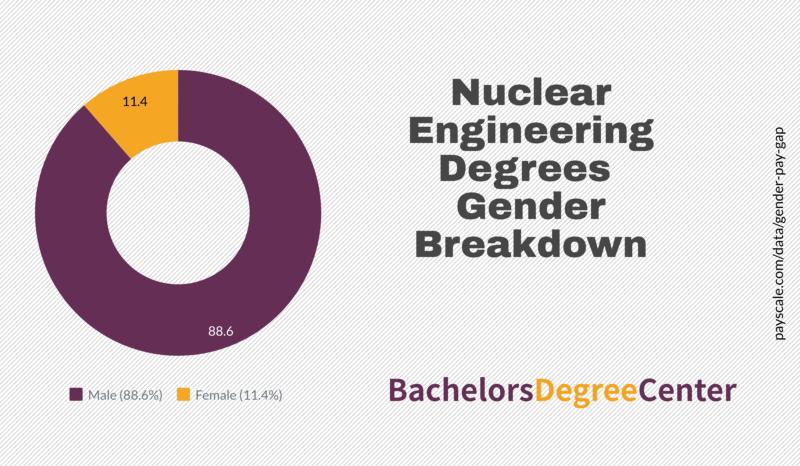
Industrial management is an engineering field where different engineering processes are integrated in order to create a management system. A industrial manager is responsible for integrating these engineering processes into one integrated management system. Here are some details about the job. Here are the requirements and benefits of becoming an industrial manager. This career is for you if your qualifications are up-to-date and you're looking for a rewarding and challenging job. Continue reading for more information.
Job description
An industrial manager supervises the production processes and products. This job will cover many aspects of production, but it will also include how to source raw materials or implement equipment. Because computers are increasingly playing a central role in the coordination and management of many departments, suppliers, or clients, industrial production managers must be computer-literate. Additionally, industrial production managers need to be proficient in current production technologies and management methods. Many managers take part in professional organizations, attend tradeshows and conferences in the industry, and enroll in courses to earn certification.
Industrial managers coordinate all activities within a company, in addition to supervising production processes. They make sure production lines run smoothly and meet customers' time and quality requirements. In addition, they oversee staffing levels and change production levels as necessary to minimize inventory. They may also oversee quality control programs and coordinate communication with suppliers and other departments. A majority of this role involves managing people, which includes identifying, training, and motivating employees.
Education is necessary
A bachelor's degree is not required to be an industrial manager. However, some employers prefer to hire people with experience in these fields. A computer-literate industrial manager is also required. Computers are becoming increasingly essential in the manufacturing process. They help coordinate production between departments, suppliers, clients, and other parties. In order to succeed in this field, individuals interested should have the appropriate education and experience.
Many industrial production managers started their careers as production workers before moving up to the first-line supervisory position. To advance to an industrial manager position, most professionals must earn a college degree in business management. Some workers can earn this education on their own, while others may opt to attend classes sponsored or paid for by their companies. However, most managers are expected to have two to five years of relevant experience before becoming a manager.
Potential earning
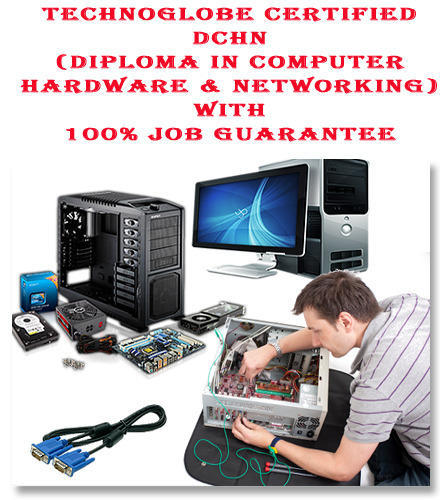
In manufacturing plants, industrial managers oversee the smooth running of the entire operation. They are responsible for determining how best to utilize equipment and employees, as well as making strategic decisions. Their responsibilities include hiring, evaluating, and setting production times, and making sure safety procedures are adhered to. They supervise the day-today activities of a workforce and monitor the entire production process to ensure it operates efficiently and at peak efficiency.
