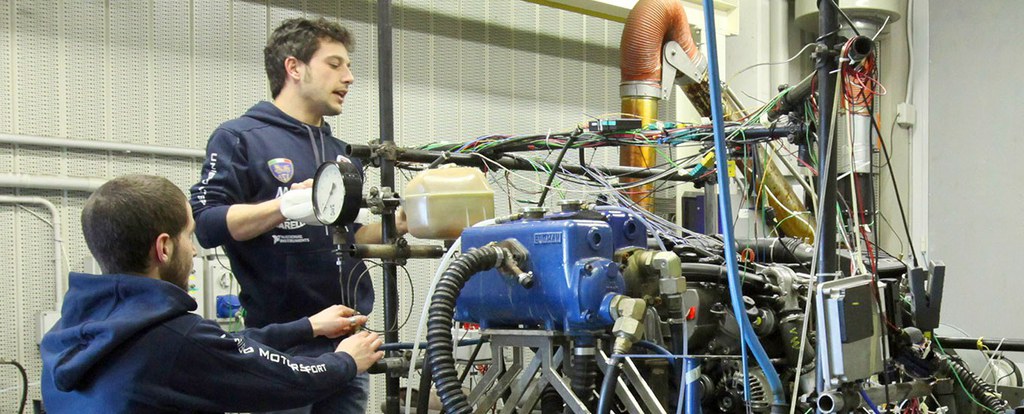
Are you interested in the average salary of environmental engineers? Here's an overview of the average annual income for environmental engineers. Also read on to learn about the job outlook and the requirements to become one. This article will discuss the job outlook and salary requirements for environmental engineers. Average annual salaries for environmental engineers are $59,870. You should realize that you can earn more. A bachelor's degree is required in environmental engineering, or an equivalent.
Average annual salary
The average annual salary for environmental engineers is $96,820, and is expected to grow slightly faster than the average for all occupations. Over the next decade, there will be approximately 4,000 openings. This is mostly due to people retiring or moving to other professions. Seek out similar salaries to find out if you have the right experience and degree for the job of environmental engineer.
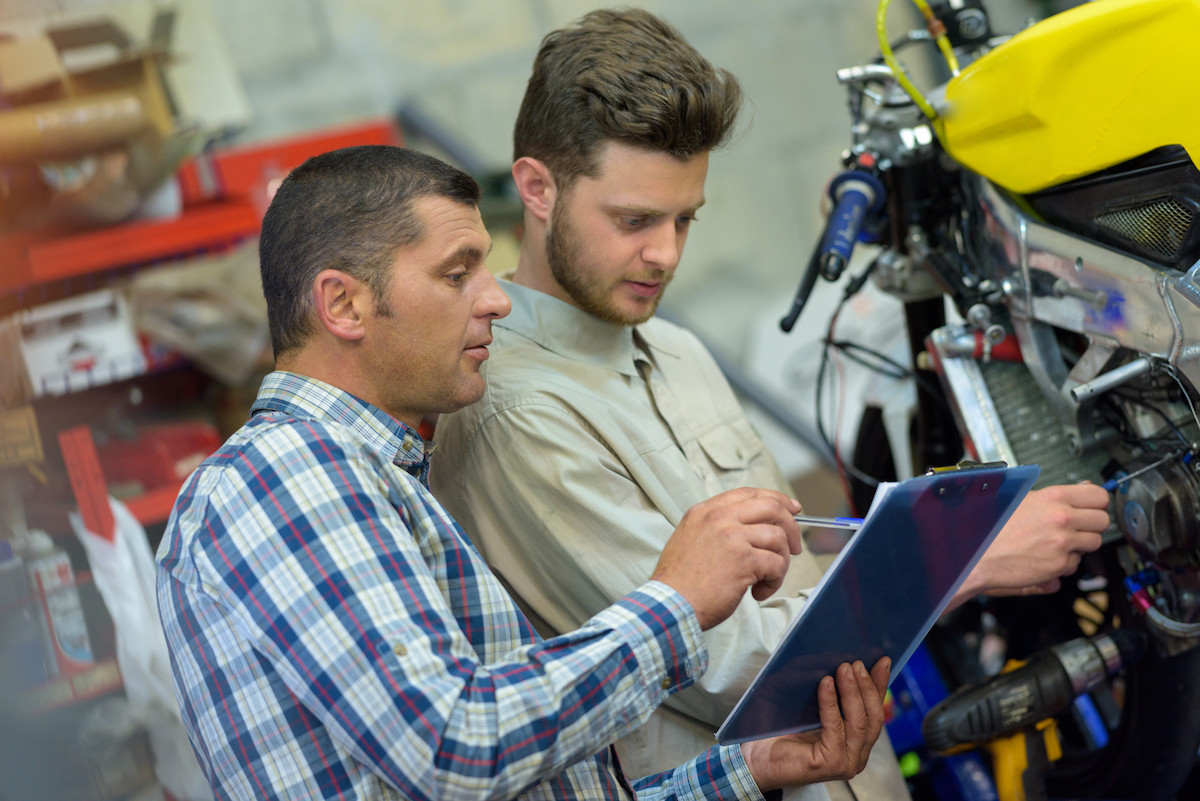
The average annual salary of an environmental engineer is not set, but this field provides both meaning and financial work. According to the BLS, environmental engineers working for the federal government made an average annual salary of $101,640. The highest-paid 10% earned more than $128,000. There are however variations within the profession, with the highest-paid earning individuals making more than $150,000 while the lowest-paid workers earning less that $67,000.
