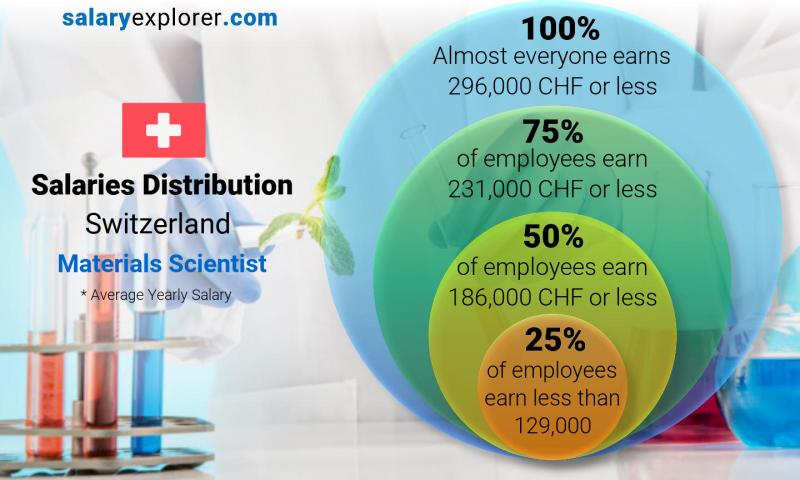
What salary is a robot engineer earning? Read on to learn about the job duties and responsibilities of a robotics engineer and the average salary for this career. Learn about the cost of living in different cities as well as the requirements for becoming a robotic engineer. A robotic engineer can enjoy many benefits.
Average salary for a robotics engineering engineer
The average salary of a robotic engineer will vary depending on many factors including your experience level and seniority. Engineers tend to earn more the higher they go up the hierarchy. Robotics engineers are the most highly paid tech workers and they enjoy their work. As the field continues to evolve, robotic engineers need to be problem solvers and innovative. Robotics engineering demands a variety of skills as well as an extensive knowledge of mathematics, science, and technology.
According to the National Careers Service (NCS), the average salary of a robotic engineer in a given year is PS27,500. Starting salaries may be higher if the job focuses on maintenance and operation. The company's size is another factor that can impact starting salaries. Larger companies tend to offer higher starting salaries.
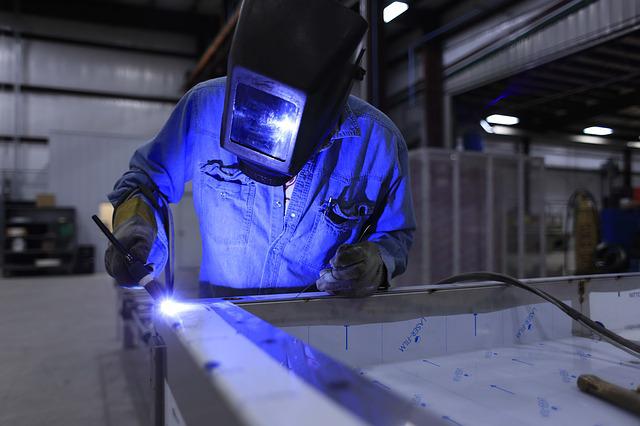
Robotics engineers have specific job responsibilities
Robotics engineers are responsible for programming and developing algorithms. They also do research on robotics and robot technology. They create new robotic systems and devise ways to improve their performance. They may also design robot systems for military defense, high-throughput operations, or other purposes. They should have strong communication skills and advanced mathematical concepts.
A robotics engineer must be highly skilled and innovative. They should be able anticipate future robotic requirements and collaborate well with others. They must also be able to collaborate with other engineers.
Cost of living across different cities
If you're looking for a job in robotic engineering, you'll want to consider a city with a high salary. Boston, for instance has a strong record in robotics, and is more affordable than other robotics cities. Boston is home for many robotics firms, including Boston Dynamics as well as iRobot.
An average robotics engineer earns $94,310 per annum, so you can still afford to live comfortably in your mid-career. Some cities have higher living costs than others.
