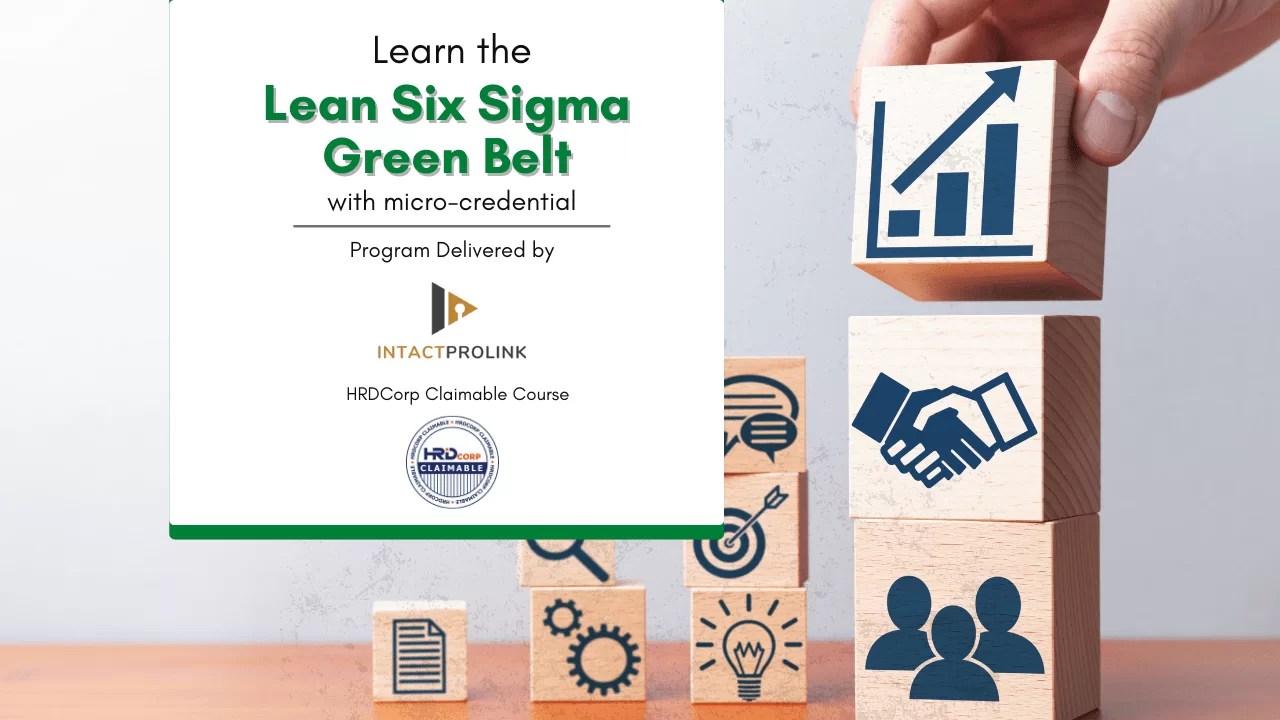
DFSS (Design for Six Sigma), a design methodology, uses a variety of methods to design a product or service. It is designed to reduce waste, improve quality, and increase market share. This is an efficient method that can help improve your products.
DFSS allows customers to be included in the design process. This helps ensure that your product or service is the most suitable for your customers' needs. It also ensures that your product has a high level of quality when it is introduced to the market. DFSS is often used for the design of a product or a service. It is also used for designing products and/or services that can replace existing products or services.
The DFSS team begins by determining what the customer needs. This can involve gathering information, interviewing customers, or surveying customers. In order to find the best product or design, the design team reviews other products and designs. This phase also includes developing substitute concepts and classifying functional needs. Additional steps may be required depending on how complex the project is.
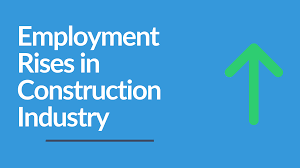
DFSS can be used by companies to create products and services that are efficient and effective. It can also be used to identify potential issues before they become serious problems. It helps reduce waste and increases profitability. It is designed to improve the effectiveness of a product/service by identifying processes that make it more efficient.
There are different methodologies for implementing DFSS. DMADV, which follows a 5-step process, is the most common method for implementing DFSS. The process begins with the definition of the customer and their needs. Next, they create a design concept. This method has a solid engineering base and is often used when developing new products and/or services. It also includes an analysis and measurement phase to evaluate product performance.
Optimization is the next phase. This involves evaluating product performance across multiple performance levels. This step is very useful for developing new business procedures. This stage aims to reduce variability and ensure stability over time.
Verification is the final stage. This is used often to confirm that the product's stability. This stage also validates that the product is capable of performing over time. This step will also include validation testing. Validation testing is typically completed once the design has been approved.
