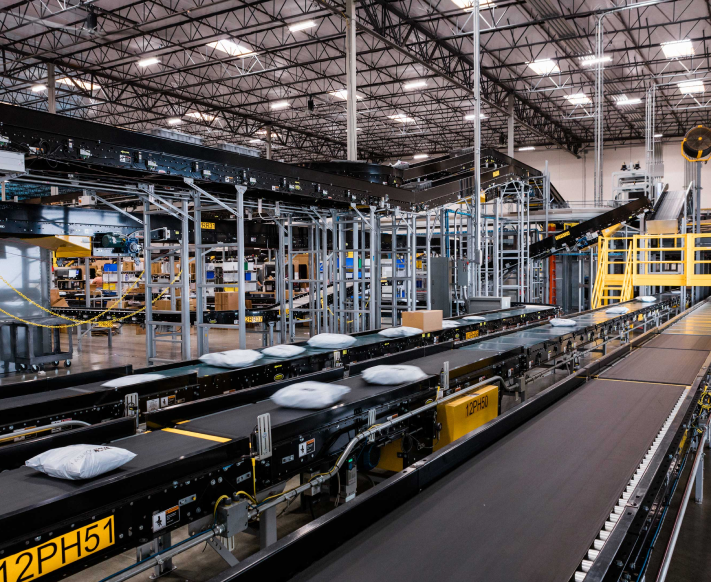
The machines that machine operators use to make repairs are a wide range of machines. These machines repair metal products like cars. They also create precision metal components and new alloys. Machinists can be exposed to toxic substances. A skilled machinist will be detail-oriented, have strong communication skills, and be able to read mechanical blueprints.
Machinists may work part-time as well as full-time. Many machinists start working straight out of high school. Some machinists go on to complete an apprenticeship before they can move up to a full time position. Others pursue associate degrees. A few machinists will even go on to study engineering or computer-aided designs (CAD).
Machinists often work in factories or specialty shops. These positions can be noisy, and they are exposed to potentially hazardous materials. However, these positions offer tremendous opportunities for problem solving. Machines used by machinists can be manual or automatic. Experienced machinists can rise to managerial or supervisory levels. With the retirement of baby boomers, the need for machinists grows. Machine shops are retooling for automation also increases job security.
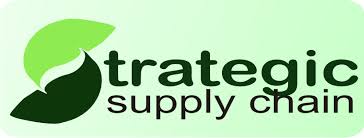
According to the employer, machinists may be assigned specific tasks, such as setting up and repairing machines or ensuring that their parts meet quality standards. They can also operate assembly lines, which are machines that are controlled by either a human or robot. Other responsibilities include programming and monitoring machines, as well as interpreting blueprints.
Machinists are skilled in working with a wide range of materials including steel, aluminum and brass as well as other metals. Although most machinists work on a machine that makes metal parts, they are sometimes required to work on other materials as well.
Generally, machinists have a high school diploma, although some employers may require an associate's degree. You can begin a four-year program if you're interested in becoming a Machinist. You may also have the opportunity to learn from a mentor in your work environment. Be sure to ask your mentor about other opportunities for training, such as apprenticeships or additional education.
No matter what company they work for, machinists have to collaborate with others. While they may work in a team or independently, machinists are expected to adhere to safety protocols. Proper safety equipment is required, including earplugs. Also, machinists are frequently exposed to fumes, chemicals, and other environmental hazards. Fortunately, machinists rarely have to work in a constant time zone.
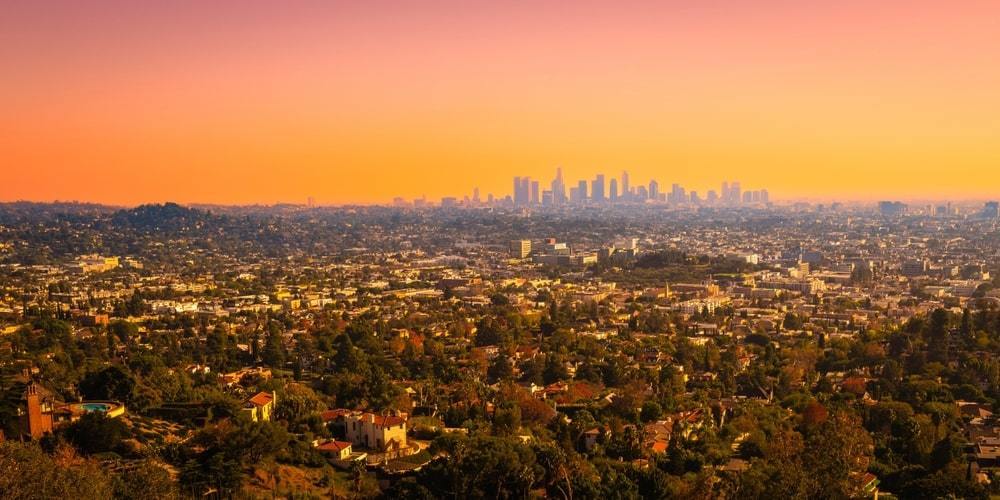
Machinists can also take college courses, or join trade unions. Union membership offers machinists greater benefits and more job security. Union members have access to health insurance and retirement plans. Many colleges offer 2-year programs for machining associates.
