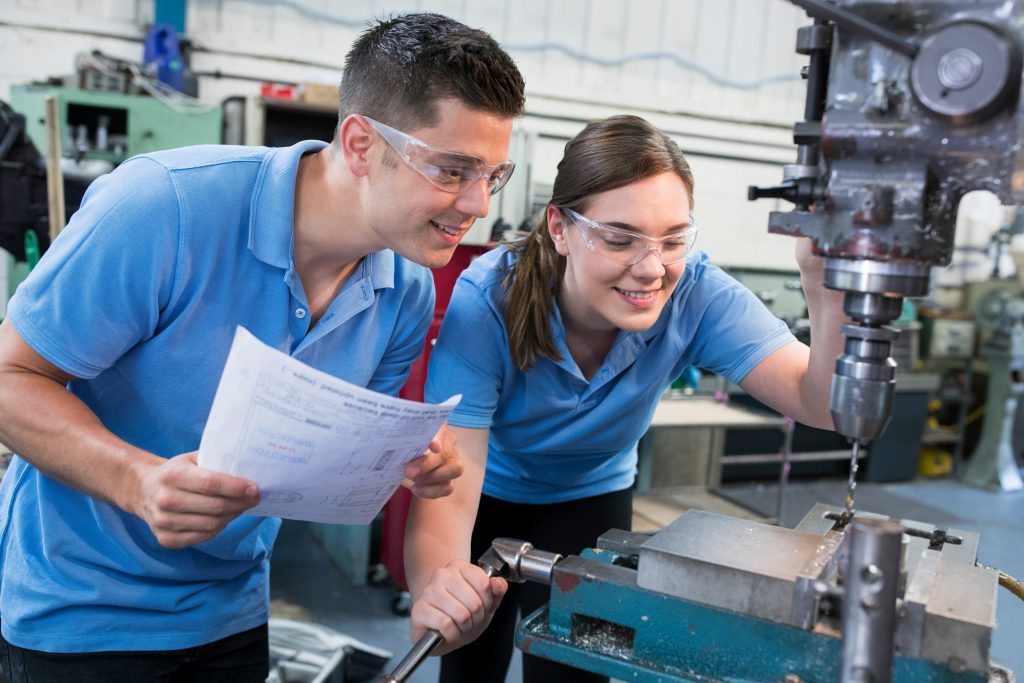
A cost estimate is required for almost everything a company does. This task is performed by cost estimators. They are responsible for determining the costs associated with manufacturing and developing new products or services. They also need to assess the cost of building new structures. This includes analysing the labor and materials costs.
Construction companies employ many cost estimators. They are expected to be well-versed in construction processes and methods. They must also be familiar with computer-aided designs (CAD) software. This software helps to improve efficiency in design and manufacturing. It is also necessary for cost estimators to be able read data from databases. They can also use Microsoft Excel and other software.
Cost estimators work with other professionals to make accurate cost estimates. They review the project blueprints and site conditions to determine the cost of each component. They may also work with engineers to determine the gauges and machining operations required.
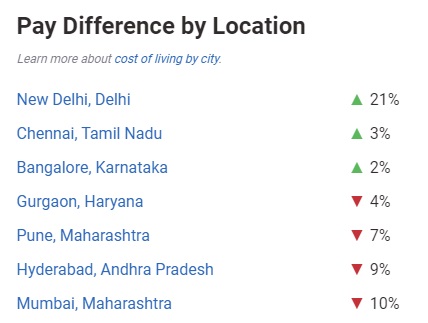
Cost estimators should be detail-oriented, assertive and reliable. They must be able and willing to analyse difficult information. They must be able to communicate clearly and accurately their findings. They must be able communicate effectively with clients or professionals.
Cost estimators are typically assigned to the engineering or cost departments of a company. They should have a solid knowledge of science and math. They should be proficient in computer software such as CAD, BIM and commercial. They might also need to complete a certification course. Certified Cost Estimator/Analysts(CCEA), Professional Estimator/Analysts and Certified Professional Estimators may be required.
Cost estimators might be experts in particular services or industries. Some individuals specialize in building or construction costs, while others focus on software development costs. You can also search for jobs as cost estimators in other areas such as automotive repair and maintenance and building construction.
These people communicate with engineers, clients, or suppliers. They are also well-versed in industry terminology. Before preparing cost estimates, they also have a lot of knowledge. These individuals are skilled in cost estimations and many others conduct studies to determine the effects of different processes on prices, and then find ways to reduce them.
