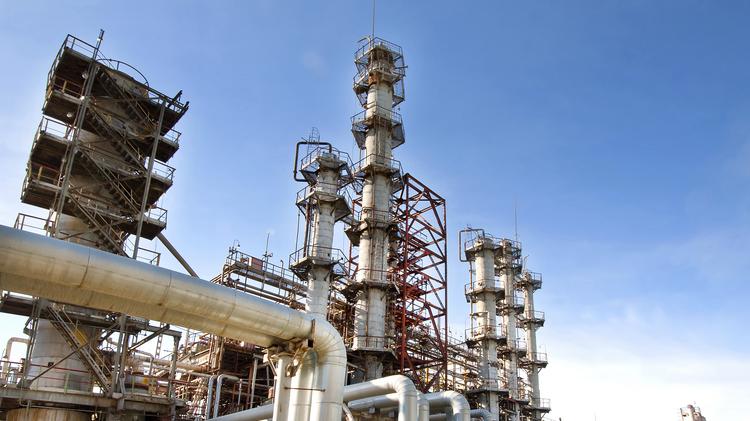
Civil engineers design and build infrastructure such a roads, railways, airports, bridges, harbours, dams, etc. They design and manage irrigation, water and sewerage system projects.
A career as a Civil Engineer requires certain skills and an education commitment. Students who wish to enter this field need a bachelor's in civil engineering, or another related field such as business administration or construction. A master's is held by about one fifth of civil engineers. This increases the chances that you will get a position as a junior engineer. Senior engineers may need a license from ABET.
A bachelor's in civil engineering or a closely-related discipline like construction management is usually required for entry-level positions. Most civil engineering programs take between four and five years to finish. However, many schools offer special programs which allow you to earn your degree for less money.
Graduates of civil engineering can take on a number of different roles. They may work as design engineers or project managers. They typically start with a graduate training program where they will work under an experienced expert to develop their skill. After gaining more experience, engineers can progress to full-time roles and eventually become lead engineers.
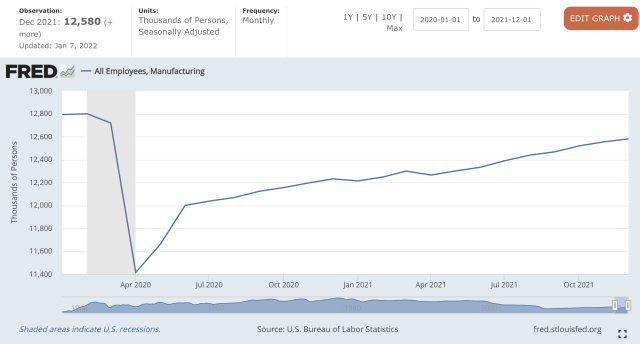
Careers as civil engineers can be challenging and rewarding, with lots of opportunities for growth. These careers are available in many industries including transportation, energy production, manufacturing, and building construction.
Employers want candidates with excellent communication, creativity and critical thinking skills. These skills are essential to solving engineering problems and improving technical processes for employers.
Your projects often require you to supervise construction. Leadership and teamwork skills will be important. You'll need to be able to communicate with your team members and vendors about issues that arise, so you can resolve them quickly and efficiently.
As the civil engineering profession is constantly evolving, it's essential to stay on top of trends and new regulations. You can keep up by pursuing continuing education or joining a professional association.
It is also important to have good decisionmaking skills for this position. You will need to make budgeting decisions and balance safety concerns with your own knowledge.
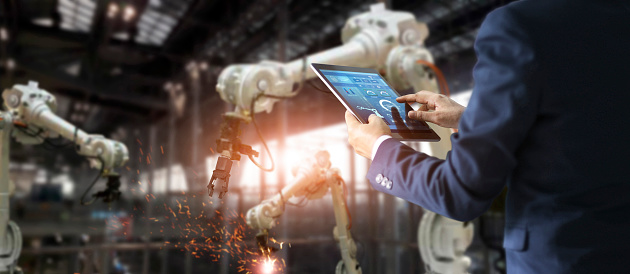
It is essential that you have the right education and training to be a successful civil engineer. You must also prove yourself on the job through completing projects, meeting deadlines and demonstrating your professionalism. This includes communicating with clients, coworkers and contractors.
This career will require a solid understanding of mathematics, physics and the ability think creatively. You will also need to have the ability to analyze data, and to present your findings effectively.
The salary of a civil engineer varies widely depending on what you do and where you are located. California, Texas, Florida and other states offer the highest salaries in this field. Alaska, Rhode Island & Wyoming are other states where civil engineers can earn high salaries.
FAQ
Can we automate some parts of manufacturing?
