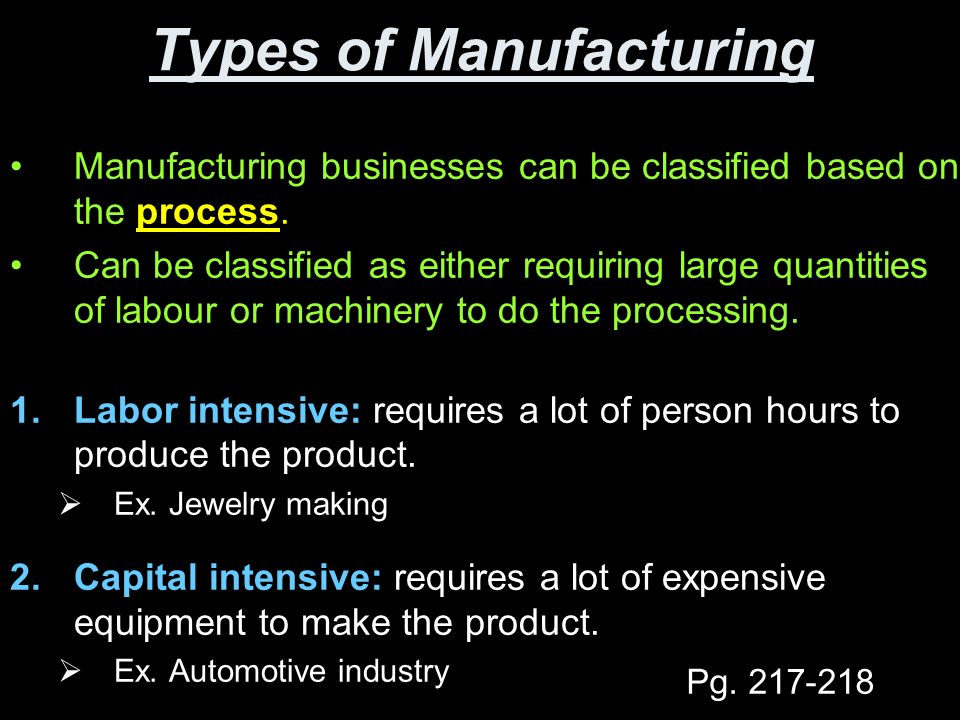
The company's manufacturing director is responsible for overseeing the entire production process. As they are responsible for managing the entire production process, their role is critical. The ideal candidate should have extensive manufacturing experience and be proficient in new technologies in order to succeed in this position. Some examples of such technologies include robotics and 3D printing. An asset to any company is a director who can keep up with new technologies. As the manufacturing industry continues to evolve, the director's role will become increasingly complex, as he or she must work with the engineering and operations departments, as well as putting a greater emphasis on quality control within the manufacturing plant.
Director of manufacturing: Salary
The compensation for a Director in Manufacturing will vary depending on the location they work. Many directors are compensated in the low six-figure range, and some earn significantly more than others. The salary of a Director of Manufacturing may also vary significantly based on years of experience and education. Consider these factors when determining how much you will earn in your local area.
Although the salary of a Director of Manufacturing is variable, it is generally higher for those with more experience. Like many other positions, salary can be affected by the cost of living or where you live. Living in a big city will result in higher salaries. But, be aware that your salary might not reflect the cost of living. When the opportunity presents itself, it is important to be open to negotiations to obtain a higher wage.
A Director of Manufacturing Operations makes between $181,500 and $66,000 a year. The salary of a Director Manufacturing Operations is highly variable. It can vary by up 8% among different cities. Fremont, CA's director for manufacturing operations can earn between $128.493 and $164.500. This is significantly more than the average national salary. However, salaries for Director of Manufacturing Operations vary depending on location, experience, and company.
Education necessary
The director for manufacturing is responsible in managing a manufacturing plant and supervising the production process. Some of the duties of this position include hiring new employees, overseeing quality assurance, collaborating with designers, and meeting operations standards. A director in manufacturing typically reports directly to the senior management team. This person executes policies and sales initiatives. Candidates must have experience in manufacturing and communicate well. Each company has its own requirements regarding education for a manufacturing director.
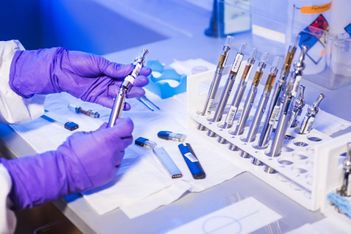
A graduate degree is not necessary for director of manufacturing jobs. However, you will be able to enhance your skill and knowledge by completing post-secondary education. An MBA program in industrial management or business administration is a great choice for this position, as it helps candidates to learn about management, economics, and organization. Ultimately, you will be responsible for managing a diverse group of people.