The experience and employer of an industrial production manager will determine the potential earnings. While it's difficult to predict the future earnings of industrial managers, the average salary in May 2016 was $103,380, with the highest paid industrial production managers earning $172,150 annually. Higher earnings may also be available for industrial production managers who have completed advanced training or certification. According to the U.S. Bureau of Labor Statistics (USBoLS), industrial production managers who hold a bachelor's or higher degree in manufacturing management may earn more.
Work environment
An industrial production manager splits his or her time between a production floor and an office. Often, the offices are located in the same building. When working in a production area, industrial production managers must adhere to established safety and health practices. They spend a lot of time meeting with their subordinates and analysing production data. These managers may also write reports. An industrial production manager's work environment can be dynamic.
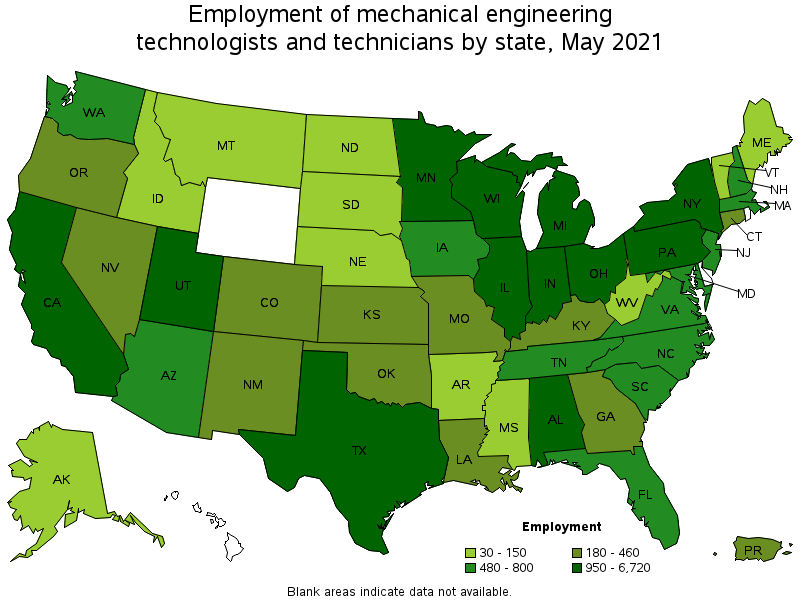
The industrial production manager is an important part of a company's management structure. They have to coordinate the work of many workers and increase productivity. Increasing productivity and ensuring safety are some of the primary responsibilities of an industrial production manager. Due to corporate restructuring, many levels have been eliminated and support staff reduced. Production managers are now able to handle more of the work load. This can be a significant challenge for any manager, and can make it difficult to do the job as a production manager.
FAQ
What is production planning?
Production Planning involves developing a plan for all aspects of the production, including scheduling, budgeting, casting, crew, location, equipment, props, etc. This document is designed to make sure everything is ready for when you're ready to shoot. This document should also include information on how to get the best result on set. This includes shooting schedules, locations, cast lists, crew details, and equipment requirements.
It is important to first outline the type of film you would like to make. You may have already decided where you would like to shoot, or maybe there are specific locations or sets that you want to use. Once you have determined your scenes and locations, it is time to start figuring out the elements that you will need for each scene. If you decide you need a car and don't know what model to choose, this could be an example. In this case, you could start looking up cars online to find out what models are available and then narrow your choices by choosing between different makes and models.
After you have chosen the right car, you will be able to begin thinking about accessories. What about additional seating? Or perhaps you need someone walking around the back of the car? Perhaps you would like to change the interior colour from black to white. These questions will help you determine the exact look and feel of your car. Another thing you can do is think about what type of shots are desired. You will be filming close-ups and wide angles. Maybe the engine or steering wheel is what you are looking to film. These details will help identify the exact car you wish to film.
