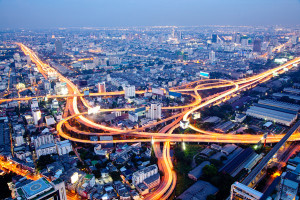
The salary for an engineer varies greatly depending on where you live. Washington is the most highly paid state in America, followed by New York City and California. It is also important to take into account the cost of living in a new place. As an example, a salary of $96,640 may not be sufficient to pay all your living expenses. You should consider your expenses before you apply to a new position.
Electrical engineers earn a median salary of $96,640
According to the U.S. Bureau of Labor Statistics (USBoLS), the average annual salary of an electric engineer is $96,640. This number may differ from one state to another. Salaries can also vary considerably within industry sectors. Retail trade is the most lucrative industry for electrical engineers, while education services is the lowest paying. However, there are some important factors to consider when determining the average salary for an electrical engineer. Below is a breakdown showing the different salary levels of electrical engineers.
The design and development electrical equipment is the responsibility of electrical engineers. They are also responsible for the design and development of electrical equipment. This statistic includes salaries for all types of electrical engineers, but does not include Computer Hardware Engineers, who make computers. According to Bureau of Labor Statistics the employment of these professionals should increase by 7 percentage points by 2026. Most electrical engineers will work in offices, though they may also travel to different types of sites for field work.
Biomedical engineers make a median income of $89 130
Biomedical engineers combine engineering knowledge with a knowledge of the human body in order to design and manufacture medical devices. Their experience in biomechanics and mechanics gives them the ability to understand how medical products interact and work with the body. This knowledge is useful for creating artificial organs and medical devices as well as diagnostic tools.
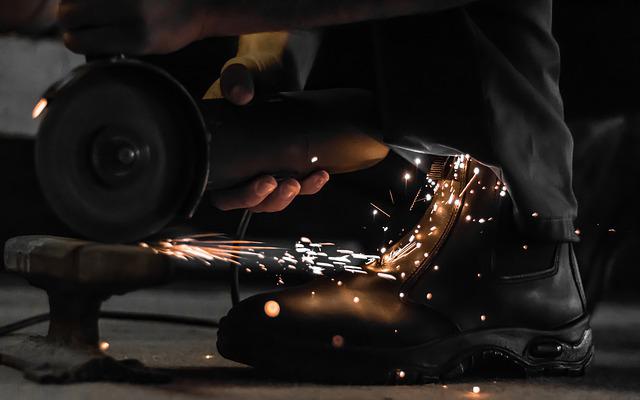
In addition to applying engineering principles to medical procedures, biomedical engineers are expected to have excellent communication skills. Their work requires them to present research findings, publish scientific papers, and collaborate with other health care professionals. Moreover, they must be proficient in advanced mathematics.
The median salary for mechanical engineers is $91,352.
Multiple factors influence the salary of a mechanical engineer. Salaries can differ by industry and location. According to the 2017 Salary Survey of ASME members, those living in the Northeast and the Southwest earn more than others. Those working in the Midwest earn the least.
The average salary for mechanical engineers ranges from $91,352 - $137,028. The average salary of mechanical engineers is $91,352, while the top six percent earn more than this. Those earning less than two years of experience earn an average of $72,400. But, those with more experience than two years can earn up to $150,000.
Agricultural engineers earn a median salary of $89,130
To solve power supply and environmental problems, agricultural engineers work in agricultural environments. They oversee construction and participate in design. This occupation requires advanced engineering knowledge and a good understanding of science, including biology and math. Their salaries are comparable to other related occupations in the United States. However, their salaries are usually lower than those of naval architects or locomotive engineers. The outlook for agricultural engineers looks positive. There will be 7.4% growth in employment between 2016 and 2026.
The average salary of agricultural engineers in the United States is $89130. The highest-paid individuals earn more than $110,000. The median agricultural engineer salary varies from one location to the next. Santa Clara and San Francisco are the most highly-paid cities for agricultural engineering professionals.