As a director in manufacturing you will work closely alongside engineers and designers during the product design phase. This stage is where you will evaluate new manufacturing processes and ensure high quality standards. As well as overseeing production, directors can also serve as coaches to employees. They mentor their employees in risk mitigation and best practices. A manufacturing director must not only oversee the production process but also be able to solve problems.
Experience required
For this position, you will need a bachelor's or master's degree in a related field. You also need to have five to ten years of work experience. For this position, manufacturing companies prefer to recruit internal employees. The ideal candidate must have a deep understanding of the manufacturing industry and its business goals. Employers may require a graduate degree. Additional training may be required for candidates in their chosen field.
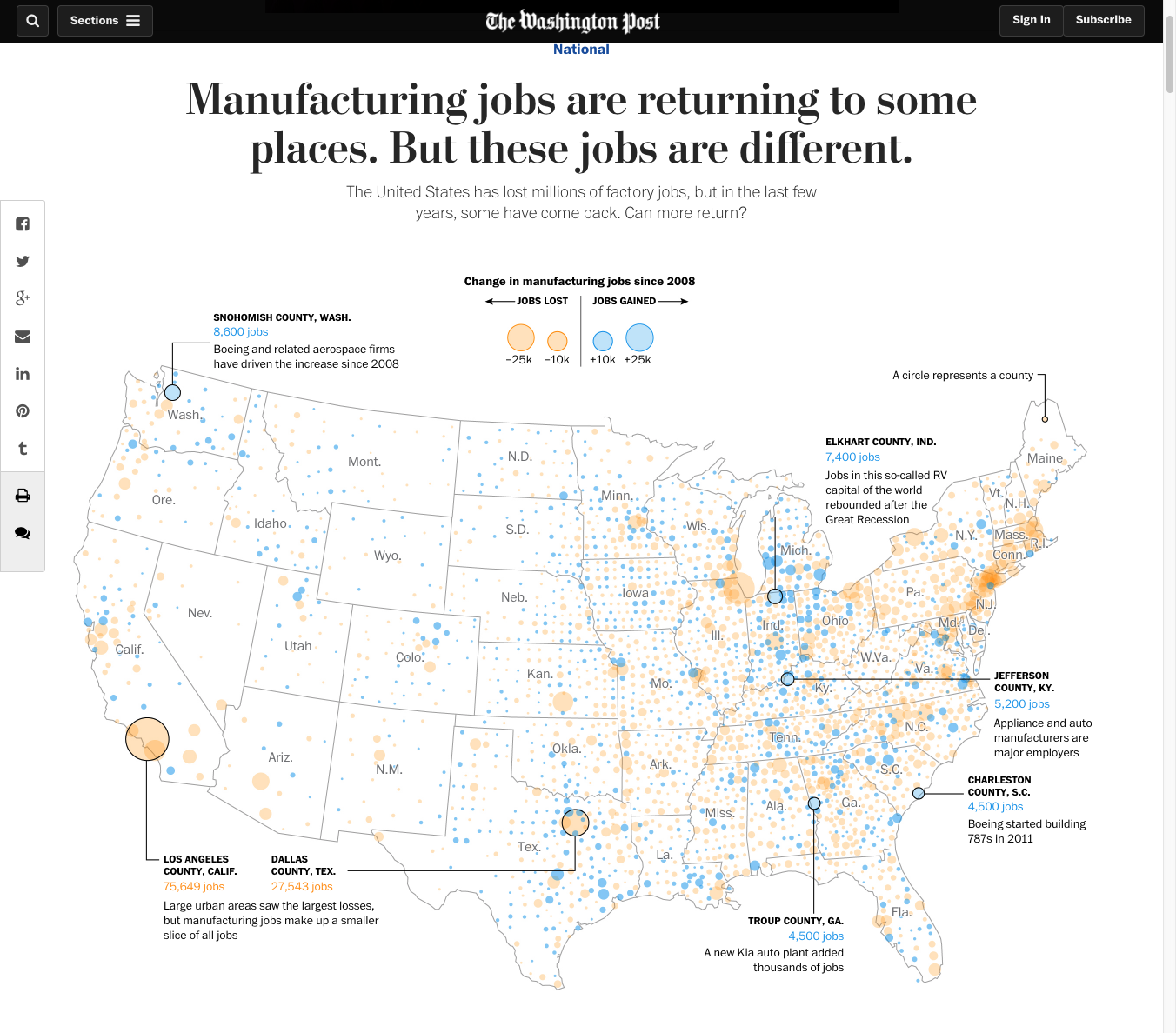
The director of manufacturing supervises the production process. This includes supervisors, engineers, workers, and supervisors. They may be responsible solving problems or finding a solution. They might also be responsible to develop and implement quality control programs. Directly reports to the top management of the manufacturing organization, the director of manufacturing. Experience in manufacturing is an absolute must. This position can be made more successful if you have experience in manufacturing management.
