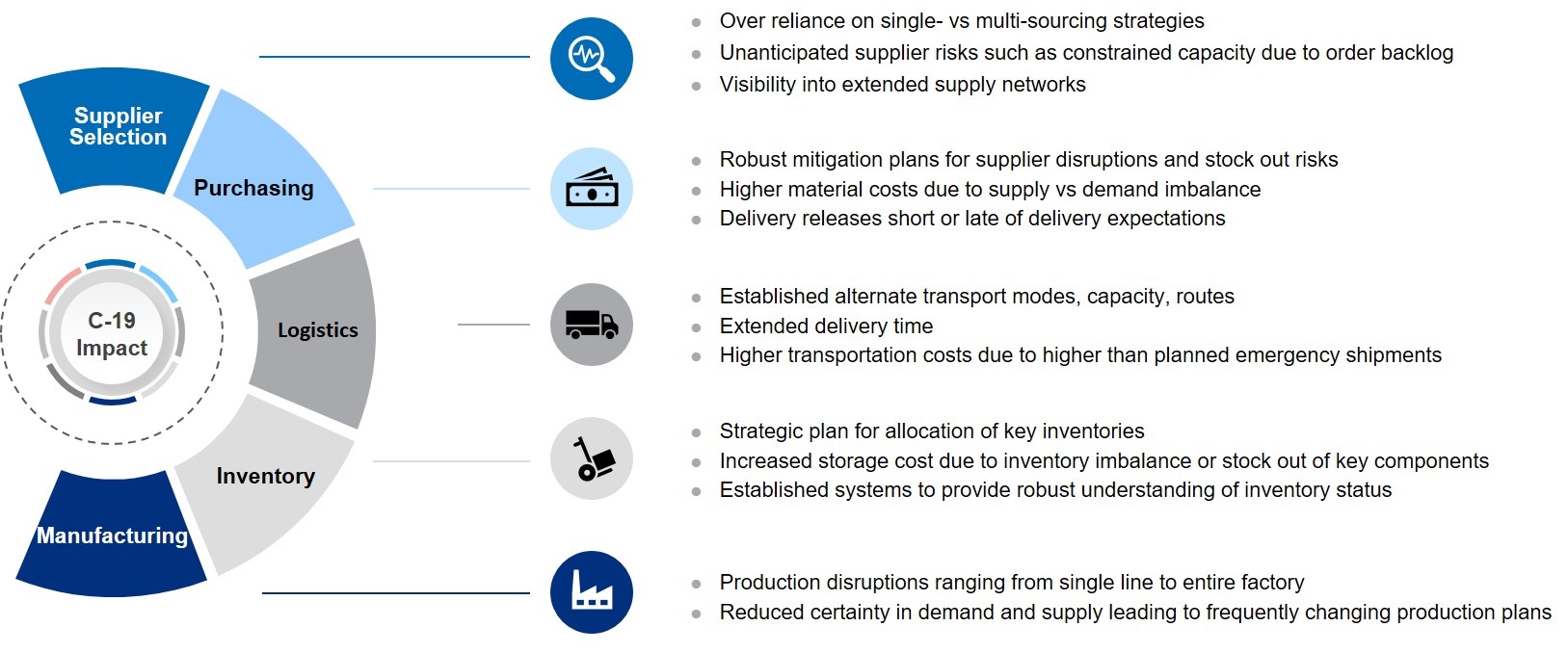
A cost estimate can be used to accurately price almost any service a company offers. This is the job of cost estimators. They aid companies to determine the costs involved in manufacturing or developing new products. They also need to assess the cost of building new structures. This includes analysing the labor and materials costs.
Construction companies employ most cost estimaters. They are expected to be well-versed in construction processes and methods. They should also be proficient in computer-aided designing (CAD) software. This software can improve design and manufacturing efficiency. The software can also be used to analyze data from databases. They can also utilize other software such as Microsoft Excel.
To make accurate cost estimates, cost estimators collaborate with other professionals. They review the project blueprints and site conditions to determine the cost of each component. They may also consult engineers to determine the necessary machining operations and gauges.
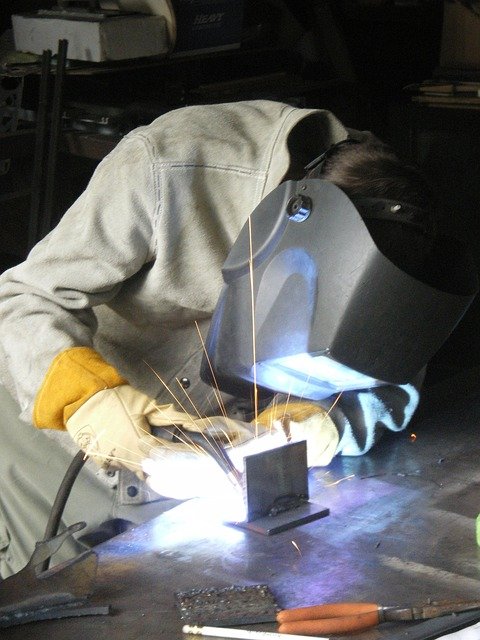
Cost estimators should be detail-oriented, assertive and reliable. They must be able interpret difficult information and analyze it. They must be able to communicate clearly and accurately their findings. Aside from that, they should be able work with professionals as well as clients.
Cost estimators typically work in the engineering or cost divisions of a company. They must be able to apply science and math skills. They should be proficient in computer software such as CAD, BIM and commercial. You may need to take a certification class. Certified Cost Estimator/Analyst(CCEA), Professional cost estimator/Analyst and Certified Professional Estimator are some examples of certifications.
