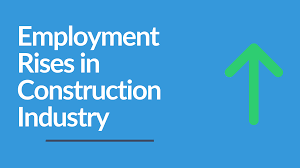
Six-Sigma is a complementary approach to improving processes. Although they both have the same tools for problem solving, each has its strengths and weaknesses. Six-Sigma refers to a statistical control technique. Lean, on the other hand, starts with the assumption that a product should add value to its customers, not just make it. Lean is about reducing waste and improving the quality of products as they are being made.
Problem solving in PDCA
There are some differences between PDCA and DMAIC problem solving, but both are based on the DMAIC approach. The PDCA cycle needs more planning and analysis. PDCA is not as effective as DMAIC for urgent problems. This approach requires a lead problem-solver with technical skills. Six Sigma will require a problem-solving team lead who is a Six Sigma "green belt" certified practitioner.
Six Sigma uses a cycle introduced by W. Edwards Deming in the 1950s to solve problems. Its creators intended to use it in conjunction with continuous improvement methods to help rebuild Japan's industries. In the P (Plan) stage, real data must be gathered, and a clear mission statement must be created. After the PDCA phase, the team must agree on a solution.
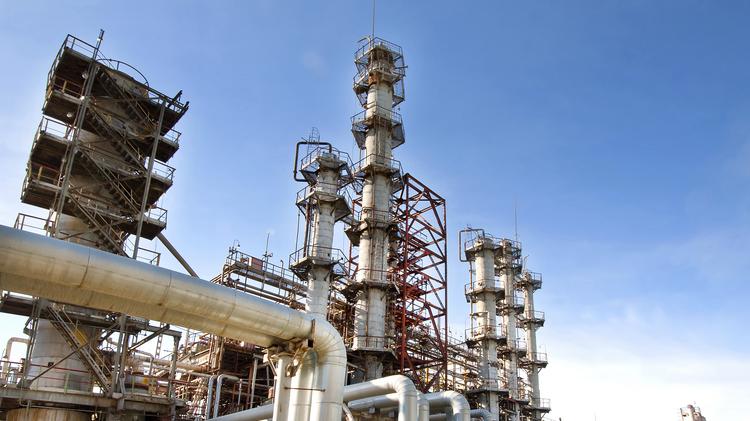
Process maps
A key difference between Lean and Six Sigma processes maps is how each approach describes the processes. Both methods focus on defining the process in detail but each approach focuses more on different aspects. Lean is a method of mapping actual processes, not standard operating protocols. When creating process maps, consider major activities, decisions, and sources of approval. Include areas where multiple methods are used and factors that could hinder members. You should carefully match the roles and go through the process flow.
A process map should include steps, symbols, and arrows to show the flow of a process. To ensure that each process accurately depicts the actual process, several people should review it. It should also contain information about the date and who to call if you have any questions. Overall, process maps are a good way to improve a process. However, they can be complicated.
Analyse Cause and Effect
Six Sigma, lean project management techniques are based on statistical analysis. The Cause and Effect Matrix, also known as the Cause and Effect Matrix (CAE), links each step of a process to its inputs and outputs. Customers' requirements are listed in order they are most important to them. Inputs and outputs are then ranked according to their impact on the outcome. It is important to determine the ranking of key process input variables.
Each technique offers a different set of benefits. Lean Six Sigma employs a process improvement method that is based upon Frederick Winslow Taylor’s Principles of Scientific Management. Taylor saw business processes as interconnected processes and workflows. Taylor advocated reducing variation and also minimizing waste. Six-Sigma (and lean) are complementary in the effort to reduce waste.