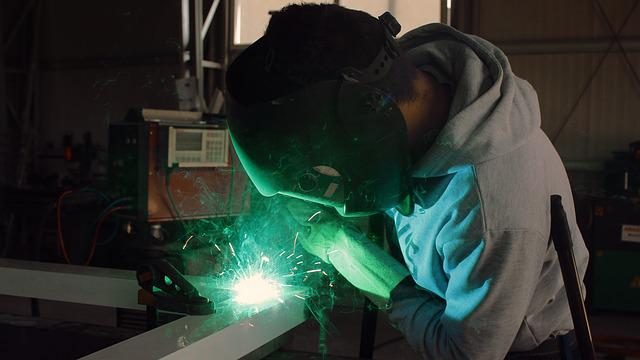
You need a process map to show all of the workflows involved in implementing DFSS. Additionally, it is important to include information on resources and timeframes as well milestones. You should also be able to identify any external involvement that may be required. It may be necessary to develop a prototype of the product to make sure it meets all customer requirements. It is also beneficial to implement DFSS within an environment that offers clear rewards for achieving the goals of your project.
FAQ
How can overproduction in manufacturing be reduced?
The key to reducing overproduction lies in developing better ways to manage inventory. This would decrease the time that is spent on inefficient activities like purchasing, storing, or maintaining excess stock. We could use these resources to do other productive tasks.
Kanban systems are one way to achieve this. A Kanban Board is a visual display that tracks work progress. Kanban systems allow work items to move through different states until they reach their final destination. Each state is assigned a different priority.
If work is moving from one stage to the other, then the current task can be completed and moved on to the next. A task that is still in the initial stages of a process will be considered complete until it moves on to the next stage.
This allows you to keep work moving along while making sure that no work gets neglected. Managers can view the Kanban board to see how much work they have done. This information allows them to adjust their workflow based on real-time data.
Lean manufacturing, another method to control inventory levels, is also an option. Lean manufacturing seeks to eliminate waste from every step of the production cycle. Anything that doesn't add value to the product is considered waste. Here are some examples of common types.
-
Overproduction
-
Inventory
-
Unnecessary packaging
-
Materials in excess
Manufacturers can reduce their costs and improve their efficiency by using these ideas.
Why is logistics important in manufacturing
Logistics are an integral part any business. They help you achieve great results by helping you manage all aspects of product flow, from raw materials to finished goods.
Logistics are also important in reducing costs and improving efficiency.
What is the difference between Production Planning and Scheduling?
Production Planning (PP), is the process of deciding what production needs to take place at any given time. Forecasting and identifying production capacity are two key elements to this process.
Scheduling refers to the process of allocating specific dates to tasks in order that they can be completed within a specified timeframe.
Can certain manufacturing steps be automated?
Yes! Yes. Automation has been around since ancient time. The Egyptians invented the wheel thousands of years ago. Today, robots assist in the assembly of lines.
Actually, robotics can be used in manufacturing for many purposes. These include:
-
Assembly line robots
-
Robot welding
-
Robot painting
-
Robotics inspection
-
Robots that create products
There are many other examples of how manufacturing could benefit from automation. 3D printing, for example, allows us to create custom products without waiting for them to be made.
What is manufacturing and logistics?
Manufacturing refers the process of producing goods from raw materials through machines and processes. Logistics manages all aspects of the supply chain, including procurement, production planning and distribution, inventory control, transportation, customer service, and transport. Sometimes manufacturing and logistics are combined to refer to a wider term that includes both the process of creating products as well as their delivery to customers.
Statistics
- It's estimated that 10.8% of the U.S. GDP in 2020 was contributed to manufacturing. (investopedia.com)
- [54][55] These are the top 50 countries by the total value of manufacturing output in US dollars for its noted year according to World Bank.[56] (en.wikipedia.org)
- (2:04) MTO is a production technique wherein products are customized according to customer specifications, and production only starts after an order is received. (oracle.com)
- According to a Statista study, U.S. businesses spent $1.63 trillion on logistics in 2019, moving goods from origin to end user through various supply chain network segments. (netsuite.com)
- Job #1 is delivering the ordered product according to specifications: color, size, brand, and quantity. (netsuite.com)
External Links
How To
Six Sigma: How to Use it in Manufacturing
Six Sigma is "the application statistical process control (SPC), techniques for continuous improvement." It was developed by Motorola's Quality Improvement Department at their plant in Tokyo, Japan, in 1986. The basic idea behind Six Sigma is to improve quality by improving processes through standardization and eliminating defects. In recent years, many companies have adopted this method because they believe there is no such thing as perfect products or services. Six Sigma seeks to reduce variation between the mean production value. If you take a sample and compare it with the average, you will be able to determine how much of the production process is different from the norm. If it is too large, it means that there are problems.
The first step toward implementing Six Sigma is understanding how variability works in your business. Once you've understood that, you'll want to identify sources of variation. This will allow you to decide if these variations are random and systematic. Random variations occur when people do mistakes. Symmetrical variations are caused due to factors beyond the process. If you make widgets and some of them end up on the assembly line, then those are considered random variations. If however, you notice that each time you assemble a widget it falls apart in exactly the same spot, that is a problem.
After identifying the problem areas, you will need to devise solutions. You might need to change the way you work or completely redesign the process. You should then test the changes again after they have been implemented. If they fail, you can go back to the drawing board to come up with a different plan.