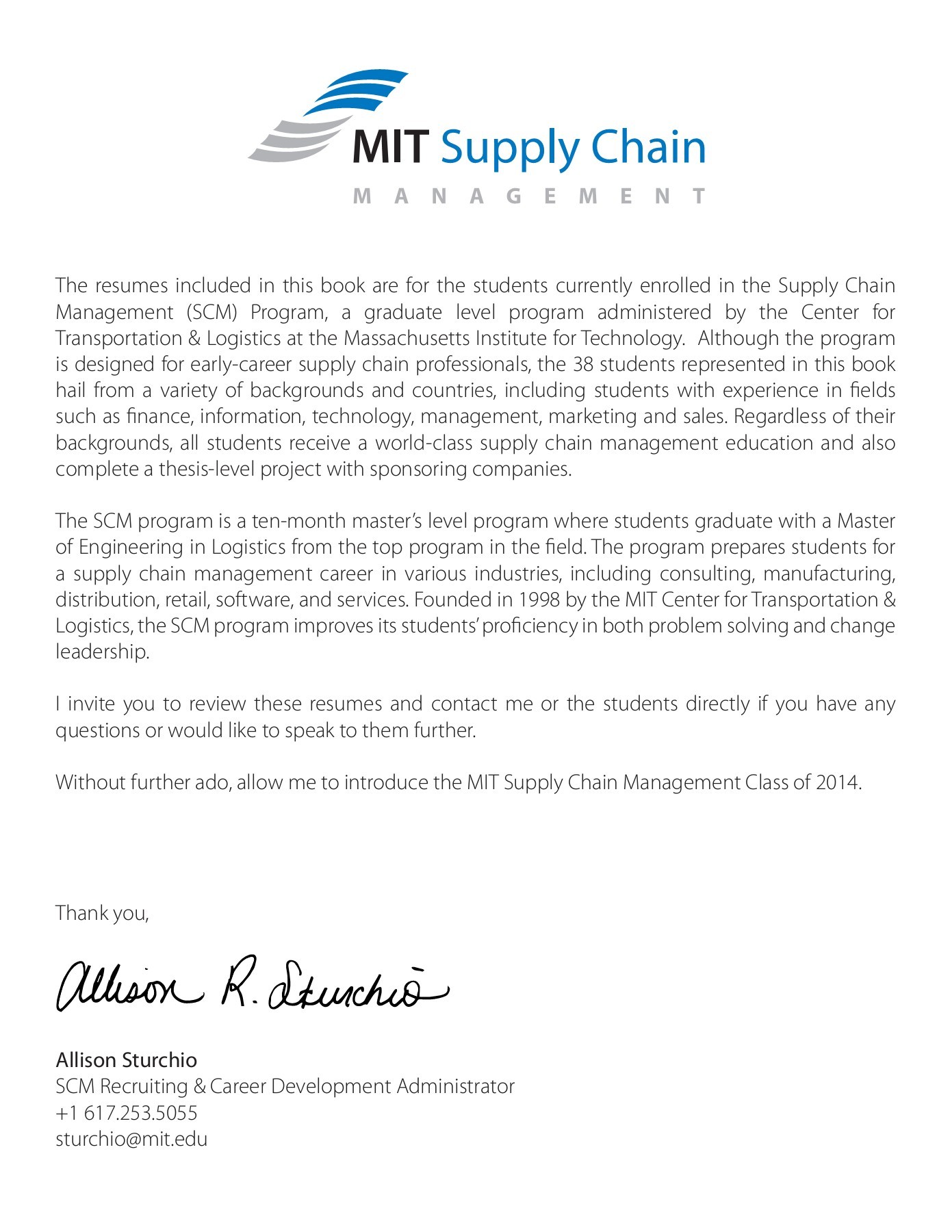
Manufacturing engineers are responsible to convert raw materials into updated and new products, create efficient systems that integrate production and supervise people involved in the product manufacturing. This career is rewarding and can provide a great work-life balance.