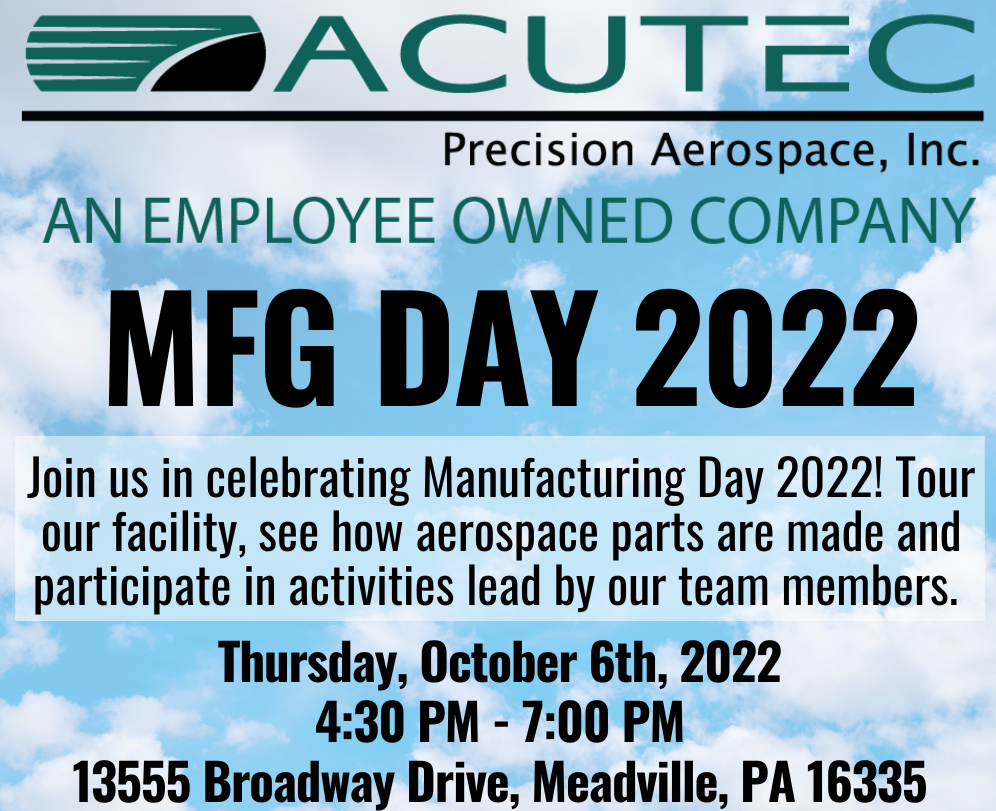
Eliminating Variation
Variability is a normal part of any manufacturing process. This variability can create uncertainty in the result. It is important to maintain consistency in order to deliver professional results. Six Sigma and Lean manufacturing methods strive to eliminate variation. Some amount of variation is fine, but too much leads to repairs, rework, and possibly even out-of-business consequences. It is important to determine the root causes of variation in order to address it.
You should first look at decision points for variations. Process maps identify decision points, which are represented by diamonds. Six Sigma teams have the ability to identify decision points and start eliminating variation. This information can be obtained from the Six Sigma team or the process owner. The Six Sigma group cannot focus on a process that is not governed by a standard process if it's owner. The Six Sigma team may not have enough technical capacity to modify the process map in this instance.
FAQ
What kind of jobs are there in logistics?
There are different kinds of jobs available in logistics. Some examples are:
-
Warehouse workers - They load and unload trucks and pallets.
-
Transport drivers - These are people who drive trucks and trailers to transport goods or perform pick-ups.
-
Freight handlers - They sort and pack freight in warehouses.
-
Inventory managers: They are responsible for the inventory and management of warehouses.
-
Sales representatives: They sell products to customers.
-
Logistics coordinators - They plan and organize logistics operations.
-
Purchasing agents - They purchase goods and services needed for company operations.
-
Customer service representatives – They answer emails and phone calls from customers.
-
Ship clerks - They issue bills and process shipping orders.
-
Order fillers - They fill orders based on what is ordered and shipped.
-
Quality control inspectors are responsible for inspecting incoming and outgoing products looking for defects.
-
Other - Logistics has many other job opportunities, including transportation supervisors, logistics specialists, and cargo specialists.
Why should you automate your warehouse?
Modern warehouses have become more dependent on automation. E-commerce has increased the demand for quicker delivery times and more efficient processes.
Warehouses need to adapt quickly to meet changing needs. To do so, they must invest heavily in technology. The benefits of automating warehouses are numerous. Here are some reasons why it's worth investing in automation:
-
Increases throughput/productivity
-
Reduces errors
-
Increases accuracy
-
Safety Boosts
-
Eliminates bottlenecks
-
This allows companies to scale easily
-
Makes workers more efficient
-
The warehouse can be viewed from all angles.
-
Enhances customer experience
-
Improves employee satisfaction
-
Reducing downtime and increasing uptime
-
You can be sure that high-quality products will arrive on time
-
Eliminates human error
-
Assure compliance with regulations
What are the 7 R's of logistics?
The acronym 7R's for Logistics stands to represent the seven basic principles in logistics management. It was published in 2004 by the International Association of Business Logisticians as part of their "Seven Principles of Logistics Management" series.
