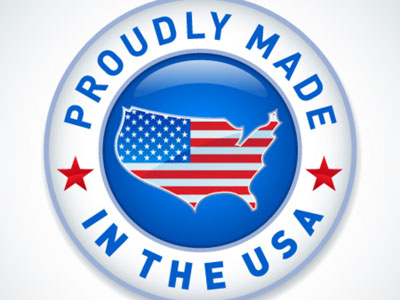
Supply Dynamics was established in Loveland (Ohio) in 2003. It offers technology solutions to manufacturers in highly distributed manufacturing environments. Supply Dynamics works in partnership with the Navy and the Defense Logistics Agency (DLA). It gives visibility and control over an organization's entire supply chain. It helps manufacturers plan production, and lowers the cost of raw materials. Supply Dynamics works with a number of industries including aerospace and defense manufacturing as well as transportation.
Dynamics 365 Supply Chain Management is a Microsoft Cloud-powered solution that enables organizations to improve operational efficiency, streamline production, and build strong supply chains. It provides unrivaled visibility into the entire supply chain, as well as flexibility and predictive analytics. Its modules ensure that products reach their customers on-time and provide functionality for the entire product lifecycle.
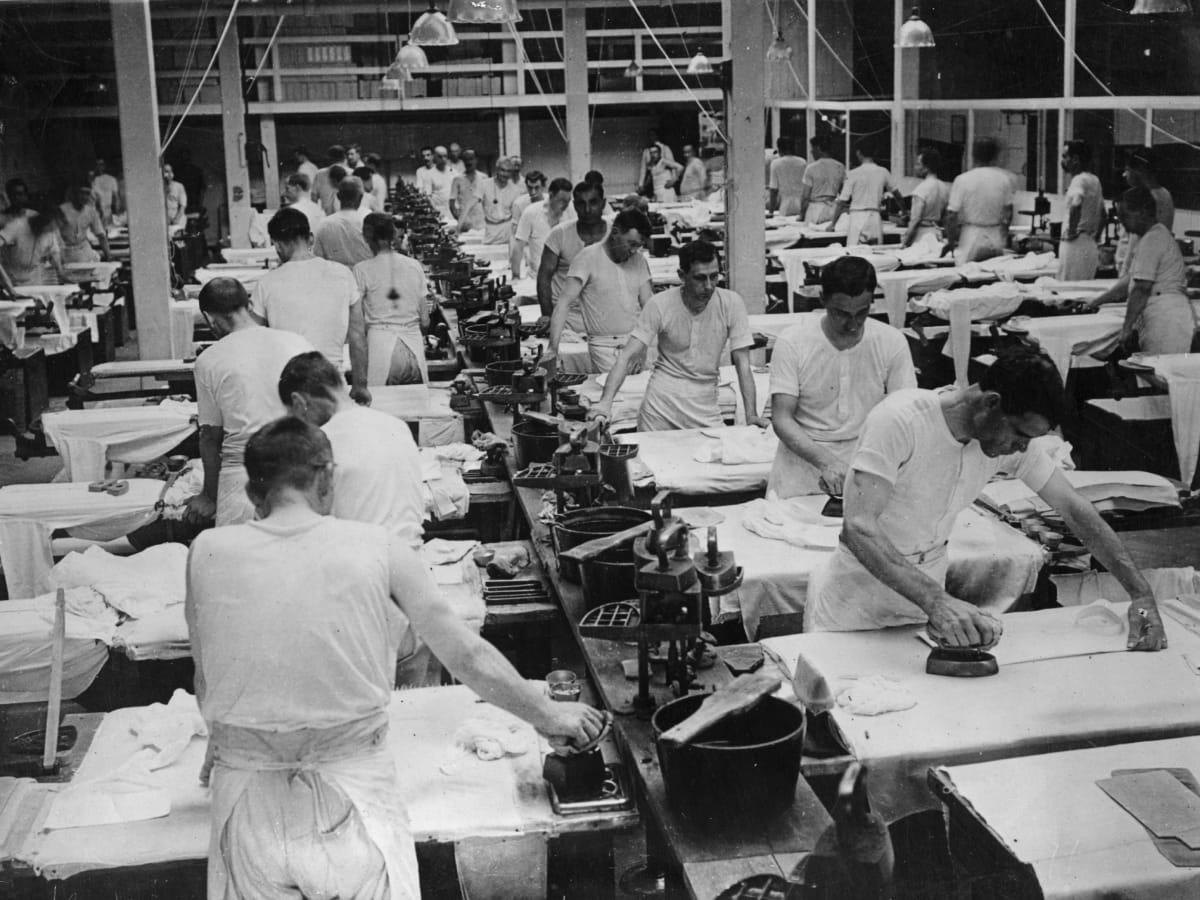
The Dynamics Supply Chain module allows users to create items for discrete or process manufacturing, submit RFQs and test product quality before submitting purchase orders. Gantt charts are also available to give transparency to all operations. Using the Visual Supply Schedule, users can see a forecast of inventory levels and anticipated supply and demand. They can also adjust schedules when supply chain issues arise. It also provides managers with the ability to track progress of job functions in various areas of a production floor.