The average manufacturing engineer salary in the US is $77,500. This figure is based on data from 655 TurboTax users who reported their occupation as manufacturing engineer and includes taxable wages, tips, bonuses and more.
What is Manufacturing Engineering Salary?
The Manufacturing Engineering Salary ranges between $28,500 and $178,500, depending on your education, skills and experience, as well as the employer you work for. Those with more experience in the manufacturing industry earn more, whereas those starting out tend to earn less.
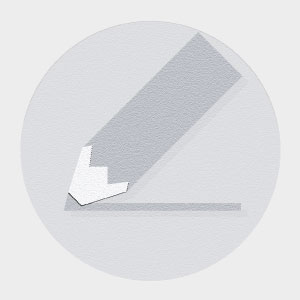
Salary of Entry-Level Manufacturing Engineer: The average salary for a manufacturing engineer at the entry-level is $52,000. This can vary greatly from one state to another, so you should always check to see what the average wage is before applying for any job.
What qualifications are required to be a manufacturing engineers?
Generally, you'll need at least a bachelor's degree in a relevant subject. You can choose from a wide range of engineering specialties as well as a general field such s computer science or electric engineering. You will need a graduate level degree if your goal is to work in research or to progress within the field.
What is the average job of a manufacturing engineer?
Most engineers create and develop systems which improve productivity. They are the experts who create the processes that turn raw materials into a finished product, focusing on eliminating wastefulness. These engineers have strong problem-solving ability, allowing them to solve problems quickly in the development of new products and upgrading of existing ones.
What do manufacturing engineers do in their day-to-day duties?
Manufacturing engineers are responsible for keeping projects on time and within budget. They also ensure that production is efficient, and maintain high standards. They must be able to communicate effectively with design engineers, technicians and management. It is important that they understand how their choices affect production costs, timelines, etc. and how to manage this in a way which benefits the whole project team.
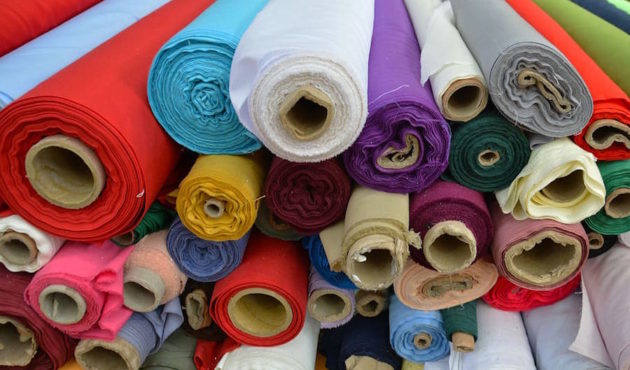
What are the requirements to become a manufacturing or industrial engineer?
Almost any company that has in-house manufacturing needs a manufacturing engineer. They can be large multinational corporations or small companies.
What are popular jobs in manufacturing engineering?
There are a variety of industries that employ manufacturing engineers, including aerospace, defense, software and hardware development, robotics and assembly line automation. The manufacturing engineer may work in a laboratory, office or factory.
What is a typical manufacturing engineer's salary?
The US manufacturing engineer salary ranges between $57,839 and $96,809 annually. This figure was derived from data collected by 655 TurboTax customers who identified themselves as manufacturing engineers. The figures include taxable earnings, tips, bonuses, and other items.
FAQ
What skills are required to be a production manager?
You must be flexible and organized to become a productive production planner. Also, you must be able and willing to communicate with clients and coworkers.
How can we improve manufacturing efficiency?
The first step is to determine the key factors that impact production time. We then need to figure out how to improve these variables. If you don't know where to start, then think about which factor(s) have the biggest impact on production time. Once you have identified the factors, then try to find solutions.
What is the role of a manager in manufacturing?
Manufacturing managers must ensure that manufacturing processes are efficient, effective, and cost-effective. They should be alert for any potential problems in the company and react accordingly.
They should also be able and comfortable communicating with other departments like sales and marketing.
