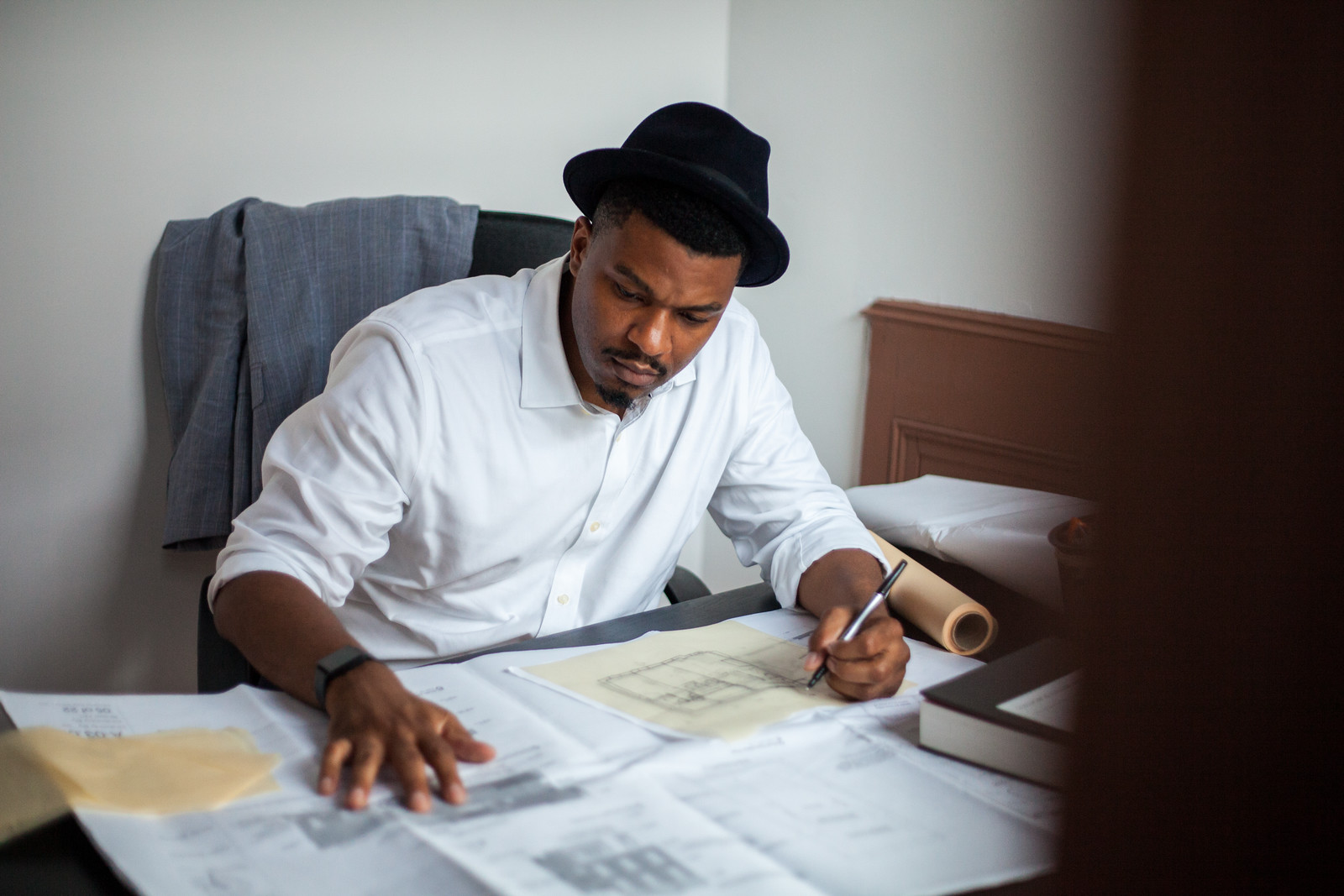
The supply chain is made up of a web of organizations, people and technologies that move materials from one supplier to another. The supply chain is made up of suppliers who provide raw materials, manufacturers, who create the parts and services needed to make a finished product and distributors, who distribute products to the consumers.
Companies are struggling with the economic downturn to build a stronger supply chain, despite a weaker demand environment and an increased level of competition. Stock accumulation makes it more difficult for businesses to forecast, plan, and execute their logistics.
