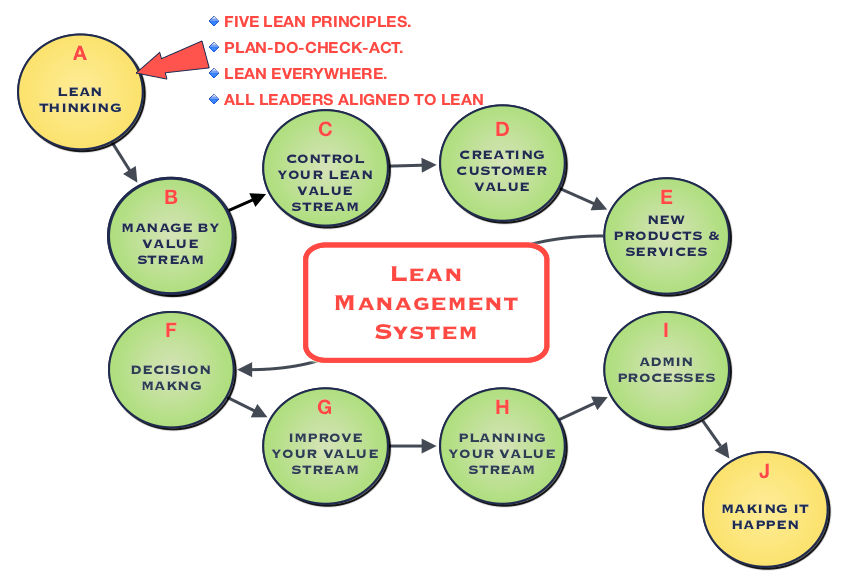
In job manufacturing, the duties and responsibilities of a job director are similar to those of a manufacturing associate. This article will talk about the qualifications needed to become a job-director in manufacturing. This position requires a skilled workforce to execute various operations. In addition, it is important to have erratic workflow, as it will help manage projects and track development. This type of production line demands a skilled workforce. It requires employees who can keep up with the pace, and be able deliver quality products on-time.
Job director for manufacturing
The duties of a job director of manufacturing include managing the daily operations of a manufacturing unit. They are responsible to ensure that products meet the highest standards and are completed on-time. The director of manufacturing must be able to work with engineers and designers in order to develop new products. Before a product goes into large-scale production, they have to assess its feasibility, market fit and impact on processes as well as quality. A director of manufacturing must also have leadership skills. They should also be able to mentor and implement changes to processes and equipment.
Directors of manufacturing usually hold a bachelor’s degree or more. Employers will hire more experienced candidates. Directors of manufacturing must have at least five years experience in managerial positions. Candidates should be able to adapt to a high learning curve.
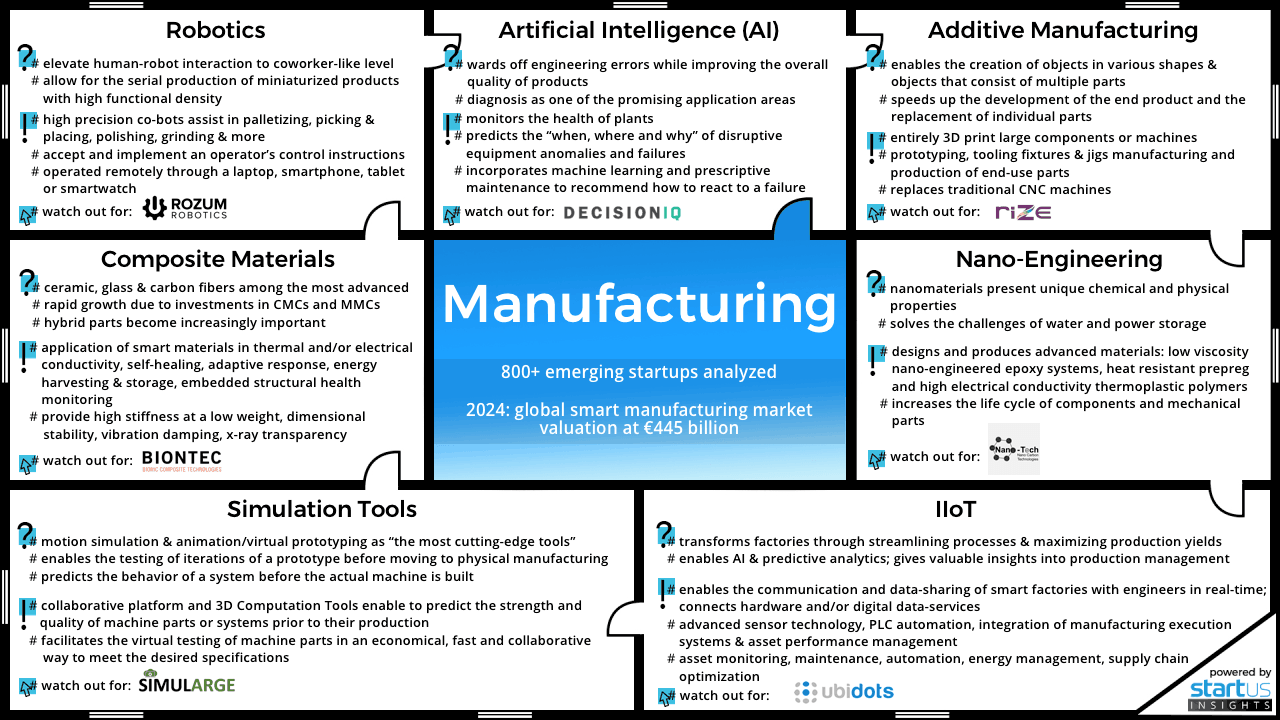
Duties of a manufacturing associate
Manufacturing associates have many different duties. However, most of them involve repetitive motions and assembly lines. To avoid injury, associates must practice good body mechanics. They may have to lift heavy items or stand for long periods.
