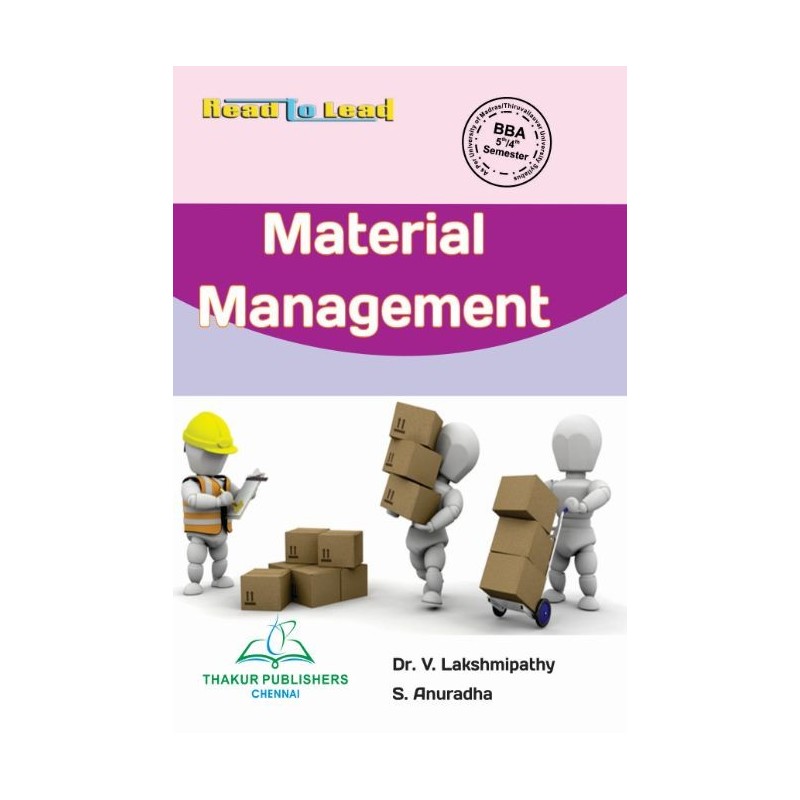
Across the industrial manufacturing industry, the Industrial Products & Services sector is facing intensified global competition, as well as a shortage of skilled workers. In the 2020s, the industrial manufacturing industry is facing a challenging landscape. This is due to increased supply-chain volatility. A comprehensive culture of innovation is required for the Industrial Products & Services sector to maximize growth in established markets while also maximizing growth opportunities in emerging markets.
According to Deloitte and Manufacturing Institute, the US manufacturing sector will be experiencing the greatest shortage in skilled workers since the beginning of history. This is because 2 million jobs are unfilled over the next ten-years. In order to prepare for the future, the industry must decide how it will enhance its digital and innovation capabilities. Deloitte's Industrial Manufacturing Team can help manufacturers navigate the landscape of the industry.
As the fourth industrial revolution continues its disruption in the manufacturing sector, the industry must prepare employees for a future that includes networking within the internet of things' as well as digital transformation. The Industrial Manufacturing team has extensive experience in creating innovative management models that are grounded on industry-specific knowledge and industry expertise. It also provides a wide range of digital transformation services that can help manufacturers to thrive in a world of digital disruption.
The Deloitte study was based on extensive secondary data analysis and interviews with executives at manufacturing organizations of all sizes. Economic projections are also included in the research. The findings also highlight the importance of a diverse workforce. In particular, half of respondents said that adaptability to company values was key to their job happiness. Respondents also reported that more than one third believe employees must have a purpose for being satisfied at work. Executives also think that millennials value environmental awareness and are increasingly interested in climate change issues.
Deloitte has predicted that manufacturing GDP would grow moderately at 1.3 percentage points in 2020 using the Oxford Economic Model. However, the study notes that this level of growth is expected to be less than half of the rate seen in the past few years. Companies will need to reconsider their approach to supply chain security. Businesses will need to focus their efforts on other management initiatives such a greater resilience in operations. According to Deloitte research, manufacturers will probably be making decisions about work places and work practices.