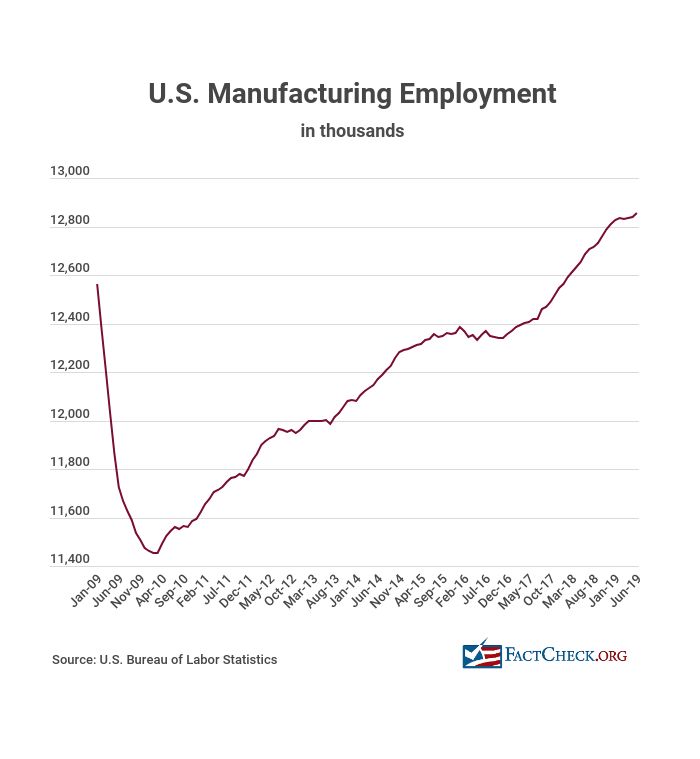
For robotics engineers, you need to have the required experience
Robotics engineers use computer software to create detailed designs and evaluate the performance of robotic systems. You will need to be analytical and able make compromises in order for the robots to function properly. Robotic engineers must also have excellent communication skills and be able to solve problems.
Engineers work in teams, working together on software development. In addition, they must have excellent communication skills so they can convey their thoughts to other experts in their field. The job requires you to regularly deliver reports to investors or other stakeholders. Because the development process is high-risk, robotics engineers need to be able to work in a team. One small mistake can lead to the destruction of an entire system.
FAQ
What are the responsibilities of a production planner
Production planners ensure that all project aspects are completed on time, within budget and within the scope. A production planner ensures that the service and product meet the client's expectations.
What are the 7 Rs of logistics?
The acronym 7Rs of Logistics refers to the seven core principles of logistics management. It was published in 2004 by the International Association of Business Logisticians as part of their "Seven Principles of Logistics Management" series.
The following letters form the acronym:
-
Responsive - ensure all actions are legal and not harmful to others.
-
Reliable: Have faith in your ability or the ability to honor any promises made.
-
It is reasonable to use resources efficiently and not waste them.
-
Realistic - Take into consideration all aspects of operations including cost-effectiveness, environmental impact, and other factors.
-
Respectful: Treat others with fairness and equity
-
Resourceful - look for opportunities to save money and increase productivity.
-
Recognizable is a company that provides customers with value-added solutions.
How can overproduction in manufacturing be reduced?
Better inventory management is key to reducing excess production. This would reduce time spent on activities such as purchasing, stocking, and maintaining excess stock. We could use these resources to do other productive tasks.
Kanban systems are one way to achieve this. A Kanban board, a visual display to show the progress of work, is called a Kanban board. Kanban systems allow work items to move through different states until they reach their final destination. Each state represents a different priority level.
When work is completed, it can be transferred to the next stage. It is possible to keep a task in the beginning stages until it gets to the end.
This keeps work moving and ensures no work is lost. A Kanban board allows managers to monitor how much work is being completed at any given moment. This information allows them to adjust their workflow based on real-time data.
