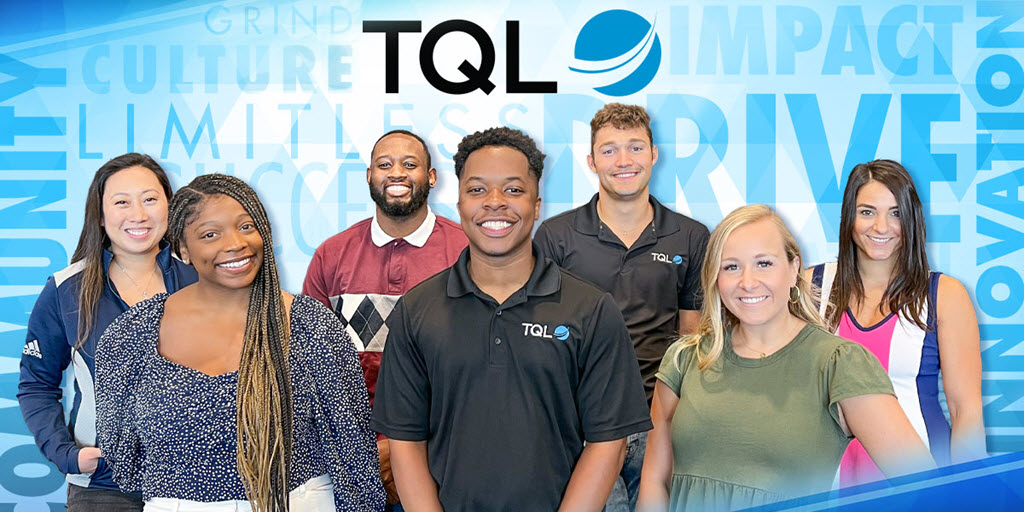
Industrial engineers use their expertise in mathematics and engineering to optimize the operation of a company. This includes creating blueprints for machinery, analysing data and designing procedures. A skilled industrial engineer will be able to help management make decisions that will increase the efficiency of the company.
Typical tasks of an industrial engineering technician include: performing time and motion studies to enhance productivity, evaluating performance and implementing changes. They might also be asked to analyze data related to an industrial safety and health program.
Additionally, they are responsible for technical tasks like preparing diagrams and graphs to show the flow of a process. They perform various quality checks on products to ensure they meet the required standards.
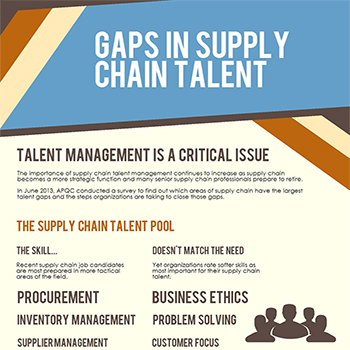
Some of the most popular job functions of an industrial engineer include: planning workflow, analyzing production costs, gauging prototypes, assessing equipment capacities, and developing efficient operating procedures. You can find them in many industries including aerospace, automotive, electronics, food and pharmaceuticals. Most work full-time. Their average annual salary is $53,000. But, people with more education or work experience might earn a higher income.
To become an industrial engineer, you don't need to have a degree. However, a strong math skills, critical thinking, and an eye for detail are vital. They must be able and willing to communicate with employees and to observe work processes.
A skilled industrial engineer technician will recognize and be able to implement the necessary factors in the most effective workflow. For example, they should understand the importance to reduce waste materials and other inefficient practices. As a result, they are able to find ways to implement improvements in the workplace, and to save the organization money in the long run.
They are likely the first ones in the organization to experiment with new ideas. A strategic outline is one of the best ways to accomplish this. It's like putting together the pieces of an enormous puzzle.