It's vital to stay informed about the ever-changing supply chain by reading up on the latest news in supply chain management and logistic. Below are some of our favorite supply chain news sites to keep you up-to-date on the latest trends and issues.
Supply Chain Digest provides an excellent starting point. Each week it reviews hundreds news articles, reports, analyst opinions, and research studies and summarizes them in a format that is easy to understand for supply chains and logistics professionals. Alternatively, you can sign up for their weekly newsletter and get supply chain management and logistics news delivered to your inbox.
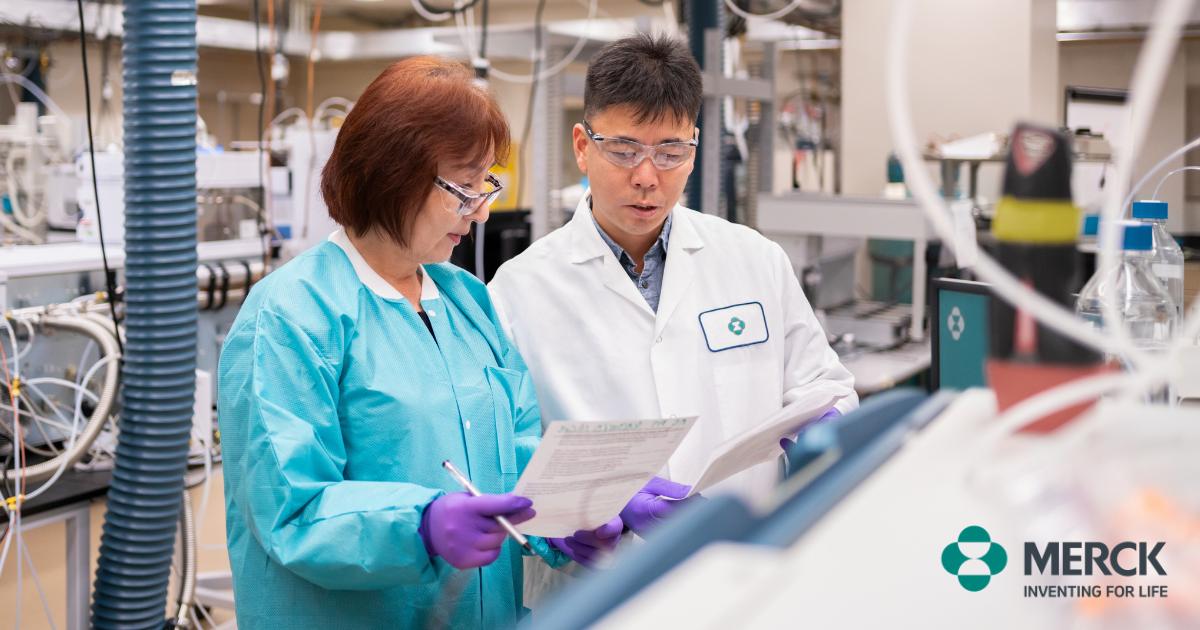
Another resource for supply chain and logistics news is Supply Chain Digital, which covers a variety of topics and sectors including digital procurement innovation, risk management, sustainable sourcing, indirect procurement and more. The site has a digital publication, blogs and podcasts, as well a database.
One Network - A revolutionary network approach to solving supply chain problems.
The One Network is an innovative network of organizations that helps businesses reduce their inventories and streamline their reverse logistic processes so they can manage obsolete products better. The network is featured in many influential supply chain magazines around the globe, and its technologies are used by major companies.
One Network is the best way to invest in your business's future.
To remain competitive in a world that is constantly changing, it is important to implement and adapt new technologies and methods. By using a network of technology providers, companies can increase their productivity and efficiency while decreasing their environmental impact.
Vyas believes that decoupling the supply chain, which involves encouraging companies to produce in multiple countries at once, will strengthen the system and help it be more resilient. This means shifting manufacturing from major hubs to smaller more diverse places.
In recent years, this strategy has become more popular due to changes in consumer tastes and an increased awareness of environmental issues. It also requires significant investments in infrastructure to support this move.