Microsoft Dynamics 365 Supply Chain Management gives organizations a unified, predictive way to manage customer demands and ensure the right materials are available at the right moment. It can also help businesses anticipate customer needs and changes in their capacity. It can be used to integrate logistics, purchasing, production, and can even be used for multiple warehouses or sites. It supports vendor-specific pricing and multiple inventory costing methods. It can also be used for transportation management. The solution allows for inventory optimization and predictive analysis, as well as AI-features.
Dynamics 365 also includes self-service capabilities for suppliers. Suppliers can accept or reject purchase orders and raise PO invoices. They can also enter shipment information for existing POs. It supports many inventory costing options, including vendor-specific pricing as well as item-level and item group pricing. It has many inventory optimization options, including the ability create an inventory plan for an order.
Supply Dynamics offers unique benchmarking solutions for metals prices. With this technology, manufacturers are able to respond quicker to fluctuations in marketplace prices. They can also forecast and anticipate fluctuations in production cost. This technology allows manufacturers to lower the cost of raw materials and thus reduce waste. It also provides a blueprint for bill-of material data conversion.
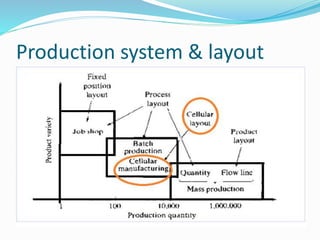
Its master plan feature automates creation of Production Orders based upon open Purchase Orders. It also features an optimization plugin that lets users forecast changes in customer needs. The AI capabilities of the program can help improve the flow in goods distribution. The Dynamics Supply Chain Management platform is certified by Microsoft, making it a great solution for companies seeking to build a strong supply chain.
FAQ
What is the importance of automation in manufacturing?
Not only is automation important for manufacturers, but it's also vital for service providers. Automation allows them to deliver services quicker and more efficiently. It also helps to reduce costs and improve productivity.
What is the job of a production plan?
Production planners ensure all aspects of the project are delivered within time and budget. They make sure that the product and services meet client expectations.
What does the term manufacturing industries mean?
Manufacturing Industries refers to businesses that manufacture products. These products are sold to consumers. These companies use various processes such as production, distribution, retailing, management, etc., to fulfill this purpose. They create goods from raw materials, using machines and various other equipment. This includes all types manufactured goods such as clothing, building materials, furniture, electronics, tools and machinery.
Statistics
- It's estimated that 10.8% of the U.S. GDP in 2020 was contributed to manufacturing. (investopedia.com)
- In 2021, an estimated 12.1 million Americans work in the manufacturing sector.6 (investopedia.com)
- Job #1 is delivering the ordered product according to specifications: color, size, brand, and quantity. (netsuite.com)
- [54][55] These are the top 50 countries by the total value of manufacturing output in US dollars for its noted year according to World Bank.[56] (en.wikipedia.org)
- According to a Statista study, U.S. businesses spent $1.63 trillion on logistics in 2019, moving goods from origin to end user through various supply chain network segments. (netsuite.com)
External Links
How To
How to use the Just In-Time Production Method
Just-intime (JIT), which is a method to minimize costs and maximize efficiency in business process, is one way. This is where you have the right resources at the right time. This means that your only pay for the resources you actually use. Frederick Taylor developed the concept while working as foreman in early 1900s. He noticed that workers were often paid overtime when they had to work late. He concluded that if workers were given enough time before they start work, productivity would increase.
The idea behind JIT is that you should plan ahead and have everything ready so you don't waste money. The entire project should be looked at from start to finish. You need to ensure you have enough resources to tackle any issues that might arise. If you expect problems to arise, you will be able to provide the necessary equipment and personnel to address them. This way, you won't end up paying extra money for things that weren't really necessary.
There are many types of JIT methods.
-
Demand-driven: This is a type of JIT where you order the parts/materials needed for your project regularly. This will enable you to keep track of how much material is left after you use it. It will also allow you to predict how long it takes to produce more.
-
Inventory-based : You can stock the materials you need in advance. This allows for you to anticipate how much you can sell.
-
Project-driven: This means that you have enough money to pay for your project. When you know how much you need, you'll purchase the appropriate amount of materials.
-
Resource-based JIT : This is probably the most popular type of JIT. Here you can allocate certain resources based purely on demand. You might assign more people to help with orders if there are many. If you don’t have many orders you will assign less people to the work.
-
Cost-based : This is similar in concept to resource-based. But here, you aren't concerned about how many people your company has but how much each individual costs.
-
Price-based: This approach is very similar to the cost-based method except that you don't look at individual workers costs but the total cost of the company.
-
Material-based: This is quite similar to cost-based, but instead of looking at the total cost of the company, you're concerned with how much raw materials you spend on average.
-
Time-based: Another variation of resource-based JIT. Instead of focusing on the cost of each employee, you will focus on the time it takes to complete a project.
-
Quality-based: This is yet another variation of resource-based JIT. Instead of thinking about the cost of each employee or the time it takes to produce something, you focus on how good your product quality.
-
Value-based JIT: This is the latest form of JIT. You don't worry about whether the products work or if they meet customer expectations. Instead, you are focused on adding value to the marketplace.
-
Stock-based. This method is inventory-based and focuses only on the actual production at any given point. It is used when production goals are met while inventory is kept to a minimum.
-
Just-intime planning (JIT), is a combination JIT/sales chain management. It's the process of scheduling delivery of components immediately after they are ordered. It reduces lead times and improves throughput.