Cost estimators could be specialists in specific industries or services. One person may specialize in building costs or construction, while another might be more interested in software development costs. Cost estimators could also be employed in other areas like automotive repair and management, building construction, or specialty trade contractors.
This occupation requires individuals to communicate with clients, engineers, and suppliers. They are also fluent in industry terminology. They are also able to build a solid knowledge base in order to prepare cost estimates. This occupation is not only responsible for preparing cost estimates but also conducts studies to study the impact of various processes on costs and to find ways to decrease costs.
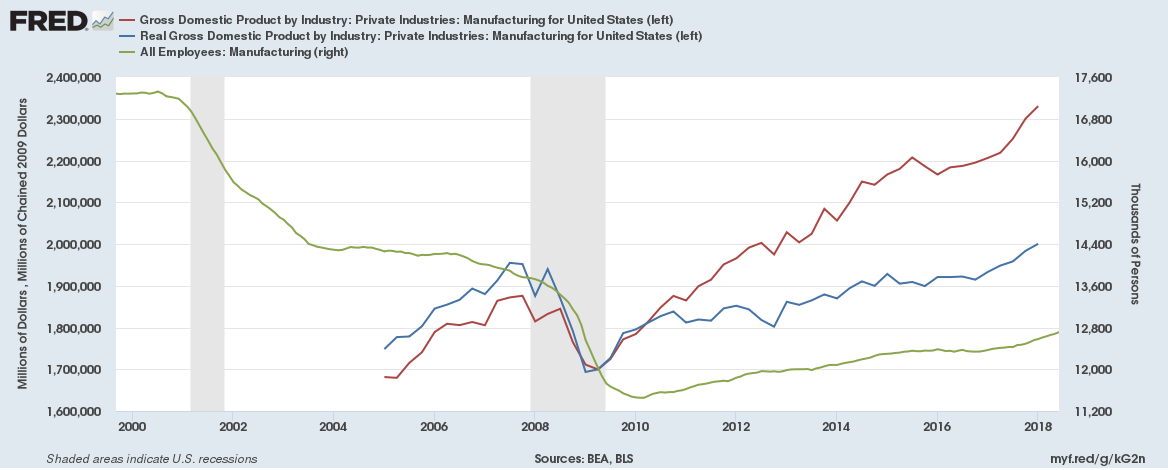
You may need to have a bachelor’s degree depending on your industry. An internship may be required. They may also be eligible for cooperative education programs. A degree in building construction, or construction management is also an advantage for construction companies.
In construction companies and other manufacturing firms, cost estimators are employed. They aid companies to create accurate estimates that can be used to help them place profitable bids. They also analyze data related the supply chain as well as other factors that may affect costs. Cost estimators can also work for government programs. They may be asked to design new products or services.
Cost estimators need to have a solid understanding of computer-aided designing (CAD) software. They can also learn how to use automated cost estimation software.
FAQ
How can I learn about manufacturing?
The best way to learn about manufacturing is through hands-on experience. You can also read educational videos or take classes if this isn't possible.
What is the job of a logistics manger?
A logistics manager makes sure that all goods are delivered on-time and in good condition. This is done by using his/her experience and knowledge of the company's products. He/she must also ensure sufficient stock to meet the demand.
How can we improve manufacturing efficiency?
First, we need to identify which factors are most critical in affecting production times. Next, we must find ways to improve those factors. You can start by identifying the most important factors that impact production time. Once you've identified them, try to find solutions for each of those factors.
Why is logistics so important in manufacturing?
Logistics are essential to any business. Logistics can help you achieve amazing results by helping to manage product flow from raw materials to finished products.
Logistics play an important role in reducing costs as well as increasing efficiency.
Is automation important for manufacturing?
Automating is not just important for manufacturers, but also for service providers. Automation allows them to deliver services quicker and more efficiently. It reduces human errors and improves productivity, which in turn helps them lower their costs.
Statistics
- According to the United Nations Industrial Development Organization (UNIDO), China is the top manufacturer worldwide by 2019 output, producing 28.7% of the total global manufacturing output, followed by the United States, Japan, Germany, and India.[52][53] (en.wikipedia.org)
- (2:04) MTO is a production technique wherein products are customized according to customer specifications, and production only starts after an order is received. (oracle.com)
- You can multiply the result by 100 to get the total percent of monthly overhead. (investopedia.com)
- [54][55] These are the top 50 countries by the total value of manufacturing output in US dollars for its noted year according to World Bank.[56] (en.wikipedia.org)
- Many factories witnessed a 30% increase in output due to the shift to electric motors. (en.wikipedia.org)
External Links
How To
How to Use 5S to Increase Productivity in Manufacturing
5S stands in for "Sort", the "Set In Order", "Standardize", or "Separate". Toyota Motor Corporation invented the 5S strategy in 1954. It helps companies achieve higher levels of efficiency by improving their work environment.
This method aims to standardize production processes so that they are repeatable, measurable and predictable. Cleaning, sorting and packing are all done daily. These actions allow workers to perform their job more efficiently, knowing what to expect.
Implementing 5S requires five steps. These are Sort, Set In Order, Standardize. Separate. And Store. Each step is a different action that leads to greater efficiency. If you sort items, it makes them easier to find later. When items are ordered, they are put together. Next, organize your inventory into categories and store them in containers that are easily accessible. Finally, when you label your containers, you ensure everything is labeled correctly.
Employees must be able to critically examine their work practices. Employees need to be able understand their motivations and discover alternative ways to do them. They must learn new skills and techniques in order to implement the 5S system.
The 5S Method not only improves efficiency, but it also helps employees to be more productive and happier. They will feel motivated to strive for higher levels of efficiency once they start to see results.