Environmental engineers have a bright future.
According to the Bureau of Labor Statistics the outlook for environmental engineers' employment is good. There will be an increase of 3.23% in the number of environmental engineer jobs from 2004 to 2024. This is slightly lower than the national average. There will be another 7,350 job openings in the near future. This is an increase of 1.63 percent per year. But, there is only moderate growth in job openings.
As people are more conscious of the environmental effects of human activity on the environment, the demand to be an environmental engineer will grow. This is due a growing awareness of environmental damages and the need for solutions. This makes the hiring market for environmental engineers very friendly. According to the U.S. Bureau of Labor Statistics there is a 12 percent growth in demand for environmental engineers between 2014 and 2024. It is therefore a good time in your life to obtain a degree of environmental engineering.
The requirements for becoming an environmental engineer
An engineering bachelor's degree can make you eligible for the Foundational Examination (FE). This exam tests your basic knowledge and understanding of the environmental environment. These engineers may also be known as "engineer interns", or "engineer im training", until they can take Principles and Practice of Engineering. While many states require the continued education of environmental engineers, most will recognize prior licensure. Additionally, environmental engineers can earn board certification from the American Academy of Environmental Engineers (AACE), a mark of experience that demonstrates the level of expertise they have in a particular area of environmental engineering.
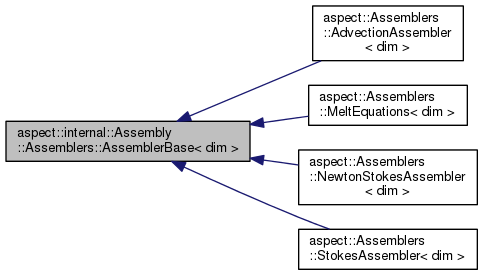
A bachelor's degree is not enough. There are also other skills required. Environmental engineers must be highly imaginative and able to imagine how their designs and solutions will affect larger systems. They must communicate well with others and be able work independently. They must be able to collaborate with a wide variety of professionals, including scientists and other engineers who have other specialties. They must also be able to write clearly.
FAQ
What are the logistics products?
Logistics involves the transportation of goods from point A and point B.
They cover all aspects of transportation, such as packing, loading, transporting and unloading.
Logisticians make sure that the right product arrives at the right place at the correct time and in safe conditions. They provide information on demand forecasts as well stock levels, production schedules and availability of raw material.
They keep track and monitor the transit of shipments, maintain quality standards, order replenishment and inventories, coordinate with suppliers, vendors, and provide support for sales and marketing.
How can we reduce manufacturing overproduction?
Better inventory management is key to reducing excess production. This would reduce the time spent on unproductive activities like purchasing, storing and maintaining excess stock. This will allow us to free up resources for more productive tasks.
One way to do this is to adopt a Kanban system. A Kanban board, a visual display to show the progress of work, is called a Kanban board. In a Kanban system, work items move through a sequence of states until they reach their final destination. Each state has a different priority level.
When work is completed, it can be transferred to the next stage. A task that is still in the initial stages of a process will be considered complete until it moves on to the next stage.
This allows you to keep work moving along while making sure that no work gets neglected. Managers can see how much work has been done and the status of each task at any time with a Kanban Board. This data allows them adjust their workflow based upon real-time data.
Another way to control inventory levels is to implement lean manufacturing. Lean manufacturing works to eliminate waste throughout every stage of the production chain. Anything that doesn't add value to the product is considered waste. These are some of the most common types.
