage of the project.
What are the 7 Rs of logistics?
The 7R's of Logistics is an acronym for the seven basic principles of logistics management. It was created by the International Association of Business Logisticians and published in 2004 under its "Seven Principles of Logistics Management".
The acronym is made up of the following letters:
-
Responsible – ensure that all actions are legal and don't cause harm to anyone else.
-
Reliable: Have faith in your ability or the ability to honor any promises made.
-
Be responsible - Use resources efficiently and avoid wasting them.
-
Realistic – consider all aspects of operations, from cost-effectiveness to environmental impact.
-
Respectful - treat people fairly and equitably.
-
You are resourceful and look for ways to save money while increasing productivity.
-
Recognizable - provide customers with value-added services.
What is production plan?
Production Planning refers to the development of a plan for every aspect of production. This document aims to ensure that everything is planned and ready when you are ready to shoot. This document should include information about how to achieve the best results on-set. This includes shooting schedules, locations, cast lists, crew details, and equipment requirements.
First, you need to plan what you want to film. You might have an idea of where you want to film, or you may have specific locations or sets in mind. Once you have determined your scenes and locations, it is time to start figuring out the elements that you will need for each scene. You might decide you need a car, but not sure what make or model. If this is the case, you might start searching online for car models and then narrow your options by selecting from different makes.
After you have selected the car you want, you can begin to think about additional features. You might need to have people in the front seats. Or perhaps you need someone walking around the back of the car? You might want to change your interior color from black and white. These questions will help determine the look and feel you want for your car. You can also think about the type of shots you want to get. Are you going to be shooting close-ups? Or wide angles? Maybe you want the engine or the steering wheels to be shown. These factors will help you determine which car style you want to film.
Once you have all the information, you are ready to create a plan. You will know when you should start and when you should finish shooting. You will need to know when you have to be there, what time you have to leave and when your return home. This way, everyone knows what they need to do and when. If you need to hire extra staff, you can make sure you book them in advance. You don't want to hire someone who won't show up because he didn't know.
Your schedule will also have to be adjusted to reflect the number of days required to film. Some projects can be completed in a matter of days or weeks. Others may take several days. When you are creating your schedule, you should always keep in mind whether you need more than one shot per day or not. Multiple takes of the same location will lead to higher costs and take more time. If you aren't sure whether you need multiple shots, it is best to take fewer photos than you would like.
Budgeting is another crucial aspect of production plan. As it will allow you and your team to work within your financial means, setting a realistic budget is crucial. You can always lower the budget if you encounter unexpected problems. However, you shouldn't overestimate the amount of money you will spend. Underestimating the cost will result in less money after you have paid for other items.
Production planning is a very detailed process, but once you understand how everything works together, it becomes easier to plan future projects.
How can overproduction in manufacturing be reduced?
In order to reduce excess production, you need to develop better inventory management methods. This would reduce time spent on activities such as purchasing, stocking, and maintaining excess stock. This could help us free up our time for other productive tasks.
A Kanban system is one way to achieve this. A Kanban board can be used to monitor work progress. Kanban systems are where work items travel through a series of states until reaching their final destination. Each state is assigned a different priority.
To illustrate, work can move from one stage or another when it is complete enough for it to be moved to a new stage. It is possible to keep a task in the beginning stages until it gets to the end.
This allows work to move forward and ensures that no work is missed. With a Kanban board, managers can see exactly how much work is being done at any given moment. This data allows them adjust their workflow based upon real-time data.
Lean manufacturing is another option to control inventory levels. Lean manufacturing is about eliminating waste from all stages of the production process. Anything that doesn't add value to the product is considered waste. Some common types of waste include:
-
Overproduction
-
Inventory
-
Packaging not required
-
Exceed materials
These ideas will help manufacturers increase efficiency and lower costs.
Statistics
- (2:04) MTO is a production technique wherein products are customized according to customer specifications, and production only starts after an order is received. (oracle.com)
- In the United States, for example, manufacturing makes up 15% of the economic output. (twi-global.com)
- It's estimated that 10.8% of the U.S. GDP in 2020 was contributed to manufacturing. (investopedia.com)
- According to the United Nations Industrial Development Organization (UNIDO), China is the top manufacturer worldwide by 2019 output, producing 28.7% of the total global manufacturing output, followed by the United States, Japan, Germany, and India.[52][53] (en.wikipedia.org)
- According to a Statista study, U.S. businesses spent $1.63 trillion on logistics in 2019, moving goods from origin to end user through various supply chain network segments. (netsuite.com)
External Links
How To
How to Use 5S for Increasing Productivity in Manufacturing
5S stands as "Sort", Set In Order", Standardize", Separate" and "Store". Toyota Motor Corporation was the first to develop the 5S approach in 1954. It assists companies in improving their work environments and achieving higher efficiency.
This method has the basic goal of standardizing production processes to make them repeatable. This means that every day tasks such cleaning, sorting/storing, packing, and labeling can be performed. Through these actions, workers can perform their jobs more efficiently because they know what to expect from them.
Implementing 5S involves five steps: Sort, Set in Order, Standardize Separate, Store, and Each step requires a different action, which increases efficiency. Sorting things makes it easier to find them later. When you arrange items, you place them together. Then, after you separate your inventory into groups, you store those groups in containers that are easy to access. Make sure everything is correctly labeled when you label your containers.
This process requires employees to think critically about how they do their job. Employees must be able to see why they do what they do and find a way to achieve them without having to rely on their old methods. In order to use the 5S system effectively, they must be able to learn new skills.
The 5S method not only increases efficiency but also boosts morale and teamwork. They are more motivated to achieve higher efficiency levels as they start to see improvement.