Yes! Automation has been around since ancient times. The Egyptians discovered the wheel thousands and years ago. Robots are now used to assist us in assembly lines.
Robotics is used in many manufacturing processes today. These include:
-
Assembly line robots
-
Robot welding
-
Robot painting
-
Robotics inspection
-
Robots create products
Automation could also be used to improve manufacturing. 3D printing makes it possible to produce custom products in a matter of days or weeks.
What are the 7 Rs of logistics management?
The acronym 7Rs of Logistics refers to the seven core principles of logistics management. It was created by the International Association of Business Logisticians and published in 2004 under its "Seven Principles of Logistics Management".
The following letters make up the acronym:
-
Responsible – ensure that all actions are legal and don't cause harm to anyone else.
-
Reliable - Have confidence in your ability to fulfill all of your commitments.
-
Use resources effectively and sparingly.
-
Realistic - Consider all aspects of operations, including environmental impact and cost effectiveness.
-
Respectful - Treat people fairly and equitably
-
Reliable - Find ways to save money and increase your productivity.
-
Recognizable - provide customers with value-added services.
What is the difference between manufacturing and logistics
Manufacturing is the process of creating goods from raw materials by using machines and processes. Logistics covers all aspects involved in managing supply chains, including procurement and production planning. Logistics and manufacturing are often referred to as one thing. It encompasses both the creation of products and their delivery to customers.
What does manufacturing industry mean?
Manufacturing Industries refers to businesses that manufacture products. Consumers are those who purchase these products. To accomplish this goal, these companies employ a range of processes including distribution, sales, management, and production. They manufacture goods from raw materials using machines and other equipment. This includes all types manufactured goods such as clothing, building materials, furniture, electronics, tools and machinery.
How can manufacturing excess production be decreased?
The key to reducing overproduction lies in developing better ways to manage inventory. This would reduce the time spent on unproductive activities like purchasing, storing and maintaining excess stock. We could use these resources to do other productive tasks.
One way to do this is to adopt a Kanban system. A Kanban Board is a visual display that tracks work progress. A Kanban system allows work items to move through several states before reaching their final destination. Each state represents a different priority.
To illustrate, work can move from one stage or another when it is complete enough for it to be moved to a new stage. However, if a task is still at the beginning stages, it will remain so until it reaches the end of the process.
This allows for work to continue moving forward, while also ensuring that there is no work left behind. Managers can view the Kanban board to see how much work they have done. This allows them the ability to adjust their workflow using real-time data.
Lean manufacturing can also be used to reduce inventory levels. Lean manufacturing focuses on eliminating waste throughout the entire production chain. Waste includes anything that does not add value to the product. There are several types of waste that you might encounter:
-
Overproduction
-
Inventory
-
Unnecessary packaging
-
Excess materials
These ideas will help manufacturers increase efficiency and lower costs.
Statistics
- According to the United Nations Industrial Development Organization (UNIDO), China is the top manufacturer worldwide by 2019 output, producing 28.7% of the total global manufacturing output, followed by the United States, Japan, Germany, and India.[52][53] (en.wikipedia.org)
- (2:04) MTO is a production technique wherein products are customized according to customer specifications, and production only starts after an order is received. (oracle.com)
- Many factories witnessed a 30% increase in output due to the shift to electric motors. (en.wikipedia.org)
- In 2021, an estimated 12.1 million Americans work in the manufacturing sector.6 (investopedia.com)
- [54][55] These are the top 50 countries by the total value of manufacturing output in US dollars for its noted year according to World Bank.[56] (en.wikipedia.org)
External Links
How To
How to Use 5S to Increase Productivity in Manufacturing
5S stands for "Sort", 'Set In Order", 'Standardize', & Separate>. Toyota Motor Corporation created the 5S methodology in 1954. It helps companies achieve higher levels of efficiency by improving their work environment.
This approach aims to standardize production procedures, making them predictable, repeatable, and easily measurable. Cleaning, sorting and packing are all done daily. Through these actions, workers can perform their jobs more efficiently because they know what to expect from them.
Five steps are required to implement 5S: Sort, Set In Order, Standardize. Separate. Each step is a different action that leads to greater efficiency. Sorting things makes it easier to find them later. When you arrange items, you place them together. You then organize your inventory in groups. Labeling your containers will ensure that everything is correctly labeled.
This requires employees to critically evaluate how they work. Employees should understand why they do the tasks they do, and then decide if there are better ways to accomplish them. To be successful in the 5S system, employees will need to acquire new skills and techniques.
The 5S method increases efficiency and morale among employees. They are more motivated to achieve higher efficiency levels as they start to see improvement.