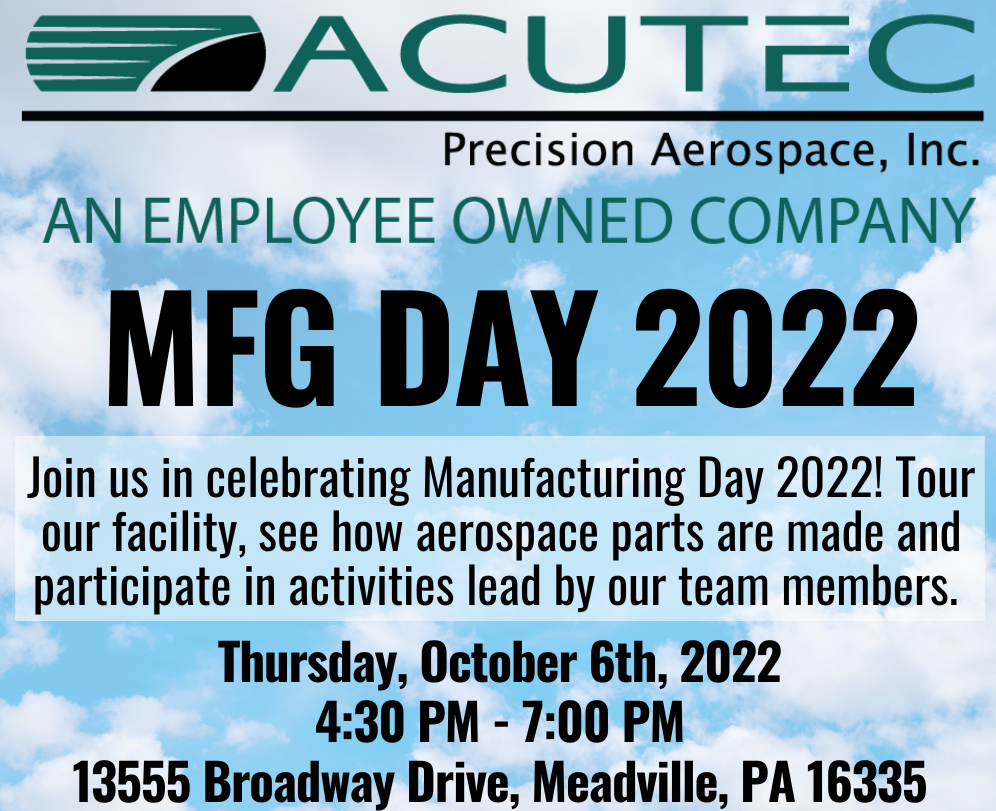
Businesses and consumers both benefit from a robust supply chain. The environment is also protected and costs are reduced for all involved.
Steps to strengthen the supply chains can help prepare businesses for the next major disruption. For example, the Covid-19 pandemic in 2021 that affected the supply of medical supplies, pharmaceuticals and other commodities. This can also ensure that businesses and consumers are able to quickly recover if disaster strikes.
FAQ
How can manufacturing avoid production bottlenecks
Production bottlenecks can be avoided by ensuring that processes are running smoothly during the entire production process, starting with the receipt of an order and ending when the product ships.
This includes planning for both capacity requirements and quality control measures.
Continuous improvement techniques such Six Sigma can help you achieve this.
Six Sigma Management System is a method to increase quality and reduce waste throughout your organization.
It seeks to eliminate variation and create consistency in your work.
Are there ways to automate parts of manufacturing?
Yes! Since ancient times, automation has been in existence. The Egyptians discovered the wheel thousands and years ago. Today, robots assist in the assembly of lines.
There are many applications for robotics in manufacturing today. These include:
-
Automated assembly line robots
-
Robot welding
-
Robot painting
-
Robotics inspection
-
Robots that create products
Manufacturing can also be automated in many other ways. 3D printing makes it possible to produce custom products in a matter of days or weeks.
Are there any Manufacturing Processes that we should know before we can learn about Logistics?
No. It doesn't matter if you don't know anything about manufacturing before you learn about logistics. Knowing about manufacturing processes will help you understand how logistics works.
What are manufacturing and logistics?