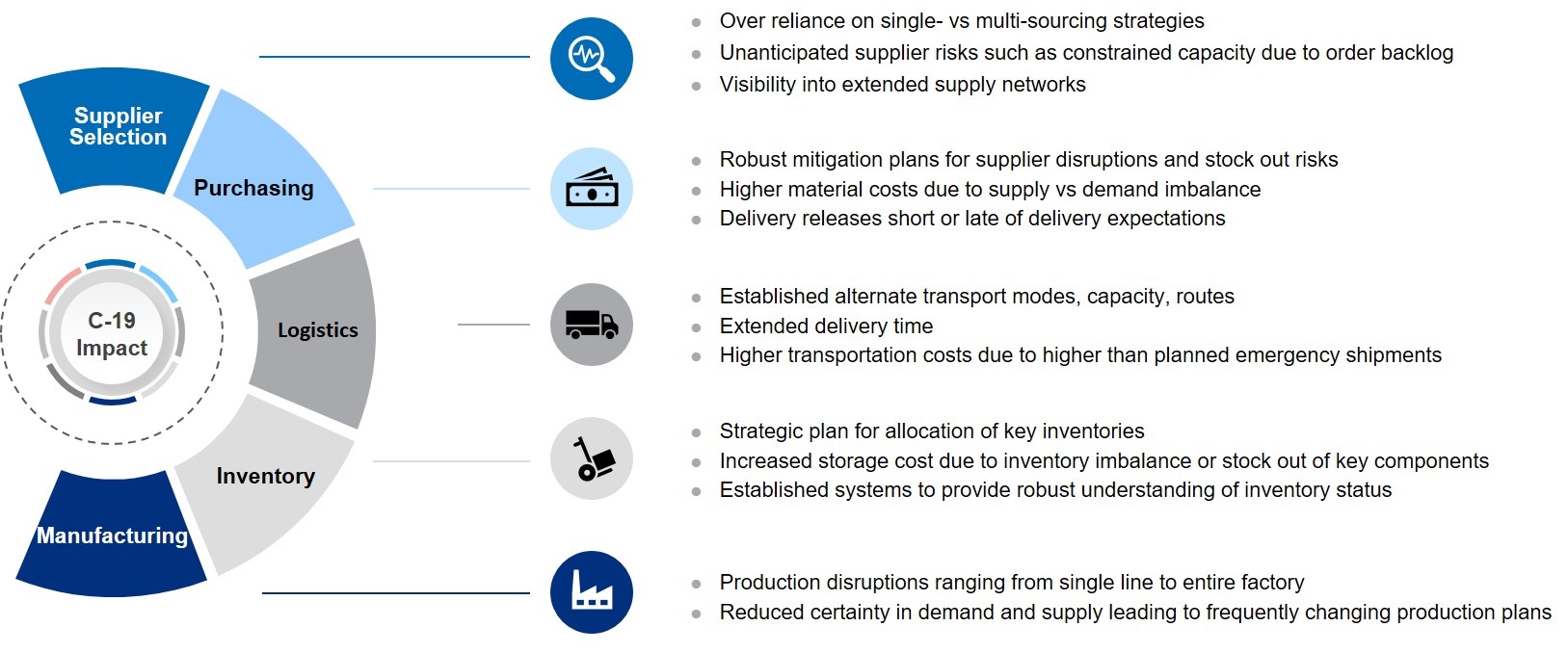
The industry may require job applicants to have a bachelor’s degree. They might also be required to do an internship. They can also take advantage of cooperative education programs. A degree in building construction, or construction management is also an advantage for construction companies.
They work in construction and other manufacturing companies. They assist companies in making accurate estimates that will allow them to submit profitable bids. They also analyze data concerning the supply chain and other factors that can affect costs. You can also hire cost estimators to work on government programs. They may also be required to redesign existing products.
Cost estimators should have a good understanding of computer-aided planning (CAD) software. They can also be trained in the use of automatic cost estimation software.
FAQ
How important is automation in manufacturing?
Not only is automation important for manufacturers, but it's also vital for service providers. It enables them to provide services faster and more efficiently. They can also reduce their costs by reducing human error and improving productivity.
How can manufacturing prevent production bottlenecks?
