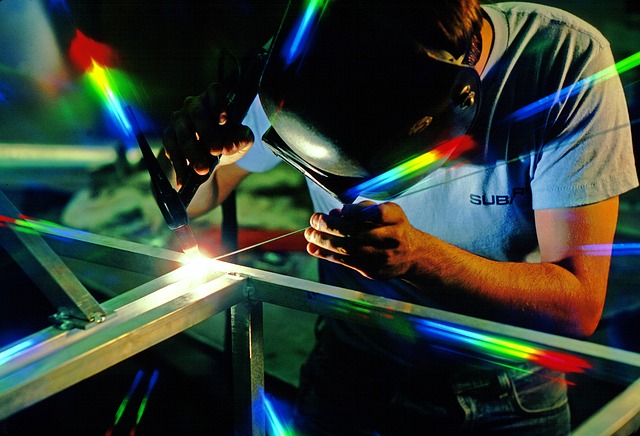
Supply chain learning is a process that improves a company's supply chains through knowledge and expertise. This covers everything from logistics to warehousing inventory and procurement management. Supply chain learning aims to improve a company's processes such as delivery of products on time at the right price.
There are many ways to learn supply chain management, including on-campus courses at colleges and universities or online learning platforms. Students can take classes according to their schedule on these platforms. They are also a good way to earn certificates for supply chain subjects or career paths.
The UT Dallas Supply Chain Learning Center is a great resource for students. They can choose from a variety courses and engage in an online discussion with professors or other students. The UT Dallas Supply Chain Learning Center is a great resource for meeting other supply chain professionals, and finding career opportunities in the industry.
The supply chain is made up of many companies who all play a role in the success of any product. This course examines the impact of digital technology on how businesses structure and operate their supply chains.
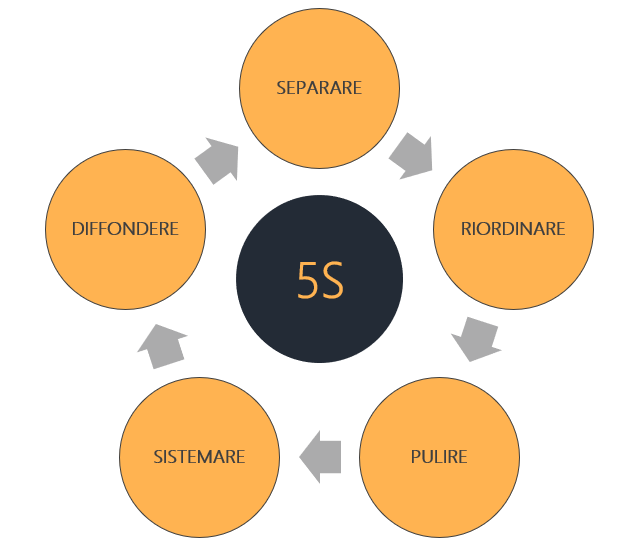
This course is ideal for anyone who wants to learn more about the future of supply chains and how they will affect their professional lives, whether or not they work in large enterprises or small-to medium-sized businesses.
Coursera's supply chain course offers a self-paced, free option for those who wish to learn the fundamentals of supply chain management. It contains short videos and interactive exercises that give a comprehensive introduction to the field.
Coursera's course on supply chains also includes case study examples that illustrate how supply-chains are changing because of technological advancements as well as economic factors.
Coursera’s Online Platform allows students the opportunity to complete courses from top universities in their own homes or offices. The platform is user-friendly and includes interactive video lessons, exercise, quizzes, etc.
Supply Chain Coursera provides a free high-quality, online education platform in partnership with top universities from around the globe. The platform's course offerings are provided by faculty from leading academic institutions and taught by experts.
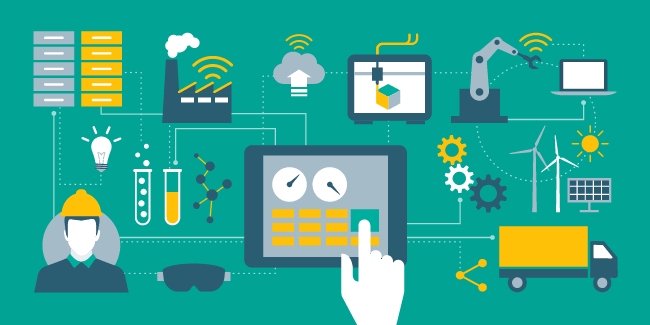
This free course will teach students the fundamentals of supply chains and their importance to an organization. Students will also learn how to utilize the most important supply chain management technologies and systems.
