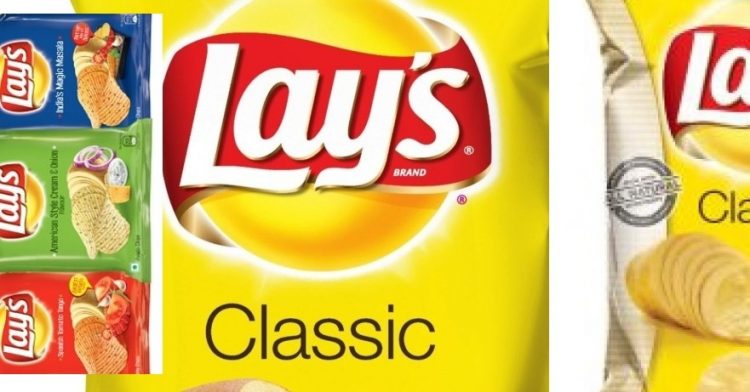
Lean 5 principles encourage the elimination and reduction of waste. Value stream mapping helps identify efficient and cost-effective activities. To eliminate waste, you must distinguish value-added (necessary), from non-value–added (unnecessary). By eliminating unnecessary steps, an efficient process is created that uses the least amount of time, energy, and materials. This ensures customers receive high quality products in a short time.
Valuable
The Value of the Lean 5 principles can help you improve your manufacturing process by eliminating waste. It is possible to create smooth flows from production to shipping by eliminating steps that are not adding value. This process helps reduce inventory, saves time and eliminates work in progress.
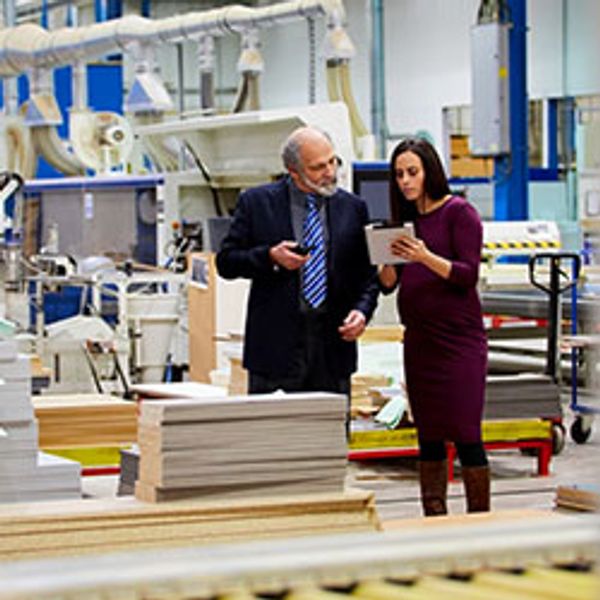
Value stream
Lean manufacturing uses the value stream to reduce waste. This process maps out each step in a process to identify the elements that are necessary and eliminate those that are not. The value stream takes into account the whole life cycle of a product - from the initial idea to the use of the product and its eventual disposal. Understanding this process is the key to eliminating waste. There are three types or wastes in a value-stream.
Flow
The first of 5 lean principles, Flow, involves identifying customers' actual needs and evaluating them. This step is important in the design of new products and services because customers do not always express their needs clearly. The second step involves defining the value stream or the sequence of activities that will complete a project. This is an essential part of lean project management and requires close collaboration with all participants.
Pull
A pull system is only able to start a process when there is a customer request. An example: A pizza place would not make extra pizzas, they only would produce food when they received a customer's order. A restaurant would not waste their time, resources, or ingredients if they did.
Perfection
One of the lean 5 principles is the pursuit of perfection. According to this concept, perfection refers to a perfect state that is precise, consistent, and complete. However, achieving perfection is an elusive goal. This idea is meant to encourage continuous improvement. This helps organizations to achieve a higher level performance.