Lean manufacturing, another method to control inventory levels, is also an option. Lean manufacturing works to eliminate waste throughout every stage of the production chain. Anything that doesn't add value to the product is considered waste. The following are examples of common waste types:
-
Overproduction
-
Inventory
-
Packaging not required
-
Excess materials
Manufacturers can reduce their costs and improve their efficiency by using these ideas.
Why is logistics so important in manufacturing?
Logistics are an essential component of any business. They are essential to any business's success.
Logistics are also important in reducing costs and improving efficiency.
What is the difference between Production Planning, Scheduling and Production Planning?
Production Planning (PP), also known as forecasting and identifying production capacities, is the process that determines what product needs to be produced at any particular time. This is accomplished by forecasting the demand and identifying production resources.
Scheduling refers the process by which tasks are assigned dates so that they can all be completed within the given timeframe.
Statistics
- (2:04) MTO is a production technique wherein products are customized according to customer specifications, and production only starts after an order is received. (oracle.com)
- In 2021, an estimated 12.1 million Americans work in the manufacturing sector.6 (investopedia.com)
- Job #1 is delivering the ordered product according to specifications: color, size, brand, and quantity. (netsuite.com)
- Many factories witnessed a 30% increase in output due to the shift to electric motors. (en.wikipedia.org)
- [54][55] These are the top 50 countries by the total value of manufacturing output in US dollars for its noted year according to World Bank.[56] (en.wikipedia.org)
External Links
How To
How to Use the Just-In-Time Method in Production
Just-in-time is a way to cut costs and increase efficiency in business processes. It's the process of obtaining the right amount and timing of resources when you need them. This means you only pay what you use. Frederick Taylor, a 1900s foreman, first coined the term. He observed how workers were paid overtime if there were delays in their work. He decided to ensure workers have enough time to do their jobs before starting work to improve productivity.
JIT is a way to plan ahead and make sure you don't waste any money. You should also look at the entire project from start to finish and make sure that you have sufficient resources available to deal with any problems that arise during the course of your project. If you expect problems to arise, you will be able to provide the necessary equipment and personnel to address them. This will ensure that you don't spend more money on things that aren't necessary.
There are many JIT methods.
-
Demand-driven: This is a type of JIT where you order the parts/materials needed for your project regularly. This will allow to track how much material has been used up. You'll also be able to estimate how long it will take to produce more.
-
Inventory-based: You stock materials in advance to make your projects easier. This allows for you to anticipate how much you can sell.
-
Project-driven : This is a method where you make sure that enough money is set aside to pay the project's cost. If you know the amount you require, you can buy the materials you need.
-
Resource-based JIT : This is probably the most popular type of JIT. Here, you allocate certain resources based on demand. For instance, if you have a lot of orders coming in, you'll assign more people to handle them. If you don't have many orders, you'll assign fewer people to handle the workload.
-
Cost-based: This is the same as resource-based except that you don't care how many people there are but how much each one of them costs.
-
Price-based: This is similar to cost-based but instead of looking at individual workers' salaries, you look at the total company price.
-
Material-based is an alternative to cost-based. Instead of looking at the total cost in the company, this method focuses on the average amount of raw materials that you consume.
-
Time-based: This is another variation of resource-based JIT. Instead of focusing only on how much each employee is costing, you should focus on how long it takes to complete your project.
-
Quality-based: This is yet another variation of resource-based JIT. Instead of worrying about the costs of each employee or how long it takes for something to be made, you should think about how quality your product is.
-
Value-based JIT is the newest form of JIT. In this case, you're not concerned with how well the products perform or whether they meet customer expectations. Instead, you focus on the added value that you provide to your market.
-
Stock-based: This is an inventory-based method that focuses on the actual number of items being produced at any given time. It's useful when you want maximum production and minimal inventory.
-
Just-in-time planning (JIT): This is a combination JIT and supply-chain management. It is the process that schedules the delivery of components within a short time of their order. It's important as it reduces leadtimes and increases throughput.