It is important to have experience as a director in manufacturing. Directors must have at least 10 years of relevant experience in a manufacturing environment. These individuals may have had previous experience as managers or technicians. They should also possess strong communication skills. Also, a director of manufacturing needs to have a good understanding of business strategy. Finally, a director of manufacturing must be able to work effectively with other departments within the organization. In this capacity, the director oversees the production process and ensures that it meets the highest quality standards.
FAQ
What skills are required to be a production manager?
A production planner must be organized, flexible, and able multitask to succeed. It is also important to be able communicate with colleagues and clients.
What are the essential elements of running a logistics firm?
It takes a lot of skills and knowledge to run a successful logistics business. Good communication skills are essential to effectively communicate with your suppliers and clients. It is important to be able to analyse data and draw conclusions. You need to be able work under pressure and manage stressful situations. You must be creative and innovative to develop new ideas to improve efficiency. You need to have strong leadership qualities to motivate team members and direct them towards achieving organizational goals.
You must be organized to meet tight deadlines.
Why automate your warehouse
Modern warehousing is becoming more automated. With the rise of ecommerce, there is a greater demand for faster delivery times as well as more efficient processes.
Warehouses should be able adapt quickly to new needs. Technology is essential for warehouses to be able to adapt quickly to changing needs. Automating warehouses is a great way to save money. Here are some reasons why it's worth investing in automation:
-
Increases throughput/productivity
-
Reduces errors
-
Increases accuracy
-
Boosts safety
-
Eliminates bottlenecks
-
Companies can scale up more easily
-
Workers are more productive
-
Gives you visibility into all that is happening in your warehouse
-
Enhances customer experience
-
Improves employee satisfaction
-
Reduces downtime and improves uptime
-
Ensures quality products are delivered on time
-
Removing human error
-
Assure compliance with regulations
What are the 7 Rs of logistics management?
The acronym 7R's for Logistics stands to represent the seven basic principles in logistics management. It was developed by International Association of Business Logisticians (IABL), and published as part of their "Seven Principles of Logistics Management Series" in 2004.
The following letters form the acronym:
-
Responsible - to ensure that all actions are within the legal requirements and are not detrimental to others.
-
Reliable – have faith in your ability and capability to keep promises.
-
Use resources effectively and sparingly.
-
Realistic – Consider all aspects, including cost-effectiveness as well as environmental impact.
-
Respectful – Treat others fairly and equitably.
-
You are resourceful and look for ways to save money while increasing productivity.
-
Recognizable provides value-added products and services to customers
What are the 4 types manufacturing?
Manufacturing is the process that transforms raw materials into useful products. It can involve many activities like designing, manufacturing, testing packaging, shipping, selling and servicing.
How can I find out more about manufacturing?
Practical experience is the best way of learning about manufacturing. However, if that's not possible, you can always read books or watch educational videos.
Statistics
- Job #1 is delivering the ordered product according to specifications: color, size, brand, and quantity. (netsuite.com)
- According to a Statista study, U.S. businesses spent $1.63 trillion on logistics in 2019, moving goods from origin to end user through various supply chain network segments. (netsuite.com)
- You can multiply the result by 100 to get the total percent of monthly overhead. (investopedia.com)
- In the United States, for example, manufacturing makes up 15% of the economic output. (twi-global.com)
- Many factories witnessed a 30% increase in output due to the shift to electric motors. (en.wikipedia.org)
External Links
How To
Six Sigma and Manufacturing
Six Sigma is "the application statistical process control (SPC), techniques for continuous improvement." It was developed by Motorola's Quality Improvement Department at their plant in Tokyo, Japan, in 1986. The basic idea behind Six Sigma is to improve quality by improving processes through standardization and eliminating defects. Many companies have adopted this method in recent years. They believe there is no such thing a perfect product or service. Six Sigma's primary goal is to reduce variation from the average value of production. If you take a sample and compare it with the average, you will be able to determine how much of the production process is different from the norm. If it is too large, it means that there are problems.
Understanding the dynamics of variability within your business is the first step in Six Sigma. Once you understand that, it is time to identify the sources of variation. Also, you will need to identify the sources of variation. Random variations occur when people make mistakes; systematic ones are caused by factors outside the process itself. You could consider random variations if some widgets fall off the assembly lines. But if you notice that every widget you make falls apart at the exact same place each time, this would indicate that there is a problem.
Once you've identified where the problems lie, you'll want to design solutions to eliminate those problems. You might need to change the way you work or completely redesign the process. To verify that the changes have worked, you need to test them again. If they don't work you need to rework them and come up a better plan.