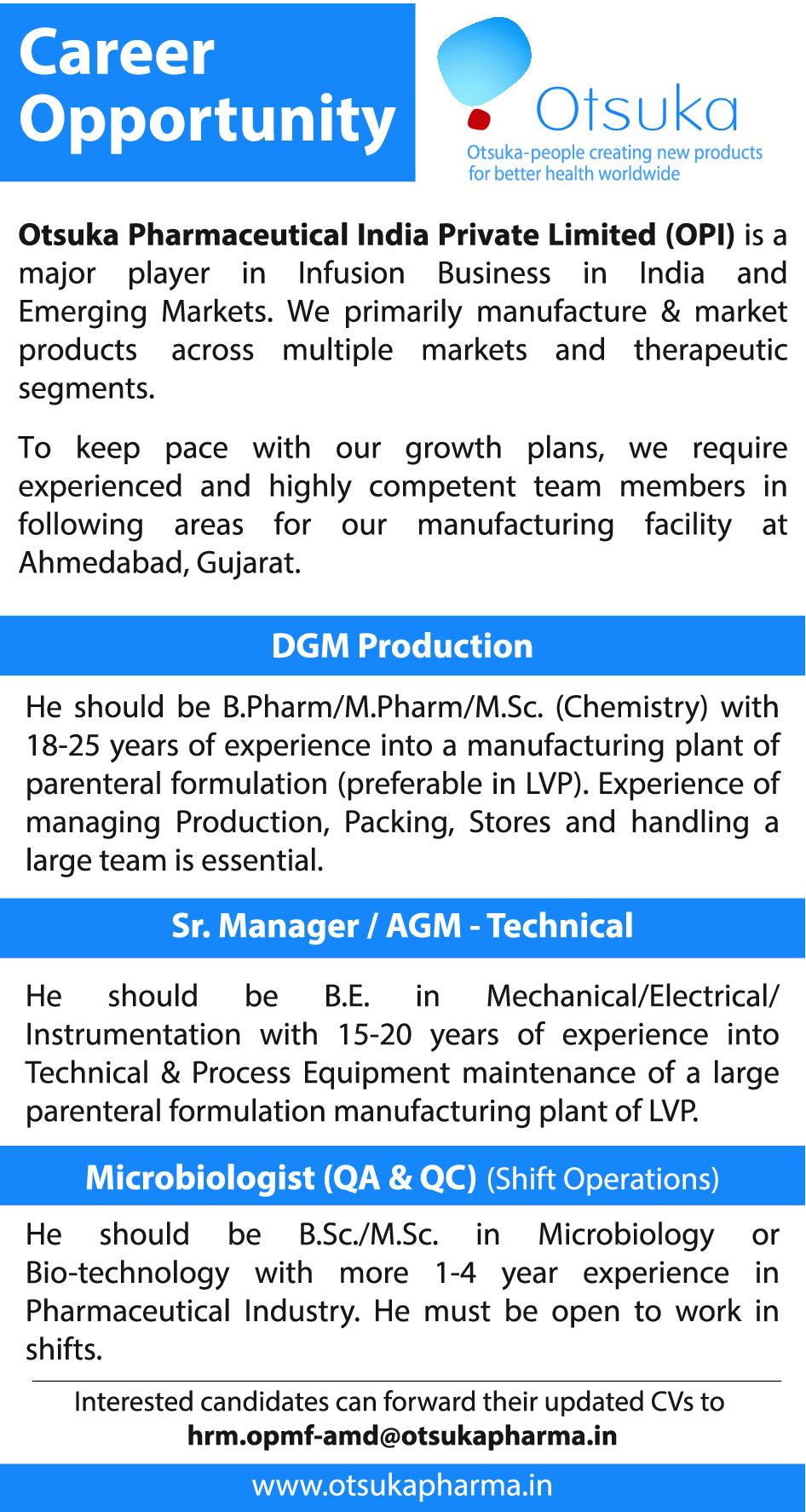
Environmental engineers earn a median salary of $87,620
The job of environmental engineers is to prevent the environment from being damaged by developing and implementing solutions that minimize any negative effects. They might work in different fields or collaborate with other engineers like urban planners and construction managers. Their training includes biology, chemistry, and data analysis and critical thought. They can also help organizations comply to environmental laws.
The environment engineers must be flexible, adaptable and able use new technologies and best-practices. They must have strong analytical skills as well as the ability to work together with their colleagues. They need to be problem solvers and positive.
FAQ
Is automation important for manufacturing?
Automating is not just important for manufacturers, but also for service providers. Automation allows them to deliver services quicker and more efficiently. It also helps to reduce costs and improve productivity.
What are the products and services of logistics?
Logistics is the process of moving goods from one point to another.
These include all aspects related to transport such as packaging, loading and transporting, storing, transporting, unloading and warehousing inventory management, customer service. Distribution, returns, recycling are some of the options.
Logisticians ensure that the right product reaches the right place at the right time and under safe conditions. They help companies manage their supply chain efficiency by providing information on demand forecasts, stock levels, production schedules, and availability of raw materials.
They monitor shipments in transit, ensure quality standards, manage inventories, replenish orders, coordinate with suppliers and other vendors, and offer support services for sales, marketing, and customer service.