Manufacturing associates can perform a variety of tasks, including inspecting parts and reading engineering drawings. They also have to execute manufacturing documents. They need to coordinate with others on the team and produce reports. They need to be organised, detail-oriented, efficient communicators, and have prior experience in manufacturing.
Also, quality control is a major responsibility. They must have a good understanding of the manufacturing process and must be able check whether products comply with company standards. Additionally, they will need to inspect finished products and find any defects.
Qualifications for a job director of manufacturing
A job as a director of manufacturing requires you to be in charge of all the operations in a manufacturing unit, from creating schedules to overseeing the production of products. You will be responsible for maintaining high quality standards and developing new techniques and ideas to reduce costs. In addition, you will also be responsible for evaluating the performance of all staff members. For a job as a director in manufacturing, you will need to demonstrate leadership, organizational skills and problem solving.
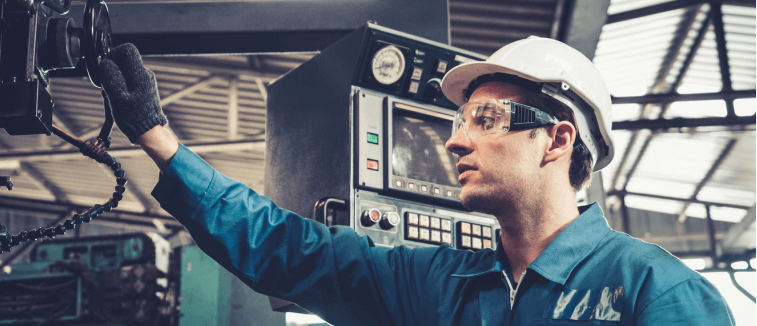
You will be a manufacturing director and work closely with engineers and designers to create products and services. It is important to be able to communicate effectively with others to ensure everyone understands what their role is and gets along well. Your ability to communicate effectively is key to your ability to oversee the entire business. As a director for manufacturing, you will need to mentor and coach employees. As an example, you'll need to give training to employees about safety protocols, risk mitigation and new equipment.
FAQ
Why is logistics important for manufacturing?
Logistics is an integral part of every business. They can help you achieve great success by helping you manage product flow from raw material to finished goods.
Logistics plays a significant role in reducing cost and increasing efficiency.
What skills are required to be a production manager?
Being a production planner is not easy. You need to be organized and flexible. Effective communication with clients and colleagues is essential.
What is meant by manufacturing industries?
Manufacturing Industries is a group of businesses that produce goods for sale. Consumers are those who purchase these products. These companies use various processes such as production, distribution, retailing, management, etc., to fulfill this purpose. These companies produce goods using raw materials and other equipment. This covers all types of manufactured goods including clothing, food, building supplies and furniture, as well as electronics, tools, machinery, vehicles and pharmaceuticals.
What are the responsibilities for a manufacturing manager
Manufacturing managers must ensure that manufacturing processes are efficient, effective, and cost-effective. They should also be aware and responsive to any company problems.
They should also know how to communicate with other departments such as sales and marketing.
They should be informed about industry trends and be able make use of this information to improve their productivity and efficiency.
What are the 4 types of manufacturing?
Manufacturing is the process of transforming raw materials into useful products using machines and processes. It involves many different activities such as designing, building, testing, packaging, shipping, selling, servicing, etc.
What are the responsibilities of a production planner
A production planner ensures all aspects of the project are delivered on time, within budget, and within scope. They also ensure the quality of the product and service meets the client's requirements.
Statistics
- It's estimated that 10.8% of the U.S. GDP in 2020 was contributed to manufacturing. (investopedia.com)
- (2:04) MTO is a production technique wherein products are customized according to customer specifications, and production only starts after an order is received. (oracle.com)
- [54][55] These are the top 50 countries by the total value of manufacturing output in US dollars for its noted year according to World Bank.[56] (en.wikipedia.org)
- According to the United Nations Industrial Development Organization (UNIDO), China is the top manufacturer worldwide by 2019 output, producing 28.7% of the total global manufacturing output, followed by the United States, Japan, Germany, and India.[52][53] (en.wikipedia.org)
- In the United States, for example, manufacturing makes up 15% of the economic output. (twi-global.com)
External Links
How To
Six Sigma: How to Use it in Manufacturing
Six Sigma can be described as "the use of statistical process control (SPC), techniques to achieve continuous improvement." It was developed by Motorola's Quality Improvement Department at their plant in Tokyo, Japan, in 1986. Six Sigma's main goal is to improve process quality by standardizing processes and eliminating defects. This method has been adopted by many companies in recent years as they believe there are no perfect products or services. Six Sigma's primary goal is to reduce variation from the average value of production. It is possible to measure the performance of your product against an average and find the percentage of time that it differs from the norm. If there is a significant deviation from the norm, you will know that something needs to change.
Understanding how variability works in your company is the first step to Six Sigma. Once you have this understanding, you will need to identify sources and causes of variation. You'll also want to determine whether these variations are random or systematic. Random variations are caused when people make mistakes. While systematic variations are caused outside of the process, they can occur. These are, for instance, random variations that occur when widgets are made and some fall off the production line. If however, you notice that each time you assemble a widget it falls apart in exactly the same spot, that is a problem.
Once you've identified the problem areas you need to find solutions. That solution might involve changing the way you do things or redesigning the process altogether. Test them again once you've implemented the changes. If they don't work you need to rework them and come up a better plan.