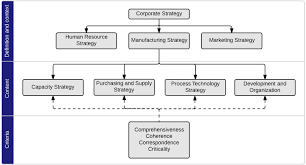
Supply chain management can be beneficial to all aspects a business. Customer satisfaction, cost savings and growth of the business are all factors that can be improved by an effective supply chain. The supply chain is a crucial factor for your business's success, regardless of its size.
The supply chain is the most neglected area of any business. However, it can have the greatest impact on the overall performance of your company and its ROI. Your supply chain will run more smoothly and efficiently if it is organized.
A successful supply chain management improves customer satisfaction by delivering exactly the right quantity and product at the right time. It also increases your profitability and improves the reputation of your business.
Companies have been trying to achieve greater speed and lower costs in the supply chain for a long time. They have invested heavily in new technologies, infrastructure and processes.
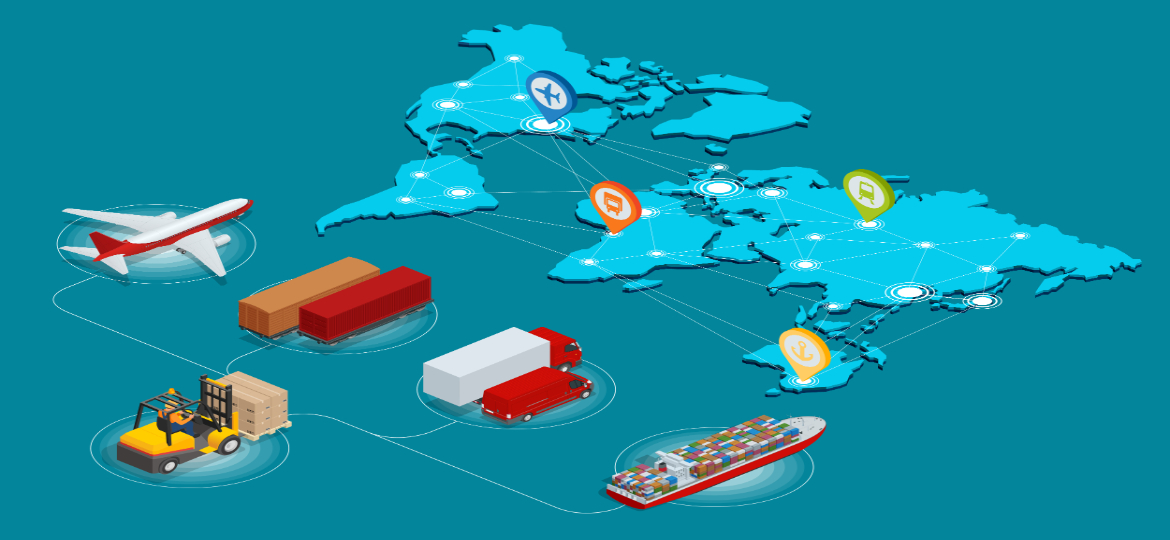
Numerous studies have shown how a firm's capability to manage the supply chain can impact its performance both financially and in terms of operations. They determine how efficiently the business runs and if it is capable of meeting its customers' needs and requirements.
If supply chain managers have the right training and a good understanding of their business from beginning to end, they can make the best decisions that will lead to savings. By working closely with all parties in the supply chain, they can improve customer satisfaction, increase profits and create better supplier relationships.
In a market with fast-paced markets and short product cycle times, the ability to quickly adapt is vital. Real-time management and analysis of raw inventories, transit times and supplier lead times is essential. The numbers must be accurate, granular and meaningful.
Supply chain management must be able to assess the financial impact that one missed delivery could have. They must also be able plan for back-up supplies.
These backup plans can help them overcome unexpected challenges. These plans will give them an advantage over rivals who lack flexible supply chain.
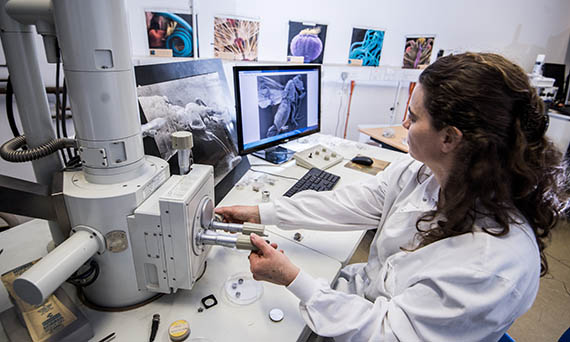
A well-organized, efficient supply chain is essential to a successful business. It ensures the consumer receives the right products at the right time. This will satisfy their needs and increase their loyalty.
It is very important to consider the different stages of a product's life cycle when deciding how to best align your supply chain with the manufacturing network and distribution system. This will allow you to develop optimal supply chain solutions for each product type, and at what stage of its lifecycle it is.
A good supply-chain strategy will make sure that the organisation is "fit for purpose" and can change from being flexible and responsive to efficient, low-cost and innovation driven.
The supply chain function's organizational design interacts with assets, technology, processes and people to support its business strategy. When these elements don't match, execution can be difficult and a business' supply chain could fail to deliver.
FAQ
What are the responsibilities of a production planner
Production planners make sure that every aspect of the project is delivered on-time, within budget, and within schedule. They also ensure that the product/service meets the client’s needs.
How is a production manager different from a producer planner?
The primary difference between a producer planner and a manager of a project is that the manager usually plans and organizes the whole project, while a production planner is only involved in the planning stage.
