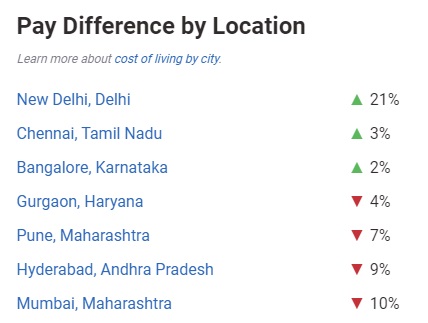
What salary is a robot engineer earning? Learn more about the duties and responsibilities of robotics engineers and what the average salary is for this job. Find out how much it costs to live in different places and what experience is required to become a robot engineer. Robotic engineers have many benefits.
Average salary for a robots engineer
The average salary of a robotic engineer will vary depending on many factors including your experience level and seniority. Engineers typically earn more the higher up the ranks. Robotics technicians are some of the highest-paid workers in technology. They also enjoy their jobs. As the field continues to evolve, robotic engineers need to be problem solvers and innovative. Robotics engineering requires a diverse skill set and a thorough knowledge of mathematics and science.
The average salary for a robotic engineer is PS27,500 a year, according to the National Careers Service. But, the starting salary for a position that focuses on maintenance or operation can be lower than this. The company's size is another factor that can impact starting salaries. Higher starting salaries are usually offered by larger companies.
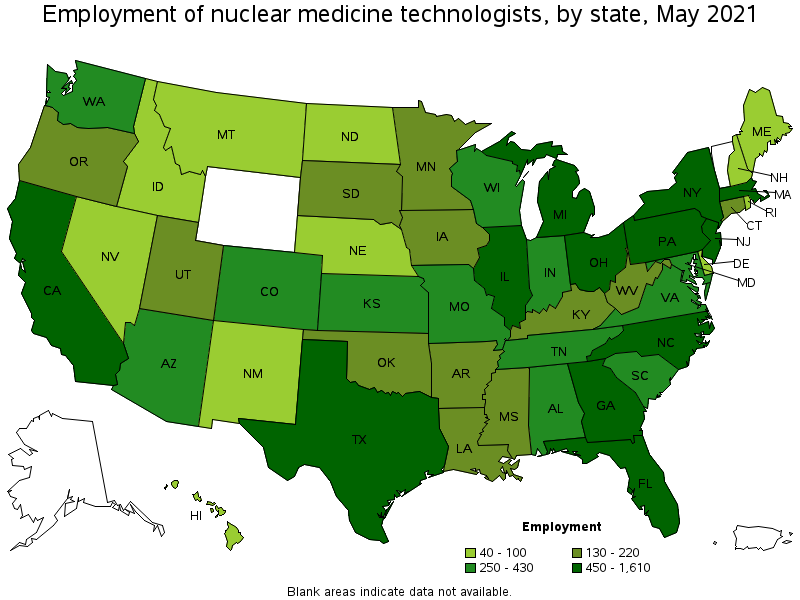
Responsibilities of a robotics engineer
The job of a robotics engineer is to develop and write algorithms and program code. They are also responsible for research in robotics, and robotic technology. They develop new robotic systems and find ways to improve their performance. They could also design robotic systems to support military defense or high throughput operations. They must be skilled in communication and mathematics.
A robotics engineer should be skilled and innovative. They should be able to predict future robotic needs and work well together with other team members. They should be able and willing to work with engineers.
Cost of living in different cities
A city that offers high salaries is a good choice if you are looking for a job as a robotic engineer. Boston, for instance, has a strong robotics history and lower housing costs than other robotics hubs. Boston has many robotics companies, including Boston Dynamics and iRobot.
An average salary for a robotics engineering engineer is $94,310 per the year. This means you can live comfortably even during your mid-career. However, the cost of living in robotic engineering cities is higher in some cities.
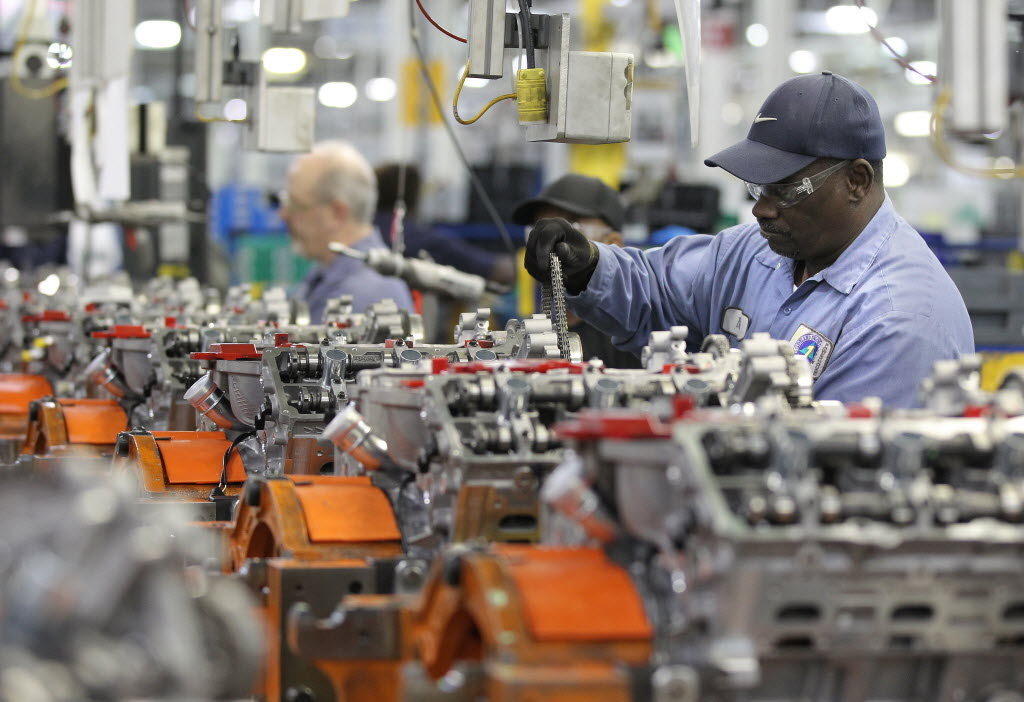
Experience level required to become a robotics engineer
As a robotics engineer, you will use computer software to develop detailed designs and test the performance of robotic systems. You will need to be analytical and able make compromises in order for the robots to function properly. Robotic engineers need to communicate well and solve problems.
