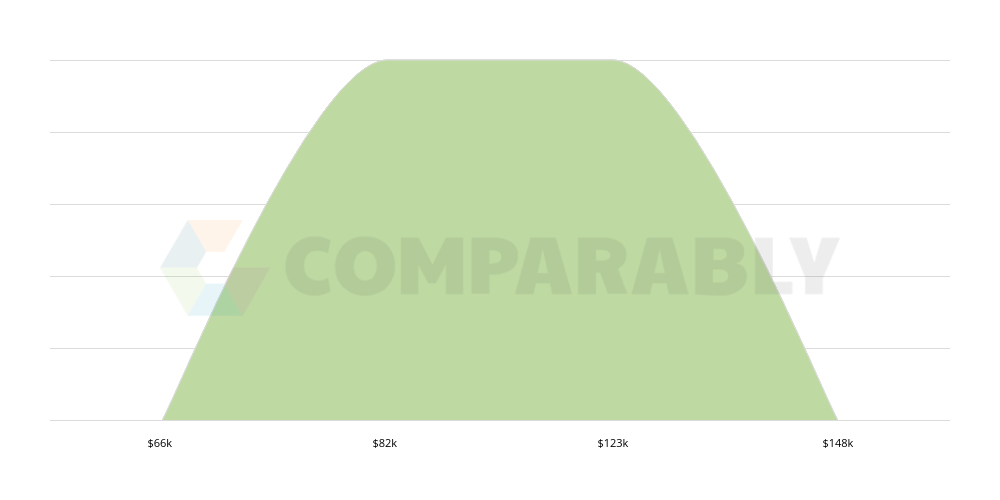
Over the years, global supply chain have experienced many changes. They have moved from being primarily an industrial problem to becoming a serious economic threat. It is a good idea to keep an eye on the latest developments. Global supply chains can be complex and interconnected in many ways.
Global value chains are a mix of flows, intangibles and capital. They are the result of economies, specialization, long-standing relationships, scale, and relationships. Some value chains are capital-intensive while others are more localized.
Global supply chains are becoming more complex, dynamic, and multidimensional. They are an integral part of global trade as well as the functioning of countries. They are also vulnerable for disruptions. These disruptions are either short-term or long-lasting. It is essential to have a diverse, flexible, and resilient supply network in order to avoid these disruptions. This requires a holistic approach that includes structural reform and strategic initiatives as well as prudent risk management. It is important to identify and assess the greatest challenges in order to build a supply chain that can withstand any future storms.
Companies should assess the risks of supply-chain disruptions and also consider the risks associated manufacturing, energy, and materials. They should also simulate severe supply-and-demand disruptions to evaluate their impact. They should also review their inventories of critical materials and make sure they have sufficient supply for foreseeable demand. A strategic strategy is required to develop a resilient supply network. This may involve reprioritizing production and shifting manufacturing to more flexible places, improving supply chain technology, and implementing guaranteed sources.
The COVID-19 pandemic caused significant disruptions to global supply chains. Many countries imposed tariffs against one another, while other countries imposed sanctions on the other. These tariffs have caused trade frictions which made it more difficult to sell certain products to China or other countries. These disruptions have increased price inflation. However, these disruptions have made companies more aware and re-examined the design and implementation aspects of their supply channels.
The COVID-19 outbreak caused disruption in global supply networks, but its effects still are being felt. For example the Suez Canal blockage caused disruptions in supply chain for up to six weeks. This has also led to a dramatic increase in freight costs. The UK has seen an increase in inflation of 9% annually.
It is difficult not to notice that China and America are at the center of a trade war. Supply chain leaders need to question the logic behind relying so heavily upon outsourced networks. They need to consider the risks of labor shortages resulting from economic shocks. Leaders in supply chains should also be aware of the potential benefits of cross-border finance as well as regulation that can help expand global integration.
Despite all the turmoil, we are still connected to the rest of the world. Companies that are more holistic in their supply chain management will reap the benefits from global integration.
FAQ
What's the difference between Production Planning & Scheduling?
Production Planning (PP), is the process of deciding what production needs to take place at any given time. This is accomplished by forecasting the demand and identifying production resources.
Scheduling is the process of assigning specific dates to tasks so they can be completed within the specified timeframe.
What does it take for a logistics enterprise to succeed?
To run a successful logistics company, you need a lot knowledge and skills. For clients and suppliers to be successful, you need to have excellent communication skills. You will need to know how to interpret data and draw conclusions. You must be able and able to handle stress situations and work under pressure. You must be creative and innovative to develop new ideas to improve efficiency. You will need strong leadership skills to motivate and direct your team members towards achieving their organizational goals.