Learning how to manage information, product data and financial data is another important aspect of the course. This is essential for anyone who wants a career as a supply-chain manager.
Supply chain management is an ever-evolving field, which requires continuous training to stay competitive and current. This is why it's important to invest in quality supply chain management training for your employees. You can help your employees succeed by providing the training they need and creating a supportive work environment.
FAQ
How can manufacturing prevent production bottlenecks?
The key to avoiding bottlenecks in production is to keep all processes running smoothly throughout the entire production cycle, from the time you receive an order until the time when the product ships.
This includes both quality control and capacity planning.
This can be done by using continuous improvement techniques, such as Six Sigma.
Six Sigma is a management system used to improve quality and reduce waste in every aspect of your organization.
It seeks to eliminate variation and create consistency in your work.
What is meant by manufacturing industries?
Manufacturing Industries are those businesses that make products for sale. The people who buy these products are called consumers. These companies employ many processes to achieve this purpose, such as production and distribution, retailing, management and so on. These companies produce goods using raw materials and other equipment. This includes all types manufactured goods such as clothing, building materials, furniture, electronics, tools and machinery.
What are the jobs in logistics?
There are many types of jobs in logistics. Some of them are:
-
Warehouse workers: They load and unload trucks, pallets, and other cargo.
-
Transportation drivers - They drive trucks and trailers to deliver goods and carry out pick-ups.
-
Freight handlers – They sort and package freight at warehouses.
-
Inventory managers – They manage the inventory in warehouses.
-
Sales representatives: They sell products to customers.
-
Logistics coordinators: They plan and manage logistics operations.
-
Purchasing agents - They purchase goods and services needed for company operations.
-
Customer service representatives are available to answer customer calls and emails.
-
Shipping clerks – They process shipping orders, and issue bills.
-
Order fillers - They fill orders based on what is ordered and shipped.
-
Quality control inspectors are responsible for inspecting incoming and outgoing products looking for defects.
-
Others - There is a variety of other jobs in logistics. These include transportation supervisors and cargo specialists.
What skills is required for a production planner?
Being a production planner is not easy. You need to be organized and flexible. Also, you must be able and willing to communicate with clients and coworkers.
Are there any Manufacturing Processes that we should know before we can learn about Logistics?
No. It doesn't matter if you don't know anything about manufacturing before you learn about logistics. It is important to know about the manufacturing processes in order to understand how logistics works.
What do you mean by warehouse?
A warehouse or storage facility is where goods are stored before they are sold. It can be an outdoor or indoor area. Sometimes, it can be both an indoor and outdoor space.
Statistics
- It's estimated that 10.8% of the U.S. GDP in 2020 was contributed to manufacturing. (investopedia.com)
- Job #1 is delivering the ordered product according to specifications: color, size, brand, and quantity. (netsuite.com)
- According to the United Nations Industrial Development Organization (UNIDO), China is the top manufacturer worldwide by 2019 output, producing 28.7% of the total global manufacturing output, followed by the United States, Japan, Germany, and India.[52][53] (en.wikipedia.org)
- In the United States, for example, manufacturing makes up 15% of the economic output. (twi-global.com)
- In 2021, an estimated 12.1 million Americans work in the manufacturing sector.6 (investopedia.com)
External Links
How To
Six Sigma in Manufacturing
Six Sigma is defined as "the application of statistical process control (SPC) techniques to achieve continuous improvement." Motorola's Quality Improvement Department, Tokyo, Japan, developed it in 1986. The basic idea behind Six Sigma is to improve quality by improving processes through standardization and eliminating defects. Many companies have adopted Six Sigma in recent years because they believe that there are no perfect products and services. Six Sigma's main objective is to reduce variations from the production average. This means that if you take a sample of your product, then measure its performance against the average, you can find out what percentage of the time the process deviates from the norm. If it is too large, it means that there are problems.
Understanding the dynamics of variability within your business is the first step in Six Sigma. Once you understand this, you can then identify the causes of variation. It is important to identify whether the variations are random or systemic. Random variations are caused by human errors. Systematic variations can be caused by outside factors. Random variations would include, for example, the failure of some widgets to fall from the assembly line. But if you notice that every widget you make falls apart at the exact same place each time, this would indicate that there is a problem.
Once you've identified where the problems lie, you'll want to design solutions to eliminate those problems. That solution might involve changing the way you do things or redesigning the process altogether. Test them again once you've implemented the changes. If they didn't work, then you'll need to go back to the drawing board and come up with another plan.