Engineers will often work in a group environment and collaborate on software development. In addition, they must have excellent communication skills so they can convey their thoughts to other experts in their field. The job requires you to regularly deliver reports to investors or other stakeholders. Robotics engineers must have excellent teamwork skills as the development process can be risky. Even the smallest mistake can make a huge difference in the outcome of a system.
FAQ
Why should you automate your warehouse?
Modern warehouses have become more dependent on automation. The rise of e-commerce has led to increased demand for faster delivery times and more efficient processes.
Warehouses have to be flexible to meet changing requirements. In order to do this, they need to invest in technology. Automation warehouses can bring many benefits. Here are some benefits of investing in automation
-
Increases throughput/productivity
-
Reduces errors
-
Improves accuracy
-
Safety increases
-
Eliminates bottlenecks
-
Allows companies to scale more easily
-
This makes workers more productive
-
The warehouse can be viewed from all angles.
-
Enhances customer experience
-
Improves employee satisfaction
-
It reduces downtime, and increases uptime
-
This ensures that quality products are delivered promptly
-
Human error can be eliminated
-
It ensures compliance with regulations
What is the importance of automation in manufacturing?
Automation is essential for both manufacturers and service providers. It allows them provide faster and more efficient services. They can also reduce their costs by reducing human error and improving productivity.
Why is logistics important in manufacturing?
Logistics are an essential component of any business. They can help you achieve great success by helping you manage product flow from raw material to finished goods.
Logistics plays a significant role in reducing cost and increasing efficiency.
What are the main products of logistics?
Logistics involves the transportation of goods from point A and point B.
These include all aspects related to transport such as packaging, loading and transporting, storing, transporting, unloading and warehousing inventory management, customer service. Distribution, returns, recycling are some of the options.
Logisticians make sure that the right product arrives at the right place at the correct time and in safe conditions. They provide information on demand forecasts as well stock levels, production schedules and availability of raw material.
They coordinate with vendors and suppliers, keep track of shipments, monitor quality standards and perform inventory and order replenishment.
How can I find out more about manufacturing?
Hands-on experience is the best way to learn more about manufacturing. However, if that's not possible, you can always read books or watch educational videos.
How can manufacturing excess production be decreased?
Improved inventory management is the key to reducing overproduction. This would reduce the time needed to manage inventory. This could help us free up our time for other productive tasks.
One way to do this is to adopt a Kanban system. A Kanban Board is a visual display that tracks work progress. Kanban systems are where work items travel through a series of states until reaching their final destination. Each state is assigned a different priority.
When work is completed, it can be transferred to the next stage. But if a task remains in the beginning stages it will stay that way until it reaches its end.
This allows for work to continue moving forward, while also ensuring that there is no work left behind. Managers can monitor the work being done by Kanban boards to see what is happening at any given time. This allows them to adjust their workflows based on real-time information.
Lean manufacturing can also be used to reduce inventory levels. Lean manufacturing is about eliminating waste from all stages of the production process. Waste includes anything that does not add value to the product. There are several types of waste that you might encounter:
-
Overproduction
-
Inventory
-
Unnecessary packaging
-
Exceed materials
Manufacturers can increase efficiency and decrease costs by implementing these ideas.
Statistics
- Many factories witnessed a 30% increase in output due to the shift to electric motors. (en.wikipedia.org)
- (2:04) MTO is a production technique wherein products are customized according to customer specifications, and production only starts after an order is received. (oracle.com)
- It's estimated that 10.8% of the U.S. GDP in 2020 was contributed to manufacturing. (investopedia.com)
- In 2021, an estimated 12.1 million Americans work in the manufacturing sector.6 (investopedia.com)
- According to a Statista study, U.S. businesses spent $1.63 trillion on logistics in 2019, moving goods from origin to end user through various supply chain network segments. (netsuite.com)
External Links
How To
How to Use Six Sigma in Manufacturing
Six Sigma is "the application statistical process control (SPC), techniques for continuous improvement." Motorola's Quality Improvement Department, Tokyo, Japan, developed it in 1986. Six Sigma is a method to improve quality through standardization and elimination of defects. Many companies have adopted this method in recent years. They believe there is no such thing a perfect product or service. Six Sigma's primary goal is to reduce variation from the average value of production. It is possible to measure the performance of your product against an average and find the percentage of time that it differs from the norm. If there is a significant deviation from the norm, you will know that something needs to change.
Understanding how variability works in your company is the first step to Six Sigma. Once you have this understanding, you will need to identify sources and causes of variation. These variations can also be classified as random or systematic. Random variations happen when people make errors; systematic variations are caused externally. For example, if you're making widgets, and some of them fall off the assembly line, those would be considered random variations. However, if you notice that every time you assemble a widget, it always falls apart at exactly the same place, then that would be a systematic problem.
Once you have identified the problem, you can design solutions. It might mean changing the way you do business or redesigning it entirely. After implementing the new changes, you should test them again to see if they worked. If they don’t work, you’ll need to go back and rework the plan.