Once you have all the information, you are ready to create a plan. You can use a schedule to determine when and where you need it to be shot. You will need to know when you have to be there, what time you have to leave and when your return home. Everyone will know what they need and when. Hire extra staff by booking them ahead of time. You don't want to hire someone who won't show up because he didn't know.
When creating your schedule, you will also need to consider the number of days you need to film. Some projects only take one or two days, while others may last weeks. When you are creating your schedule, you should always keep in mind whether you need more than one shot per day or not. Shooting multiple takes over the same location will increase costs and take longer to complete. If you aren't sure whether you need multiple shots, it is best to take fewer photos than you would like.
Budgeting is another crucial aspect of production plan. As it will allow you and your team to work within your financial means, setting a realistic budget is crucial. Remember that you can always reduce the budget later on if you run into unforeseen problems. However, it is important not to overestimate the amount that you will spend. You'll end up with less money after paying for other things if the cost is underestimated.
Production planning is a detailed process. But, once you understand the workings of everything, it becomes easier for future projects to be planned.
What type of jobs is there in logistics
Logistics can offer many different jobs. Some examples are:
-
Warehouse workers – They load, unload and transport pallets and trucks.
-
Transport drivers - These are people who drive trucks and trailers to transport goods or perform pick-ups.
-
Freight handlers: They sort and package freight in warehouses.
-
Inventory managers - These are responsible for overseeing the stock of goods in warehouses.
-
Sales reps are people who sell products to customers.
-
Logistics coordinators - They plan and organize logistics operations.
-
Purchasing agents – They buy goods or services necessary to run a company.
-
Customer service representatives - Answer calls and email from customers.
-
Ship clerks - They issue bills and process shipping orders.
-
Order fillers - They fill orders based on what is ordered and shipped.
-
Quality control inspectors: They inspect outgoing and incoming products for any defects.
-
Others – There are many other types available in logistics. They include transport supervisors, cargo specialists and others.
What is the responsibility of a logistics manager?
Logistics managers make sure all goods are delivered on schedule and without damage. This is accomplished by using the experience and knowledge gained from working with company products. He/she also needs to ensure adequate stock to meet demand.
Statistics
- In 2021, an estimated 12.1 million Americans work in the manufacturing sector.6 (investopedia.com)
- You can multiply the result by 100 to get the total percent of monthly overhead. (investopedia.com)
- It's estimated that 10.8% of the U.S. GDP in 2020 was contributed to manufacturing. (investopedia.com)
- [54][55] These are the top 50 countries by the total value of manufacturing output in US dollars for its noted year according to World Bank.[56] (en.wikipedia.org)
- (2:04) MTO is a production technique wherein products are customized according to customer specifications, and production only starts after an order is received. (oracle.com)
External Links
How To
How to Use 5S to Increase Productivity in Manufacturing
5S stands to stand for "Sort", “Set In Order", “Standardize", and "Store". The 5S methodology was developed at Toyota Motor Corporation in 1954. This methodology helps companies improve their work environment to increase efficiency.
This approach aims to standardize production procedures, making them predictable, repeatable, and easily measurable. It means tasks like cleaning, sorting or packing, labeling, and storing are done every day. Workers can be more productive by knowing what to expect.
Implementing 5S requires five steps. These are Sort, Set In Order, Standardize. Separate. And Store. Each step involves a different action which leads to increased efficiency. By sorting, for example, you make it easy to find the items later. When you set items in an order, you put items together. Next, organize your inventory into categories and store them in containers that are easily accessible. You can also label your containers to ensure everything is properly labeled.
This requires employees to critically evaluate how they work. Employees need to be able understand their motivations and discover alternative ways to do them. To be successful in the 5S system, employees will need to acquire new skills and techniques.
The 5S method not only increases efficiency but also boosts morale and teamwork. They feel more motivated to work towards achieving greater efficiency as they see the results.