Manufacturing companies need to create career pathways and build an inclusive culture to ensure they are ready for the future. Manufacturing efficiency can be improved and waste reduced by increasing resilience. Combining digital technologies with lean principles can help to reduce manufacturing variability.
As the US manufacturing industry continues to evolve, Deloitte has released a new report that explores diversity in manufacturing. Deloitte's "Beyond Reskilling" report discusses how diversity is essential to manufacturing's future, and it highlights the benefits of having a diverse workforce.
FAQ
What does it take to run a logistics business?
You need to have a lot of knowledge and skills to manage a successful logistic business. You must have good communication skills to interact effectively with your clients and suppliers. You need to understand how to analyze data and draw conclusions from it. You need to be able work under pressure and manage stressful situations. To improve efficiency, you must be innovative and creative. You must be a strong leader to motivate others and direct them to achieve organizational goals.
It is also important to be efficient and well organized in order meet deadlines.
What are the 7 Rs of logistics?
The acronym 7R's of Logistic is an acronym that stands for seven fundamental principles of logistics management. It was created by the International Association of Business Logisticians and published in 2004 under its "Seven Principles of Logistics Management".
The acronym consists of the following letters:
-
Responsible - to ensure that all actions are within the legal requirements and are not detrimental to others.
-
Reliable - You can have confidence that you will fulfill your promises.
-
Reasonable - make sure you use your resources well and don't waste them.
-
Realistic – consider all aspects of operations, from cost-effectiveness to environmental impact.
-
Respectful – Treat others fairly and equitably.
-
Responsive - Look for ways to save time and increase productivity.
-
Recognizable - Provide value-added services to customers
What are the products of logistics?
Logistics refers to all activities that involve moving goods from A to B.
They encompass all aspects transport, including packaging and loading, transporting, storage, unloading.
Logisticians make sure that the right product arrives at the right place at the correct time and in safe conditions. They assist companies with their supply chain efficiency through information on demand forecasts. Stock levels, production times, and availability.
They can also track shipments in transit and monitor quality standards.
Statistics
- [54][55] These are the top 50 countries by the total value of manufacturing output in US dollars for its noted year according to World Bank.[56] (en.wikipedia.org)
- In the United States, for example, manufacturing makes up 15% of the economic output. (twi-global.com)
- According to the United Nations Industrial Development Organization (UNIDO), China is the top manufacturer worldwide by 2019 output, producing 28.7% of the total global manufacturing output, followed by the United States, Japan, Germany, and India.[52][53] (en.wikipedia.org)
- Job #1 is delivering the ordered product according to specifications: color, size, brand, and quantity. (netsuite.com)
- Many factories witnessed a 30% increase in output due to the shift to electric motors. (en.wikipedia.org)
External Links
How To
How to Use the 5S to Increase Productivity In Manufacturing
5S stands as "Sort", Set In Order", Standardize", Separate" and "Store". Toyota Motor Corporation developed the 5S method in 1954. It allows companies to improve their work environment, thereby achieving greater efficiency.
This method aims to standardize production processes so that they are repeatable, measurable and predictable. This means that daily tasks such as cleaning and sorting, storage, packing, labeling, and packaging are possible. Because workers know what they can expect, this helps them perform their jobs more efficiently.
Implementing 5S involves five steps: Sort, Set in Order, Standardize Separate, Store, and Each step requires a different action, which increases efficiency. For example, when you sort things, you make them easy to find later. Once you have placed items in an ordered fashion, you will put them together. Once you have separated your inventory into groups and organized them, you will store these groups in easily accessible containers. Finally, when you label your containers, you ensure everything is labeled correctly.
Employees must be able to critically examine their work practices. Employees need to understand the reasons they do certain jobs and determine if there is a better way. They will need to develop new skills and techniques in order for the 5S system to be implemented.
The 5S Method not only improves efficiency, but it also helps employees to be more productive and happier. They are more motivated to achieve higher efficiency levels as they start to see improvement.