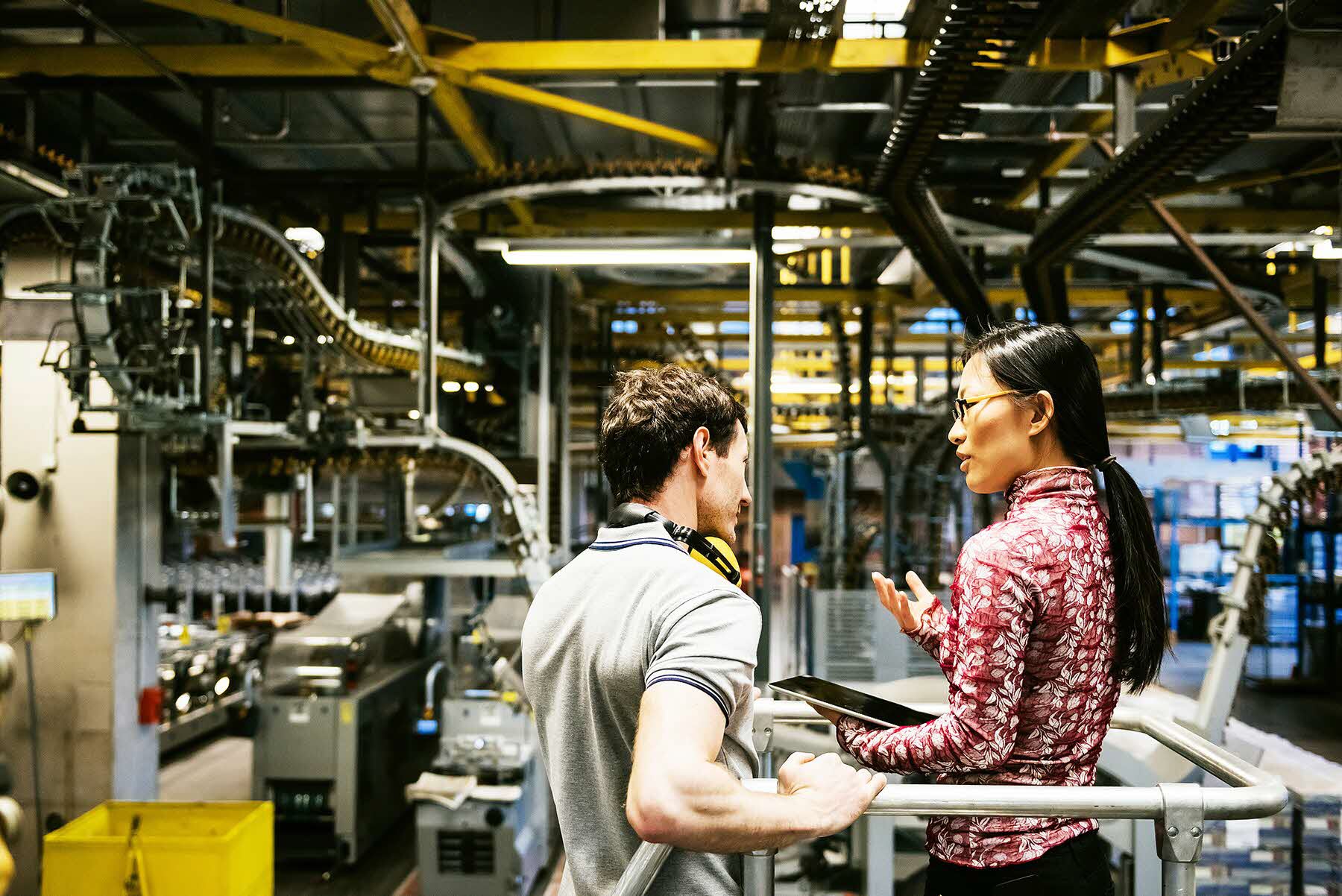
Another interesting job function of an industrial engineer is improving the quality of the output produced. While the number of jobs will be decreased by the increasing automation of industries, the role of industrial engineering technicians will be bolstered by a growing focus on cost control.
An engineer might use a motion and time study to determine how long it takes for a task to be completed. This is the most accurate way to gauge the system's performance. To calculate a standard rate of production, they might use the data from this study. These findings will be used in order to make improvements to an operation's operations.
Many universities offer a wide variety of courses in industrial engineering technology, including Liberty University. This program teaches problem-solving skills as well as how to work with others to achieve their goals.
FAQ
What kind of jobs are there in logistics?
Logistics can offer many different jobs. Some examples are:
-
Warehouse workers – They load, unload and transport pallets and trucks.
-
Transportation drivers – These drivers drive trucks and wagons to transport goods and pick up the goods.
-
Freight handlers: They sort and package freight in warehouses.
-
Inventory managers – They manage the inventory in warehouses.
-
Sales reps - They sell products and services to customers.
-
Logistics coordinators – They plan and coordinate logistics operations.
-
Purchasing agents are those who purchase goods and services for the company.
-
Customer service representatives - Answer calls and email from customers.
-
Ship clerks - They issue bills and process shipping orders.
-
Order fillers are people who fill orders based only on what was ordered.
-
Quality control inspectors – They inspect incoming and outgoing products to ensure that there are no defects.