The following letters make up the acronym:
-
Responsive - ensure all actions are legal and not harmful to others.
-
Reliable – have faith in your ability and capability to keep promises.
-
Be responsible - Use resources efficiently and avoid wasting them.
-
Realistic - Take into consideration all aspects of operations including cost-effectiveness, environmental impact, and other factors.
-
Respectful - show respect and treat others fairly and fairly
-
Be resourceful: Look for opportunities to save money or increase productivity.
-
Recognizable provides value-added products and services to customers
What is meant by manufacturing industries?
Manufacturing Industries are businesses that produce products for sale. Consumers are people who purchase these goods. To accomplish this goal, these companies employ a range of processes including distribution, sales, management, and production. They produce goods from raw materials by using machines and other machinery. This includes all types if manufactured goods.
What is the role and responsibility of a Production Planner?
A production planner ensures all aspects of the project are delivered on time, within budget, and within scope. A production planner ensures that the service and product meet the client's expectations.
What skills should a production planner have?
To become a successful production planner, you need to be organized, flexible, and able to multitask. Effective communication with clients and colleagues is essential.
Statistics
- In 2021, an estimated 12.1 million Americans work in the manufacturing sector.6 (investopedia.com)
- Many factories witnessed a 30% increase in output due to the shift to electric motors. (en.wikipedia.org)
- According to the United Nations Industrial Development Organization (UNIDO), China is the top manufacturer worldwide by 2019 output, producing 28.7% of the total global manufacturing output, followed by the United States, Japan, Germany, and India.[52][53] (en.wikipedia.org)
- [54][55] These are the top 50 countries by the total value of manufacturing output in US dollars for its noted year according to World Bank.[56] (en.wikipedia.org)
- It's estimated that 10.8% of the U.S. GDP in 2020 was contributed to manufacturing. (investopedia.com)
External Links
How To
How to Use Just-In-Time Production
Just-intime (JIT), which is a method to minimize costs and maximize efficiency in business process, is one way. It's the process of obtaining the right amount and timing of resources when you need them. This means that only what you use is charged to your account. Frederick Taylor developed the concept while working as foreman in early 1900s. He saw how overtime was paid to workers for work that was delayed. He concluded that if workers were given enough time before they start work, productivity would increase.
The idea behind JIT is that you should plan ahead and have everything ready so you don't waste money. It is important to look at your entire project from beginning to end and ensure that you have enough resources to handle any issues that may arise. You can anticipate problems and have enough equipment and people available to fix them. This will ensure that you don't spend more money on things that aren't necessary.
There are many JIT methods.
-
Demand-driven: This type of JIT allows you to order the parts/materials required for your project on a regular basis. This will allow for you to track the material that you have left after using it. This will allow to you estimate the time it will take for more to be produced.
-
Inventory-based: You stock materials in advance to make your projects easier. This allows you predict the amount you can expect to sell.
-
Project-driven: This approach involves setting aside sufficient funds to cover your project's costs. If you know the amount you require, you can buy the materials you need.
-
Resource-based: This is the most common form of JIT. Here, you allocate certain resources based on demand. For instance, if you have a lot of orders coming in, you'll assign more people to handle them. If there aren't many orders, you will assign fewer people.
-
Cost-based: This is similar to resource-based, except that here you're not just concerned about how many people you have but how much each person costs.
-
Price-based: This approach is very similar to the cost-based method except that you don't look at individual workers costs but the total cost of the company.
-
Material-based: This is very similar to cost-based but instead of looking at total costs of the company you are concerned with how many raw materials you use on an average.
-
Time-based JIT: A variation on resource-based JIT. Instead of focusing solely on the amount each employee costs, focus on how long it takes for the project to be completed.
-
Quality-based: This is yet another variation of resource-based JIT. Instead of worrying about the costs of each employee or how long it takes for something to be made, you should think about how quality your product is.
-
Value-based JIT : This is the newest type of JIT. In this case, you're not concerned with how well the products perform or whether they meet customer expectations. Instead, you are focused on adding value to the marketplace.
-
Stock-based is an inventory-based system that measures the number of items produced at any given moment. It is used when production goals are met while inventory is kept to a minimum.
-
Just-in time (JIT), planning: This is a combination JIT/supply chain management. It is the process that schedules the delivery of components within a short time of their order. It's important as it reduces leadtimes and increases throughput.