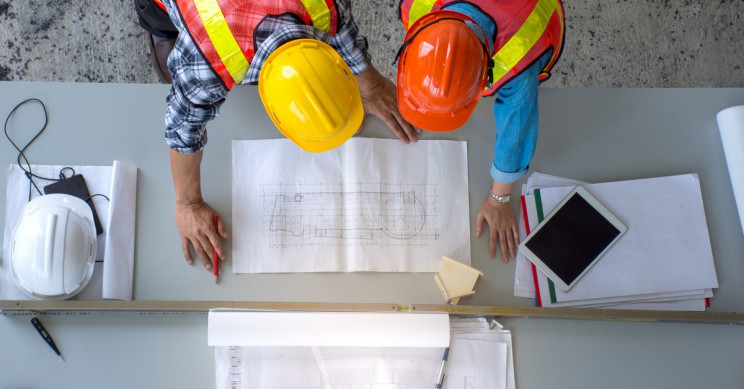
Supply chain management is crucial to maintaining a solid operation, regardless of whether you are a small businessperson or the enterprise arm for a major corporation. There are many risks that can occur, from the seemingly mundane to the potentially disastrous. You can prevent losses by creating a plan and following the implementation strategy.
Data sharing is one of the most critical aspects of a supply-chain continuity plan. If your organization relies on a single supplier, you are prone to vendor failures and supplier dispute. However, if your company is part of a multi-supplier consortium, you are more likely to avoid supply disruptions. It may also be possible to negotiate with another supplier.
Similarly, if your company has a complex network of contractors, you are at greater risk of vendor fraud, duplicate billing, and improper related-party billing. These risks can be mitigated by creating a risk assessment strategy that includes a complete assessment and assessment of all your suppliers, partners, as well other tier-1 components.
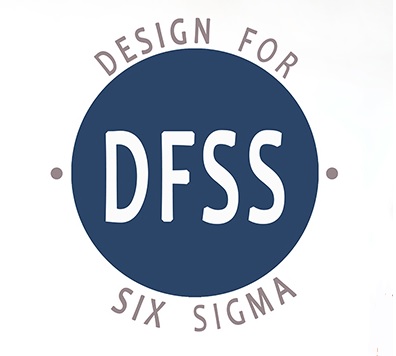
Before you can develop a supply-chain risk management program, it is essential to identify the most important elements of a supply network. Then quantify and measure them and then design an action plan. These items should be combined with a few additional. Proactive monitoring systems are the most important aspect. This is a system that provides real-time and accurate information to your executives about supply chain risk. Real-time supply chain risk tracking will help you make informed decisions and respond promptly.
As you begin assessing and quantifying your risks, it is essential to keep in mind that your supply chain's resilience is a function of governance. In particular, you need to consider the role of stakeholders. For example, the supplier bankruptcy that led to a supply-chain disruption in the pharmaceutical industry could have been avoided if the company had properly scorecarded its suppliers.
A well-planned plan is essential for minimizing supply chain crises. It isn't always easy to implement the right contingency planning. Many companies fail to plan enough contingency strategies for each risk they manage. The most important potential consequences should be considered when developing these plans.
The PPPR or preventive, preparedness, response, and recovery methodology is a worldwide standard for supply chain risk management. It is a solid approach that will improve your ability to react to supply-chain disruptions and can be used with other strategies to protect you organization from them. Using a PPPR guide to your organization can mean the difference between survival and success in today's market.
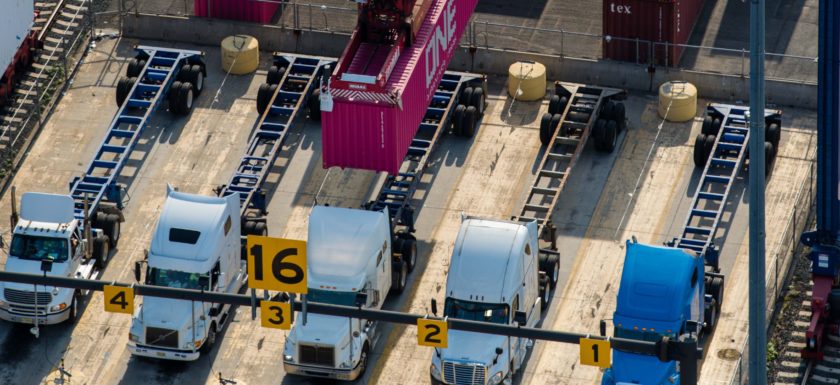
Get the right data from suppliers to understand their history, and what they can offer. This information will help you to make better decisions whether you are trying to increase your sourcing efforts or just tweaking your current processes. You can give your insurers the right premiums by using reliable data.
FAQ
Is there anything we should know about Manufacturing Processes prior to learning about Logistics.
No. No. However, knowing about manufacturing processes will definitely give you a better understanding of how logistics works.
What is the responsibility of a manufacturing manager?
Manufacturing managers must ensure that manufacturing processes are efficient, effective, and cost-effective. They must also be alert to any potential problems and take appropriate action.
They should also be able communicate with other departments, such as sales or marketing.
They must also keep up-to-date with the latest trends in their field and be able use this information to improve productivity and efficiency.
What can I do to learn more about manufacturing?
Hands-on experience is the best way to learn more about manufacturing. However, if that's not possible, you can always read books or watch educational videos.
Statistics
- Job #1 is delivering the ordered product according to specifications: color, size, brand, and quantity. (netsuite.com)
- You can multiply the result by 100 to get the total percent of monthly overhead. (investopedia.com)
- Many factories witnessed a 30% increase in output due to the shift to electric motors. (en.wikipedia.org)
- According to the United Nations Industrial Development Organization (UNIDO), China is the top manufacturer worldwide by 2019 output, producing 28.7% of the total global manufacturing output, followed by the United States, Japan, Germany, and India.[52][53] (en.wikipedia.org)
- In 2021, an estimated 12.1 million Americans work in the manufacturing sector.6 (investopedia.com)
External Links
How To
Six Sigma in Manufacturing
Six Sigma is defined as "the application of statistical process control (SPC) techniques to achieve continuous improvement." Motorola's Quality Improvement Department, Tokyo, Japan, developed it in 1986. Six Sigma is a method to improve quality through standardization and elimination of defects. Many companies have adopted Six Sigma in recent years because they believe that there are no perfect products and services. The main goal of Six Sigma is to reduce variation from the mean value of production. You can calculate the percentage of deviation from the norm by taking a sample of your product and comparing it to the average. If it is too large, it means that there are problems.
Understanding the dynamics of variability within your business is the first step in Six Sigma. Once you've understood that, you'll want to identify sources of variation. It is important to identify whether the variations are random or systemic. Random variations occur when people do mistakes. Symmetrical variations are caused due to factors beyond the process. Random variations would include, for example, the failure of some widgets to fall from the assembly line. If however, you notice that each time you assemble a widget it falls apart in exactly the same spot, that is a problem.
Once you have identified the problem, you can design solutions. You might need to change the way you work or completely redesign the process. Once you have implemented the changes, it is important to test them again to ensure they work. If they don't work you need to rework them and come up a better plan.