Manufacturing refers the process of producing goods from raw materials through machines and processes. Logistics is the management of all aspects of supply chain activities, including procurement, production planning, distribution, warehousing, inventory control, transportation, and customer service. Logistics and manufacturing are often referred to as one thing. It encompasses both the creation of products and their delivery to customers.
What are the 4 types of manufacturing?
Manufacturing refers the process of turning raw materials into useful products with machines and processes. It can involve many activities like designing, manufacturing, testing packaging, shipping, selling and servicing.
What are the products and services of logistics?
Logistics involves the transportation of goods from point A and point B.
They encompass all aspects transport, including packaging and loading, transporting, storage, unloading.
Logisticians ensure that the product is delivered to the correct place, at the right time, and under safe conditions. They provide information on demand forecasts as well stock levels, production schedules and availability of raw material.
They monitor shipments in transit, ensure quality standards, manage inventories, replenish orders, coordinate with suppliers and other vendors, and offer support services for sales, marketing, and customer service.
Statistics
- You can multiply the result by 100 to get the total percent of monthly overhead. (investopedia.com)
- In 2021, an estimated 12.1 million Americans work in the manufacturing sector.6 (investopedia.com)
- In the United States, for example, manufacturing makes up 15% of the economic output. (twi-global.com)
- Job #1 is delivering the ordered product according to specifications: color, size, brand, and quantity. (netsuite.com)
- It's estimated that 10.8% of the U.S. GDP in 2020 was contributed to manufacturing. (investopedia.com)
External Links
How To
How to Use lean manufacturing in the Production of Goods
Lean manufacturing refers to a method of managing that seeks to improve efficiency and decrease waste. It was developed in Japan during the 1970s and 1980s by Taiichi Ohno, who received the Toyota Production System (TPS) award from TPS founder Kanji Toyoda. Michael L. Watkins published the first book on lean manufacturing in 1990.
Lean manufacturing can be described as a set or principles that are used to improve quality, speed and cost of products or services. It emphasizes eliminating waste and defects throughout the value stream. The five-steps of Lean Manufacturing are just-in time (JIT), zero defect and total productive maintenance (TPM), as well as 5S. Lean manufacturing is about eliminating activities that do not add value, such as inspection, rework, and waiting.
Lean manufacturing not only improves product quality but also reduces costs. Companies can also achieve their goals faster by reducing employee turnover. Lean manufacturing is a great way to manage the entire value chain including customers, suppliers, distributors and retailers as well as employees. Lean manufacturing is widely used in many industries. For example, Toyota's philosophy underpins its success in automobiles, electronics, appliances, healthcare, chemical engineering, aerospace, paper, food, etc.
Five fundamental principles underlie lean manufacturing.
-
Define Value - Identify the value your business adds to society and what makes you different from competitors.
-
Reduce waste - Stop any activity that isn't adding value to the supply chains.
-
Create Flow - Make sure work runs smoothly without interruptions.
-
Standardize and simplify – Make processes as repeatable and consistent as possible.
-
Develop Relationships: Establish personal relationships both with internal and external stakeholders.
Although lean manufacturing isn't a new concept in business, it has gained popularity due to renewed interest in the economy after the 2008 global financial crisis. Many companies have adopted lean manufacturing methods to increase their marketability. Some economists even believe that lean manufacturing can be a key factor in economic recovery.
Lean manufacturing, which has many benefits, is now a standard practice in the automotive industry. These include higher customer satisfaction levels, reduced inventory levels as well as lower operating costs.
Any aspect of an enterprise can benefit from Lean manufacturing. It is especially useful for the production aspect of an organization, as it ensures that every step in the value chain is efficient and effective.
There are three types of lean manufacturing.
-
Just-in-Time Manufacturing (JIT): This type of lean manufacturing is commonly referred to as "pull systems." JIT is a process in which components can be assembled at the point they are needed, instead of being made ahead of time. This approach reduces lead time, increases availability and reduces inventory.
-
Zero Defects Manufacturing: ZDM ensures that no defective units leave the manufacturing plant. If a part is required to be repaired on the assembly line, it should not be scrapped. This also applies to finished products that need minor repairs before being shipped.
-
Continuous Improvement: Continuous Improvement aims to improve efficiency by continually identifying problems and making adjustments to eliminate or minimize waste. Continuous Improvement involves continuous improvement of processes.