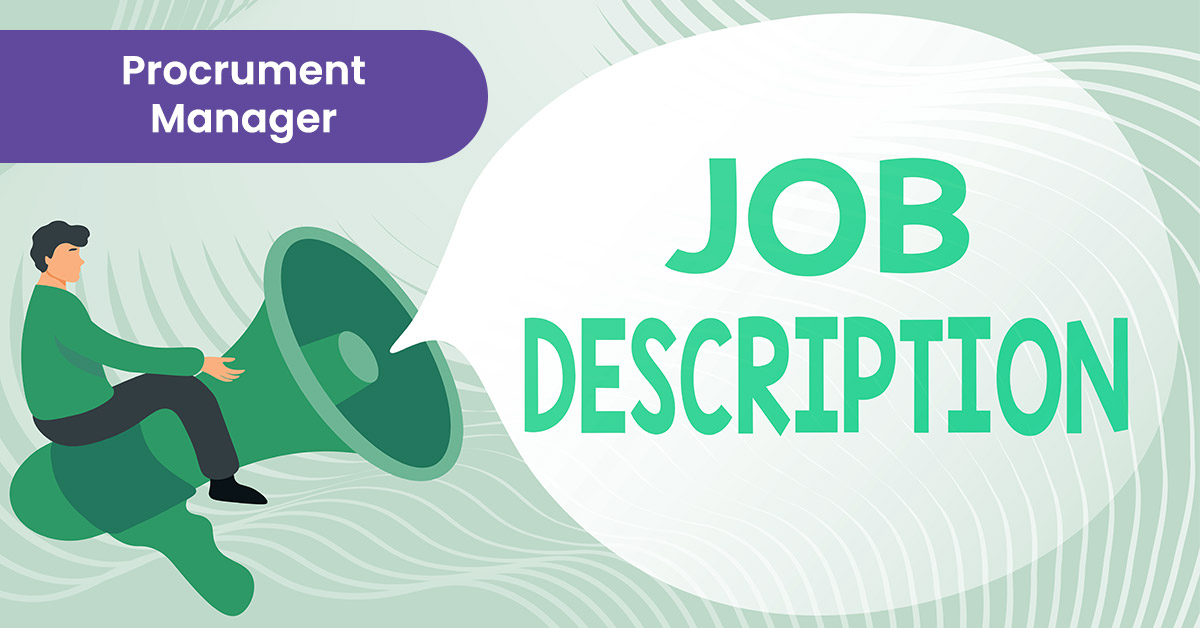
Collaboration among stakeholders
Stakeholder collaboration is a crucial element in lean project administration. Collaboration between project team members is essential to solving problems and increasing project value. Teams should identify and prioritize areas for improvement in the planning phase. The doing phase involves gathering data to help them find solutions. Execution is not the main focus. The organizational structure is also important for team collaboration.
FAQ
What are the requirements to start a logistics business?
It takes a lot of skills and knowledge to run a successful logistics business. To communicate effectively with clients and suppliers, you must be able to communicate well. You must be able analyze data and draw out conclusions. You must be able and able to handle stress situations and work under pressure. To improve efficiency, you must be innovative and creative. You will need strong leadership skills to motivate and direct your team members towards achieving their organizational goals.
You should also be organized and efficient to meet tight deadlines.
How can manufacturing prevent production bottlenecks?
The key to avoiding bottlenecks in production is to keep all processes running smoothly throughout the entire production cycle, from the time you receive an order until the time when the product ships.
This includes both planning for capacity and quality control.
The best way to do this is to use continuous improvement techniques such as Six Sigma.
Six Sigma Management System is a method to increase quality and reduce waste throughout your organization.
It is focused on creating consistency and eliminating variation in your work.
What does "warehouse" mean?
A warehouse or storage facility is where goods are stored before they are sold. It can be an outdoor or indoor area. Sometimes, it can be both an indoor and outdoor space.
Why should you automate your warehouse?
Modern warehousing has seen automation take center stage. E-commerce has brought increased demand for more efficient and quicker delivery times.
Warehouses need to adapt quickly to meet changing needs. Technology is essential for warehouses to be able to adapt quickly to changing needs. Automation of warehouses offers many benefits. Here are some reasons why it's worth investing in automation:
-
Increases throughput/productivity
-
Reduces errors
-
Improves accuracy
-
Safety increases
-
Eliminates bottlenecks
-
Allows companies to scale more easily
-
It makes workers more efficient
-
Gives you visibility into all that is happening in your warehouse
-
Enhances customer experience
-
Improves employee satisfaction
-
Minimizes downtime and increases uptime
-
Quality products delivered on time
-
Removes human error
-
It ensures compliance with regulations
What is production plan?