With a degree in machinist work, you can move up the corporate ladder. Machine operators will become more in demand as the demand for parts for cars increases. Between 2020-2030, there will be a 7% increase in employment. Machine operators will be in high demand for the next 20 years, thanks to increasing use of artificial intelligence, and retooling for automated manufacturing.
FAQ
What are the essential elements of running a logistics firm?
It takes a lot of skills and knowledge to run a successful logistics business. You must have good communication skills to interact effectively with your clients and suppliers. It is important to be able to analyse data and draw conclusions. You will need to be able handle pressure well and work in stressful situations. You must be creative and innovative to develop new ideas to improve efficiency. You must be a strong leader to motivate others and direct them to achieve organizational goals.
You should also be organized and efficient to meet tight deadlines.
Can some manufacturing processes be automated?
Yes! Automation has been around since ancient times. The wheel was invented by the Egyptians thousands of years ago. Today, robots assist in the assembly of lines.
Robotics is used in many manufacturing processes today. These include:
-
Automation line robots
-
Robot welding
-
Robot painting
-
Robotics inspection
-
Robots that create products
There are many other examples of how manufacturing could benefit from automation. For instance, 3D printing allows us make custom products and not have to wait for months or even weeks to get them made.
How does manufacturing avoid bottlenecks in production?
You can avoid bottlenecks in production by making sure that everything runs smoothly throughout the production cycle, from the moment you receive an order to the moment the product is shipped.
This includes planning to meet capacity requirements and quality control.
Continuous improvement techniques such Six Sigma can help you achieve this.
Six Sigma can be used to improve the quality and decrease waste in all areas of your company.
It's all about eliminating variation and creating consistency in work.
Statistics
- (2:04) MTO is a production technique wherein products are customized according to customer specifications, and production only starts after an order is received. (oracle.com)
- You can multiply the result by 100 to get the total percent of monthly overhead. (investopedia.com)
- According to the United Nations Industrial Development Organization (UNIDO), China is the top manufacturer worldwide by 2019 output, producing 28.7% of the total global manufacturing output, followed by the United States, Japan, Germany, and India.[52][53] (en.wikipedia.org)
- In 2021, an estimated 12.1 million Americans work in the manufacturing sector.6 (investopedia.com)
- Many factories witnessed a 30% increase in output due to the shift to electric motors. (en.wikipedia.org)
External Links
How To
How to Use 5S to Increase Productivity in Manufacturing
5S stands for "Sort", 'Set In Order", 'Standardize', & Separate>. Toyota Motor Corporation invented the 5S strategy in 1954. This methodology helps companies improve their work environment to increase efficiency.
This method has the basic goal of standardizing production processes to make them repeatable. This means that every day tasks such cleaning, sorting/storing, packing, and labeling can be performed. This knowledge allows workers to be more efficient in their work because they are aware of what to expect.
There are five steps that you need to follow in order to implement 5S. Each step involves a different action which leads to increased efficiency. For example, when you sort things, you make them easy to find later. You arrange items by placing them in an order. You then organize your inventory in groups. Make sure everything is correctly labeled when you label your containers.
This process requires employees to think critically about how they do their job. Employees must be able to see why they do what they do and find a way to achieve them without having to rely on their old methods. In order to use the 5S system effectively, they must be able to learn new skills.
In addition to increasing efficiency, the 5S method also improves morale and teamwork among employees. Once they start to notice improvements, they are motivated to keep working towards their goal of increasing efficiency.