They must also keep up-to-date with the latest trends in their field and be able use this information to improve productivity and efficiency.
How can overproduction in manufacturing be reduced?
The key to reducing overproduction lies in developing better ways to manage inventory. This would reduce the amount of time spent on unnecessary activities such as purchasing, storing, and maintaining excess stock. This could help us free up our time for other productive tasks.
You can do this by adopting a Kanban method. A Kanban board is a visual display used to track work in progress. Work items are moved through various states to reach their destination in a Kanban system. Each state represents a different priority level.
When work is completed, it can be transferred to the next stage. If a task is still in its beginning stages, it will continue to be so until it reaches the end.
This allows you to keep work moving along while making sure that no work gets neglected. Managers can monitor the work being done by Kanban boards to see what is happening at any given time. This allows them to adjust their workflows based on real-time information.
Another way to control inventory levels is to implement lean manufacturing. Lean manufacturing seeks to eliminate waste from every step of the production cycle. Waste includes anything that does not add value to the product. Some common types of waste include:
-
Overproduction
-
Inventory
-
Unnecessary packaging
-
Materials in excess
These ideas can help manufacturers improve efficiency and reduce costs.
What are the jobs in logistics?
There are many kinds of jobs available within logistics. Some of them are:
-
Warehouse workers: They load and unload trucks, pallets, and other cargo.
-
Transportation drivers – These drivers drive trucks and wagons to transport goods and pick up the goods.
-
Freight handlers: They sort and package freight in warehouses.
-
Inventory managers - They oversee the inventory of goods in warehouses.
-
Sales representatives: They sell products to customers.
-
Logistics coordinators - They plan and organize logistics operations.
-
Purchasing agents: They are responsible for purchasing goods and services to support company operations.
-
Customer service agents - They answer phone calls and respond to emails.
-
Shipping clerks - They process shipping orders and issue bills.
-
Order fillers - These people fill orders based on what has been ordered.
-
Quality control inspectors - They check incoming and outgoing products for defects.
-
Others - There is a variety of other jobs in logistics. These include transportation supervisors and cargo specialists.
Statistics
- According to a Statista study, U.S. businesses spent $1.63 trillion on logistics in 2019, moving goods from origin to end user through various supply chain network segments. (netsuite.com)
- It's estimated that 10.8% of the U.S. GDP in 2020 was contributed to manufacturing. (investopedia.com)
- According to the United Nations Industrial Development Organization (UNIDO), China is the top manufacturer worldwide by 2019 output, producing 28.7% of the total global manufacturing output, followed by the United States, Japan, Germany, and India.[52][53] (en.wikipedia.org)
- Many factories witnessed a 30% increase in output due to the shift to electric motors. (en.wikipedia.org)
- (2:04) MTO is a production technique wherein products are customized according to customer specifications, and production only starts after an order is received. (oracle.com)
External Links
How To
How to use 5S to increase Productivity in Manufacturing
5S stands for "Sort", 'Set In Order", 'Standardize', & Separate>. The 5S methodology was developed at Toyota Motor Corporation in 1954. It helps companies achieve higher levels of efficiency by improving their work environment.
The basic idea behind this method is to standardize production processes, so they become repeatable, measurable, and predictable. Cleaning, sorting and packing are all done daily. Because workers know what they can expect, this helps them perform their jobs more efficiently.
Five steps are required to implement 5S: Sort, Set In Order, Standardize. Separate. Each step is a different action that leads to greater efficiency. You can make it easy for people to find things later by sorting them. When you set items in an order, you put items together. You then organize your inventory in groups. Labeling your containers will ensure that everything is correctly labeled.
This requires employees to critically evaluate how they work. Employees need to understand the reasons they do certain jobs and determine if there is a better way. To implement the 5S system, employees must acquire new skills and techniques.
In addition to increasing efficiency, the 5S method also improves morale and teamwork among employees. They will feel motivated to strive for higher levels of efficiency once they start to see results.