Production Planning refers to the development of a plan for every aspect of production. This document will ensure everything is in order and ready to go when you need it. You should also have information to ensure the best possible results on set. This includes location information, crew details, equipment specifications, and casting lists.
The first step in filming is to define what you want. You may have already chosen the location you want, or there are locations or sets you prefer. Once you have identified your locations and scenes, you can start working out which elements you require for each scene. Perhaps you have decided that you need to buy a car but aren't sure which model. You could look online for cars to see what options are available, and then narrow down your choices by selecting between different makes or models.
Once you have found the right car, you can start thinking about extras. Are you looking for people to sit in the front seats? Or perhaps you need someone walking around the back of the car? You may want to change the interior's color from black or white. These questions will help you determine the exact look and feel of your car. It is also worth considering the types of shots that you wish to take. You will be filming close-ups and wide angles. Maybe the engine or steering wheel is what you are looking to film. All of these things will help you identify the exact style of car you want to film.
Once you have made all the necessary decisions, you can start to create a schedule. The schedule will show you when to begin shooting and when to stop. You will need to know when you have to be there, what time you have to leave and when your return home. So everyone is clear about what they need to do. You can also make sure to book extra staff in advance if you have to hire them. There is no point in hiring someone who won't turn up because you didn't let him know.
Also, consider how many days you will be filming your schedule. Some projects only take one or two days, while others may last weeks. When you are creating your schedule, you should always keep in mind whether you need more than one shot per day or not. Multiple shots at the same location can increase costs and make it more difficult to complete. You can't be certain if you will need multiple takes so it is better not to shoot too many.
Budgeting is another important aspect of production planning. You will be able to manage your resources if you have a realistic budget. It is possible to reduce the budget at any time if you experience unexpected problems. You shouldn't underestimate the amount you'll spend. If you underestimate how much something costs, you'll have less money to pay for other items.
Production planning can be a complex process. However, once you know how everything works together it will become easier to plan future projects.
What is manufacturing and logistics?
Manufacturing refers the process of producing goods from raw materials through machines and processes. Logistics manages all aspects of the supply chain, including procurement, production planning and distribution, inventory control, transportation, customer service, and transport. Sometimes manufacturing and logistics are combined to refer to a wider term that includes both the process of creating products as well as their delivery to customers.
Statistics
- [54][55] These are the top 50 countries by the total value of manufacturing output in US dollars for its noted year according to World Bank.[56] (en.wikipedia.org)
- Many factories witnessed a 30% increase in output due to the shift to electric motors. (en.wikipedia.org)
- It's estimated that 10.8% of the U.S. GDP in 2020 was contributed to manufacturing. (investopedia.com)
- According to the United Nations Industrial Development Organization (UNIDO), China is the top manufacturer worldwide by 2019 output, producing 28.7% of the total global manufacturing output, followed by the United States, Japan, Germany, and India.[52][53] (en.wikipedia.org)
- According to a Statista study, U.S. businesses spent $1.63 trillion on logistics in 2019, moving goods from origin to end user through various supply chain network segments. (netsuite.com)
External Links
How To
Six Sigma in Manufacturing:
Six Sigma is "the application statistical process control (SPC), techniques for continuous improvement." It was developed by Motorola's Quality Improvement Department at their plant in Tokyo, Japan, in 1986. Six Sigma is a method to improve quality through standardization and elimination of defects. Many companies have adopted Six Sigma in recent years because they believe that there are no perfect products and services. The main goal of Six Sigma is to reduce variation from the mean value of production. This means that if you take a sample of your product, then measure its performance against the average, you can find out what percentage of the time the process deviates from the norm. If this deviation is too big, you know something needs fixing.
Understanding the dynamics of variability within your business is the first step in Six Sigma. Once you have a good understanding of the basics, you can identify potential sources of variation. It is important to identify whether the variations are random or systemic. Random variations happen when people make errors; systematic variations are caused externally. You could consider random variations if some widgets fall off the assembly lines. If however, you notice that each time you assemble a widget it falls apart in exactly the same spot, that is a problem.
Once you've identified where the problems lie, you'll want to design solutions to eliminate those problems. This could mean changing your approach or redesigning the entire process. Test them again once you've implemented the changes. If they don't work you need to rework them and come up a better plan.