What are the requirements to start a logistics business?
It takes a lot of skills and knowledge to run a successful logistics business. To communicate effectively with clients and suppliers, you must be able to communicate well. You should be able analyse data and draw inferences. You must be able and able to handle stress situations and work under pressure. To improve efficiency, you must be innovative and creative. Strong leadership qualities are essential to motivate your team and help them achieve their organizational goals.
You must be organized to meet tight deadlines.
Why automate your factory?
Modern warehouses have become more dependent on automation. E-commerce has brought increased demand for more efficient and quicker delivery times.
Warehouses must be able to quickly adapt to changing demands. In order to do this, they need to invest in technology. Automation warehouses can bring many benefits. Here are some of the reasons automation is worth your investment:
-
Increases throughput/productivity
-
Reduces errors
-
Increases accuracy
-
Safety increases
-
Eliminates bottlenecks
-
Companies can scale up more easily
-
It makes workers more efficient
-
Provides visibility into everything that happens in the warehouse
-
Enhances customer experience
-
Improves employee satisfaction
-
Reduces downtime and improves uptime
-
This ensures that quality products are delivered promptly
-
Removing human error
-
Helps ensure compliance with regulations
Statistics
- In the United States, for example, manufacturing makes up 15% of the economic output. (twi-global.com)
- You can multiply the result by 100 to get the total percent of monthly overhead. (investopedia.com)
- (2:04) MTO is a production technique wherein products are customized according to customer specifications, and production only starts after an order is received. (oracle.com)
- In 2021, an estimated 12.1 million Americans work in the manufacturing sector.6 (investopedia.com)
- Many factories witnessed a 30% increase in output due to the shift to electric motors. (en.wikipedia.org)
External Links
How To
How to Use Lean Manufacturing for the Production of Goods
Lean manufacturing is a management system that aims at increasing efficiency and reducing waste. It was created in Japan by Taiichi Ohno during the 1970s and 80s. He received the Toyota Production System award (TPS), from Kanji Toyoda, founder of TPS. Michael L. Watkins published the original book on lean manufacturing, "The Machine That Changed the World," in 1990.
Lean manufacturing is often defined as a set of principles used to improve the quality, speed, and cost of products and services. It is about eliminating defects and waste from all stages of the value stream. The five-steps of Lean Manufacturing are just-in time (JIT), zero defect and total productive maintenance (TPM), as well as 5S. Lean manufacturing eliminates non-value-added tasks like inspection, rework, waiting.
Lean manufacturing not only improves product quality but also reduces costs. Companies can also achieve their goals faster by reducing employee turnover. Lean manufacturing can be used to manage all aspects of the value chain. Customers, suppliers, distributors, retailers and employees are all included. Lean manufacturing can be found in many industries. Toyota's philosophy, for example, is what has enabled it to be successful in electronics, automobiles, medical devices, healthcare and chemical engineering as well as paper and food.
Lean manufacturing includes five basic principles:
-
Define value - Find out what your business contributes to society, and what makes it different from other competitors.
-
Reduce waste - Get rid of any activity that does not add value to the supply chain.
-
Create Flow - Ensure work moves smoothly through the process without interruption.
-
Standardize & Simplify - Make processes as consistent and repeatable as possible.
-
Build Relationships - Establish personal relationships with both internal and external stakeholders.
Although lean manufacturing isn't a new concept in business, it has gained popularity due to renewed interest in the economy after the 2008 global financial crisis. Many businesses have adopted lean production techniques to make them more competitive. Economists think that lean manufacturing is a crucial factor in economic recovery.
Lean manufacturing, which has many benefits, is now a standard practice in the automotive industry. These include improved customer satisfaction, reduced inventory levels, lower operating costs, increased productivity, and better overall safety.
Any aspect of an enterprise can benefit from Lean manufacturing. This is because it ensures efficiency and effectiveness in all stages of the value chain.
There are three main types in lean manufacturing
-
Just-in Time Manufacturing (JIT), also known as "pull system": This form of lean manufacturing is often referred to simply as "pull". JIT is a process in which components can be assembled at the point they are needed, instead of being made ahead of time. This approach aims to reduce lead times, increase the availability of parts, and reduce inventory.
-
Zero Defects Manufacturing (ZDM): ZDM focuses on ensuring that no defective units leave the manufacturing facility. Repairing a part that is damaged during assembly should be done, not scrapping. This is true even for finished products that only require minor repairs prior to shipping.
-
Continuous Improvement: Continuous Improvement aims to improve efficiency by continually identifying problems and making adjustments to eliminate or minimize waste. Continuous Improvement involves continuous improvement of processes.