-
Overproduction
-
Inventory
-
Packaging not required
-
Exceed materials
Manufacturers can increase efficiency and decrease costs by implementing these ideas.
What are the 7 R's of logistics?
The 7R's of Logistics is an acronym for the seven basic principles of logistics management. It was developed and published by the International Association of Business Logisticians in 2004 as part of the "Seven Principles of Logistics Management".
The acronym consists of the following letters:
-
Responsible - to ensure that all actions are within the legal requirements and are not detrimental to others.
-
Reliable - have confidence in the ability to deliver on commitments made.
-
Be responsible - Use resources efficiently and avoid wasting them.
-
Realistic – consider all aspects of operations, from cost-effectiveness to environmental impact.
-
Respectful – Treat others fairly and equitably.
-
Reliable - Find ways to save money and increase your productivity.
-
Recognizable is a company that provides customers with value-added solutions.
Statistics
- In 2021, an estimated 12.1 million Americans work in the manufacturing sector.6 (investopedia.com)
- You can multiply the result by 100 to get the total percent of monthly overhead. (investopedia.com)
- According to a Statista study, U.S. businesses spent $1.63 trillion on logistics in 2019, moving goods from origin to end user through various supply chain network segments. (netsuite.com)
- According to the United Nations Industrial Development Organization (UNIDO), China is the top manufacturer worldwide by 2019 output, producing 28.7% of the total global manufacturing output, followed by the United States, Japan, Germany, and India.[52][53] (en.wikipedia.org)
- [54][55] These are the top 50 countries by the total value of manufacturing output in US dollars for its noted year according to World Bank.[56] (en.wikipedia.org)
External Links
How To
How to use lean manufacturing in the production of goods
Lean manufacturing is a management style that aims to increase efficiency and reduce waste through continuous improvement. It was first developed in Japan in the 1970s/80s by Taiichi Ahno, who was awarded the Toyota Production System (TPS), award from KanjiToyoda, the founder of TPS. Michael L. Watkins published the first book on lean manufacturing in 1990.
Lean manufacturing is often defined as a set of principles used to improve the quality, speed, and cost of products and services. It emphasizes the elimination of defects and waste throughout the value stream. The five-steps of Lean Manufacturing are just-in time (JIT), zero defect and total productive maintenance (TPM), as well as 5S. Lean manufacturing emphasizes reducing non-value-added activities like inspection, rework and waiting.
Lean manufacturing improves product quality and costs. It also helps companies reach their goals quicker and decreases employee turnover. Lean manufacturing has been deemed one of the best ways to manage the entire value-chain, including customers, distributors as well retailers and employees. Lean manufacturing is widely used in many industries. Toyota's philosophy has been a key driver of success in many industries, including automobiles and electronics.
Five principles are the basis of lean manufacturing:
-
Define Value: Identify the social value of your business and what sets you apart.
-
Reduce waste - Stop any activity that isn't adding value to the supply chains.
-
Create Flow - Make sure work runs smoothly without interruptions.
-
Standardize & simplify - Make processes consistent and repeatable.
-
Build Relationships - Establish personal relationships with both internal and external stakeholders.
Lean manufacturing isn’t new, but it has seen a renewed interest since 2008 due to the global financial crisis. To increase their competitiveness, many businesses have turned to lean manufacturing. Some economists even believe that lean manufacturing can be a key factor in economic recovery.
With many benefits, lean manufacturing is becoming more common in the automotive industry. These include improved customer satisfaction, reduced inventory levels, lower operating costs, increased productivity, and better overall safety.
It can be applied to any aspect of an organisation. Because it makes sure that all value chains are efficient and effectively managed, Lean Manufacturing is particularly helpful for organizations.
There are three types principally of lean manufacturing:
-
Just-in-Time Manufacturing: Also known as "pull systems", this type of lean manufacturing uses just-in-time manufacturing (JIT). JIT stands for a system where components are assembled on the spot rather than being made in advance. This approach is designed to reduce lead times and increase the availability of components. It also reduces inventory.
-
Zero Defects Manufacturing (ZDM): ZDM focuses on ensuring that no defective units leave the manufacturing facility. It is better to repair a part than have it removed from the production line if it needs to be fixed. This is also true for finished products that require minor repairs before shipping.
-
Continuous Improvement: Continuous Improvement aims to improve efficiency by continually identifying problems and making adjustments to eliminate or minimize waste. It involves continuous improvement of processes, people, and tools.