-
Others - There is a variety of other jobs in logistics. These include transportation supervisors and cargo specialists.
What is the role and responsibility of a Production Planner?
Production planners ensure all aspects of the project are delivered within time and budget. They also ensure that the product/service meets the client’s needs.
How can we reduce manufacturing overproduction?
Improved inventory management is the key to reducing overproduction. This would reduce time spent on activities such as purchasing, stocking, and maintaining excess stock. This would allow us to use our resources for more productive tasks.
You can do this by adopting a Kanban method. A Kanban board can be used to monitor work progress. Kanban systems are where work items travel through a series of states until reaching their final destination. Each state represents a different priority level.
As an example, if work is progressing from one stage of the process to another, then the current task is complete and can be transferred to the next. If a task is still in its beginning stages, it will continue to be so until it reaches the end.
This allows work to move forward and ensures that no work is missed. With a Kanban board, managers can see exactly how much work is being done at any given moment. This allows them the ability to adjust their workflow using real-time data.
Another way to control inventory levels is to implement lean manufacturing. Lean manufacturing emphasizes eliminating waste in all phases of production. Anything that doesn't add value to the product is considered waste. The following are examples of common waste types:
-
Overproduction
-
Inventory
-
Packaging not required
-
Excess materials
These ideas can help manufacturers improve efficiency and reduce costs.
What is the distinction between Production Planning or Scheduling?
Production Planning (PP), is the process of deciding what production needs to take place at any given time. Forecasting demand is one way to do this.
Scheduling is the process that assigns dates to tasks so they can get completed within a given timeframe.
Why automate your warehouse
Modern warehousing is becoming more automated. E-commerce has increased the demand for quicker delivery times and more efficient processes.
Warehouses should be able adapt quickly to new needs. In order to do this, they need to invest in technology. Automation of warehouses offers many benefits. Here are some reasons why it's worth investing in automation:
-
Increases throughput/productivity
-
Reduces errors
-
Improves accuracy
-
Safety is boosted
-
Eliminates bottlenecks
-
Allows companies scale more easily
-
This makes workers more productive
-
This gives you visibility into what happens in the warehouse
-
Enhances customer experience
-
Improves employee satisfaction
-
Reducing downtime and increasing uptime
-
High quality products delivered on-time
-
Eliminates human error
-
It ensures compliance with regulations
What does manufacturing mean?
Manufacturing Industries are businesses that produce products for sale. The people who buy these products are called consumers. These companies use various processes such as production, distribution, retailing, management, etc., to fulfill this purpose. They make goods from raw materials with machines and other equipment. This covers all types of manufactured goods including clothing, food, building supplies and furniture, as well as electronics, tools, machinery, vehicles and pharmaceuticals.
Statistics
- Many factories witnessed a 30% increase in output due to the shift to electric motors. (en.wikipedia.org)
- Job #1 is delivering the ordered product according to specifications: color, size, brand, and quantity. (netsuite.com)
- It's estimated that 10.8% of the U.S. GDP in 2020 was contributed to manufacturing. (investopedia.com)
- In 2021, an estimated 12.1 million Americans work in the manufacturing sector.6 (investopedia.com)
- (2:04) MTO is a production technique wherein products are customized according to customer specifications, and production only starts after an order is received. (oracle.com)
External Links
How To
Six Sigma in Manufacturing:
Six Sigma can be described as "the use of statistical process control (SPC), techniques to achieve continuous improvement." Motorola's Quality Improvement Department in Tokyo, Japan developed Six Sigma in 1986. Six Sigma's basic concept is to improve quality and eliminate defects through standardization. This method has been adopted by many companies in recent years as they believe there are no perfect products or services. Six Sigma aims to reduce variation in the production's mean value. This means that if you take a sample of your product, then measure its performance against the average, you can find out what percentage of the time the process deviates from the norm. If it is too large, it means that there are problems.
Understanding the dynamics of variability within your business is the first step in Six Sigma. Once you have this understanding, you will need to identify sources and causes of variation. It is important to identify whether the variations are random or systemic. Random variations happen when people make errors; systematic variations are caused externally. If you make widgets and some of them end up on the assembly line, then those are considered random variations. You might notice that your widgets always fall apart at the same place every time you put them together.
Once you identify the problem areas, it is time to create solutions. This could mean changing your approach or redesigning the entire process. To verify that the changes have worked, you need to test them again. If they don’t work, you’ll need to go back and rework the plan.