To meet tight deadlines, you must also be efficient and organized.
What is the difference between a production planner and a project manager?
The main difference between a production planner and a project manager is that a project manager is usually the person who plans and organizes the entire project, whereas a production planner is mainly involved in the planning stage of the project.
How can manufacturing avoid production bottlenecks
You can avoid bottlenecks in production by making sure that everything runs smoothly throughout the production cycle, from the moment you receive an order to the moment the product is shipped.
This includes planning for capacity requirements as well as quality control measures.
Continuous improvement techniques like Six Sigma are the best way to achieve this.
Six Sigma can be used to improve the quality and decrease waste in all areas of your company.
It focuses on eliminating variation and creating consistency in your work.
What does it mean to warehouse?
A warehouse, or storage facility, is where goods are stored prior to being sold. You can have it indoors or outdoors. It could be one or both.
Statistics
- In 2021, an estimated 12.1 million Americans work in the manufacturing sector.6 (investopedia.com)
- (2:04) MTO is a production technique wherein products are customized according to customer specifications, and production only starts after an order is received. (oracle.com)
- According to a Statista study, U.S. businesses spent $1.63 trillion on logistics in 2019, moving goods from origin to end user through various supply chain network segments. (netsuite.com)
- You can multiply the result by 100 to get the total percent of monthly overhead. (investopedia.com)
- Job #1 is delivering the ordered product according to specifications: color, size, brand, and quantity. (netsuite.com)
External Links
How To
How to use Lean Manufacturing in the production of goods
Lean manufacturing refers to a method of managing that seeks to improve efficiency and decrease waste. It was developed in Japan between 1970 and 1980 by Taiichi Ohno. TPS founder Kanji Tyoda gave him the Toyota Production System, or TPS award. Michael L. Watkins published the first book on lean manufacturing in 1990.
Lean manufacturing is often defined as a set of principles used to improve the quality, speed, and cost of products and services. It emphasizes the elimination and minimization of waste in the value stream. Lean manufacturing can be described as just-in–time (JIT), total productive maintenance, zero defect (TPM), or even 5S. Lean manufacturing emphasizes reducing non-value-added activities like inspection, rework and waiting.
Lean manufacturing can help companies improve their product quality and reduce costs. Additionally, it helps them achieve their goals more quickly and reduces employee turnover. Lean manufacturing has been deemed one of the best ways to manage the entire value-chain, including customers, distributors as well retailers and employees. Lean manufacturing can be found in many industries. Toyota's philosophy is the foundation of its success in automotives, electronics and appliances, healthcare, chemical engineers, aerospace, paper and food, among other industries.
Lean manufacturing includes five basic principles:
-
Define Value - Identify the value your business adds to society and what makes you different from competitors.
-
Reduce Waste - Eliminate any activity that doesn't add value along the supply chain.
-
Create Flow – Ensure that work flows smoothly throughout the process.
-
Standardize & simplify - Make processes consistent and repeatable.
-
Build relationships - Develop and maintain personal relationships with both your internal and external stakeholders.
Lean manufacturing is not a new concept, but it has been gaining popularity over the last few years due to a renewed interest in the economy following the global financial crisis of 2008. To increase their competitiveness, many businesses have turned to lean manufacturing. Many economists believe lean manufacturing will play a major role in economic recovery.
Lean manufacturing, which has many benefits, is now a standard practice in the automotive industry. These include higher customer satisfaction, lower inventory levels, lower operating expenses, greater productivity, and improved overall safety.
You can apply Lean Manufacturing to virtually any aspect of your organization. It is especially useful for the production aspect of an organization, as it ensures that every step in the value chain is efficient and effective.
There are three main types in lean manufacturing
-
Just-in Time Manufacturing: This lean manufacturing method is commonly called "pull systems." JIT is a process in which components can be assembled at the point they are needed, instead of being made ahead of time. This strategy aims to decrease lead times, increase availability of parts and reduce inventory.
-
Zero Defects Manufacturing - ZDM: ZDM focuses its efforts on making sure that no defective units leave a manufacturing facility. If a part is required to be repaired on the assembly line, it should not be scrapped. This applies to finished goods that may require minor repairs before shipment.
-
Continuous Improvement: Continuous Improvement aims to improve efficiency by continually identifying problems and making adjustments to eliminate or minimize waste. Continuous improvement refers to continuous improvement of processes as well people and tools.