Why automate your warehouse
Modern warehousing has seen automation take center stage. E-commerce has increased the demand for quicker delivery times and more efficient processes.
Warehouses must adapt quickly to meet changing customer needs. Technology investment is necessary to enable warehouses to respond quickly to changing demands. Automation warehouses can bring many benefits. These are some of the benefits that automation can bring to warehouses:
-
Increases throughput/productivity
-
Reduces errors
-
Accuracy is improved
-
Safety is boosted
-
Eliminates bottlenecks
-
Allows companies to scale more easily
-
Workers are more productive
-
The warehouse can be viewed from all angles.
-
Enhances customer experience
-
Improves employee satisfaction
-
It reduces downtime, and increases uptime
-
You can be sure that high-quality products will arrive on time
-
Removing human error
-
It ensures compliance with regulations
What is the role of a manager in manufacturing?
A manufacturing manager must make sure that all manufacturing processes run smoothly and effectively. They should be alert for any potential problems in the company and react accordingly.
They should also be able and comfortable communicating with other departments like sales and marketing.
They should be informed about industry trends and be able make use of this information to improve their productivity and efficiency.
How can manufacturing reduce production bottlenecks?
To avoid production bottlenecks, ensure that all processes run smoothly from the moment you receive your order to the time the product ships.
This includes planning to meet capacity requirements and quality control.
Continuous improvement techniques such Six Sigma can help you achieve this.
Six Sigma is a management system used to improve quality and reduce waste in every aspect of your organization.
It is focused on creating consistency and eliminating variation in your work.
What are the four types of manufacturing?
Manufacturing refers to the transformation of raw materials into useful products by using machines and processes. It involves many different activities such as designing, building, testing, packaging, shipping, selling, servicing, etc.
Statistics
- Many factories witnessed a 30% increase in output due to the shift to electric motors. (en.wikipedia.org)
- According to the United Nations Industrial Development Organization (UNIDO), China is the top manufacturer worldwide by 2019 output, producing 28.7% of the total global manufacturing output, followed by the United States, Japan, Germany, and India.[52][53] (en.wikipedia.org)
- In the United States, for example, manufacturing makes up 15% of the economic output. (twi-global.com)
- According to a Statista study, U.S. businesses spent $1.63 trillion on logistics in 2019, moving goods from origin to end user through various supply chain network segments. (netsuite.com)
- (2:04) MTO is a production technique wherein products are customized according to customer specifications, and production only starts after an order is received. (oracle.com)
External Links
How To
How to use lean manufacturing in the production of goods
Lean manufacturing is a management style that aims to increase efficiency and reduce waste through continuous improvement. It was developed in Japan between 1970 and 1980 by Taiichi Ohno. TPS founder Kanji Tyoda gave him the Toyota Production System, or TPS award. The first book published on lean manufacturing was titled "The Machine That Changed the World" written by Michael L. Watkins and published in 1990.
Lean manufacturing, often described as a set and practice of principles, is aimed at improving the quality, speed, cost, and efficiency of products, services, and other activities. It emphasizes the elimination of defects and waste throughout the value stream. Lean manufacturing is called just-in-time (JIT), zero defect, total productive maintenance (TPM), or 5S. Lean manufacturing seeks to eliminate non-value added activities, such as inspection, work, waiting, and rework.
Lean manufacturing can help companies improve their product quality and reduce costs. Additionally, it helps them achieve their goals more quickly and reduces employee turnover. Lean manufacturing can be used to manage all aspects of the value chain. Customers, suppliers, distributors, retailers and employees are all included. Lean manufacturing is widely used in many industries. Toyota's philosophy is a great example of this. It has helped to create success in automobiles as well electronics, appliances and healthcare.
Five principles are the basis of lean manufacturing:
-
Define Value- Identify the added value your company brings to society. What makes you stand out from your competitors?
-
Reduce Waste – Eliminate all activities that don't add value throughout the supply chain.
-
Create Flow – Ensure that work flows smoothly throughout the process.
-
Standardize and simplify – Make processes as repeatable and consistent as possible.
-
Build relationships - Develop and maintain personal relationships with both your internal and external stakeholders.
Although lean manufacturing isn't a new concept in business, it has gained popularity due to renewed interest in the economy after the 2008 global financial crisis. Many businesses have adopted lean manufacturing techniques to help them become more competitive. Some economists even believe that lean manufacturing can be a key factor in economic recovery.
Lean manufacturing, which has many benefits, is now a standard practice in the automotive industry. These include higher customer satisfaction levels, reduced inventory levels as well as lower operating costs.
You can apply Lean Manufacturing to virtually any aspect of your organization. Because it makes sure that all value chains are efficient and effectively managed, Lean Manufacturing is particularly helpful for organizations.
There are three main types of lean manufacturing:
-
Just-in-Time Manufacturing (JIT): This type of lean manufacturing is commonly referred to as "pull systems." JIT refers to a system in which components are assembled at the point of use instead of being produced ahead of time. This approach reduces lead time, increases availability and reduces inventory.
-
Zero Defects Manufacturing: ZDM ensures that no defective units leave the manufacturing plant. If a part needs to be fixed during the assembly line, it should be repaired rather than scrapped. This is also true for finished products that require minor repairs before shipping.
-
Continuous Improvement (CI): CI aims to improve the efficiency of operations by continuously identifying problems and making changes in order to eliminate or minimize waste. It involves continuous improvement of processes, people, and tools.