You can avoid bottlenecks in production by making sure that everything runs smoothly throughout the production cycle, from the moment you receive an order to the moment the product is shipped.
This includes both quality control and capacity planning.
Continuous improvement techniques like Six Sigma are the best way to achieve this.
Six Sigma Management System is a method to increase quality and reduce waste throughout your organization.
It focuses on eliminating variation and creating consistency in your work.
What skills does a production planner need?
A production planner must be organized, flexible, and able multitask to succeed. Effective communication with clients and colleagues is essential.
What are the 7 R's of logistics?
The acronym 7R's of Logistic is an acronym that stands for seven fundamental principles of logistics management. It was developed and published by the International Association of Business Logisticians in 2004 as part of the "Seven Principles of Logistics Management".
The acronym is composed of the following letters.
-
Responsive - ensure all actions are legal and not harmful to others.
-
Reliable: Have faith in your ability or the ability to honor any promises made.
-
Be responsible - Use resources efficiently and avoid wasting them.
-
Realistic - Consider all aspects of operations, including environmental impact and cost effectiveness.
-
Respectful - Treat people fairly and equitably
-
Be resourceful: Look for opportunities to save money or increase productivity.
-
Recognizable - provide customers with value-added services.
Statistics
- You can multiply the result by 100 to get the total percent of monthly overhead. (investopedia.com)
- According to a Statista study, U.S. businesses spent $1.63 trillion on logistics in 2019, moving goods from origin to end user through various supply chain network segments. (netsuite.com)
- In 2021, an estimated 12.1 million Americans work in the manufacturing sector.6 (investopedia.com)
- It's estimated that 10.8% of the U.S. GDP in 2020 was contributed to manufacturing. (investopedia.com)
- [54][55] These are the top 50 countries by the total value of manufacturing output in US dollars for its noted year according to World Bank.[56] (en.wikipedia.org)
External Links
How To
How to use the Just In-Time Production Method
Just-intime (JIT), which is a method to minimize costs and maximize efficiency in business process, is one way. It is a process where you get the right amount of resources at the right moment when they are needed. This means that you only pay for what you actually use. Frederick Taylor, a 1900s foreman, first coined the term. He noticed that workers were often paid overtime when they had to work late. He decided that workers would be more productive if they had enough time to complete their work before they started to work.
The idea behind JIT is that you should plan ahead and have everything ready so you don't waste money. The entire project should be looked at from start to finish. You need to ensure you have enough resources to tackle any issues that might arise. You can anticipate problems and have enough equipment and people available to fix them. This will prevent you from spending extra money on unnecessary things.
There are many types of JIT methods.
-
Demand-driven: This JIT is where you place regular orders for the parts/materials that are needed for your project. This will allow to track how much material has been used up. This will let you know how long it will be to produce more.
-
Inventory-based: You stock materials in advance to make your projects easier. This allows you to forecast how much you will sell.
-
Project-driven: This approach involves setting aside sufficient funds to cover your project's costs. Once you have an idea of how much material you will need, you can purchase the necessary materials.
-
Resource-based JIT: This type of JIT is most commonly used. Here, you allocate certain resources based on demand. For instance, if you have a lot of orders coming in, you'll assign more people to handle them. You'll have fewer orders if you have fewer.
-
Cost-based : This is similar in concept to resource-based. But here, you aren't concerned about how many people your company has but how much each individual costs.
-
Price-based: This is a variant of cost-based. However, instead of focusing on the individual workers' costs, this looks at the total price of the company.
-
Material-based: This is quite similar to cost-based, but instead of looking at the total cost of the company, you're concerned with how much raw materials you spend on average.
-
Time-based JIT: A variation on resource-based JIT. Instead of focusing on the cost of each employee, you will focus on the time it takes to complete a project.
-
Quality-based JIT is another variant of resource-based JIT. Instead of thinking about the cost of each employee or the time it takes to produce something, you focus on how good your product quality.
-
Value-based JIT: One of the most recent forms of JIT. You don't worry about whether the products work or if they meet customer expectations. Instead, you're focused on how much value you add to the market.
-
Stock-based: This is an inventory-based method that focuses on the actual number of items being produced at any given time. It's useful when you want maximum production and minimal inventory.
-
Just-in-time (JIT) planning: This is a combination of JIT and supply chain management. It refers to the process of scheduling the delivery of components as soon as they are ordered. It's important because it reduces lead times and increases throughput.