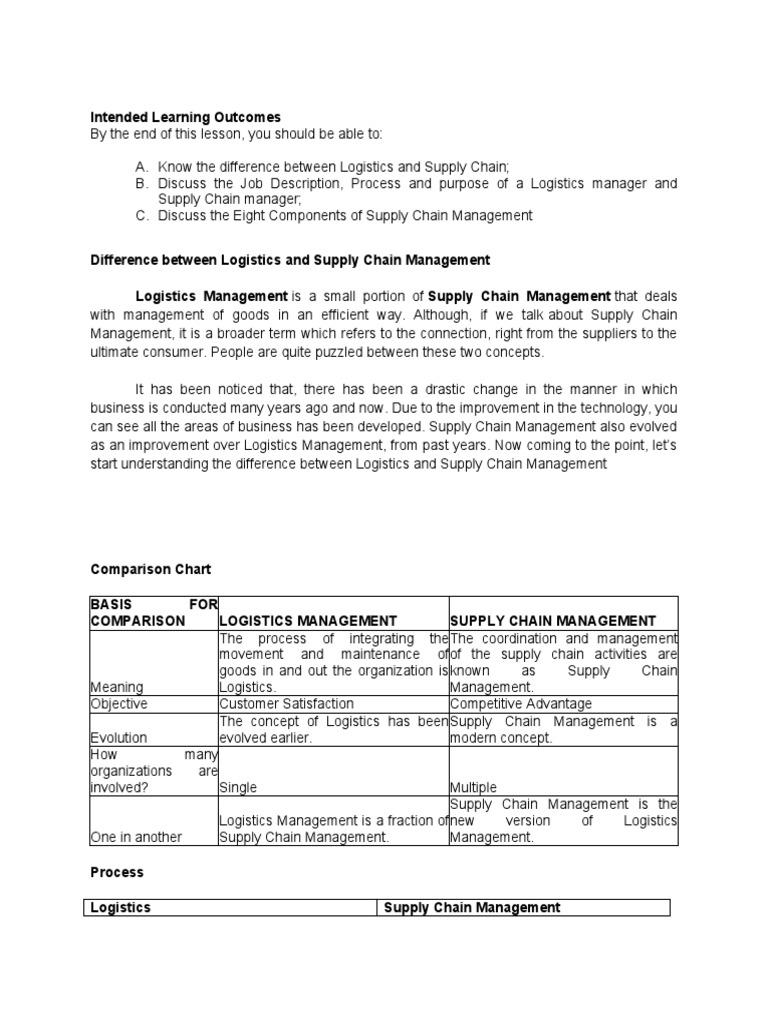
Increasingly, consumers are expecting products to be a holistic experience. In order to meet that expectation, companies must have a supply chain that can deliver fast, customized, and personalized products. The modern supply system is more flexible to adapt and responsive than the traditional one. Companies can track disruptions and make better decision to ensure that deliveries are timely and reliable by using data analytics.
Accenture Strategy, a service offered by Accenture, assists companies in transforming their supply chain capabilities. This includes creating innovative solutions and accelerating the skills of the supply-chain workforce. It also aligns operating models with business strategy. It includes a focus upon sustainability and governance. Ultimately, the company aims to build long-term value for its clients.
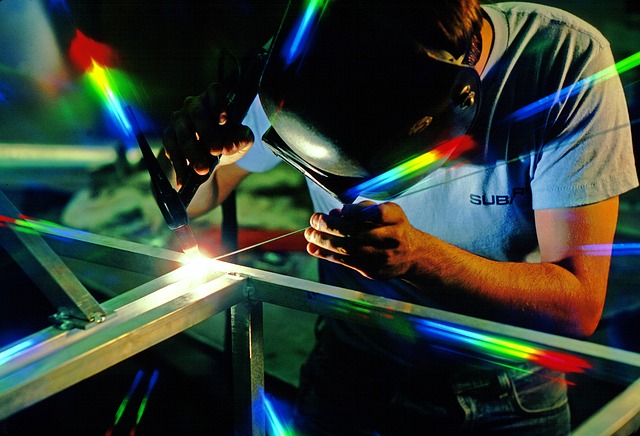
Accenture focuses on improving supply chains on a global scale. Accenture's digital services are combined with industry expertise. They strive to do this by combining both digital and industry expertise. Combined with a global supply network, they can help companies build intelligent supply chains that drive profitable growth and positive social change. Accenture's supply chain experts work in a variety of industries, including energy and consumer packaged goods. Accenture's supply chain experts can help clients design, operate and transform their supply chains using a variety of applications and services.
Accenture works with clients to develop sustainability initiatives. They have a global supplier inclusion program that aims to help more companies make good business decisions while advancing a sustainable, inclusive, and ethical supply chain ecosystem. Recently, the company released a report with advice on creating a sustainable supply network, leveraging data and leveraging governance. The report also includes supplier scoring data and suggestions for creating resilient supply networks.
Accenture's supply chain analytics team works with clients to improve their sustainability practices and to help them become more responsible. They are able identify clients' strengths, weaknesses and opportunities for improvement. Blue Yonder technology is used to assist companies in optimizing their supply chains.
Accenture has significant purchasing and supply chain capabilities. Accenture created an enterprise business system in 2007 which allows companies to more effectively manage and implement their supply chain. Companies could only see a handful suppliers and knew little about the supply chain. This made it difficult for companies respond to market demand. The company introduced myConcerto, an enterprise-wide solution that provides companies with comprehensive information on how to monitor their supply chain.
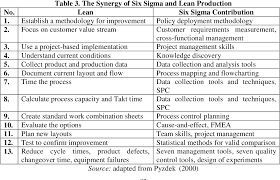
Accenture has a team of supply chain experts who work with Defense Logistics Agency (DLA). This helps them to improve efficiency and reliability in the military supply chain. The DLA oversees 520,000 shipments annually, and averages over 8,000 contracts per hour. Accenture collaborates with the DLA in order to increase product availability and decrease delivery times. The company also works closely with Coles Supermarkets on improving the customer experience. They also develop Splunk technology-based control tower monitoring solutions.
FAQ
How can we improve manufacturing efficiency?
The first step is to identify the most important factors affecting production time. Then we need to find ways to improve these factors. If you don’t know where to begin, consider which factors have the largest impact on production times. Once you've identified them, try to find solutions for each of those factors.
Is there anything we should know about Manufacturing Processes prior to learning about Logistics.
No. It doesn't matter if you don't know anything about manufacturing before you learn about logistics. But, being familiar with manufacturing processes will give you a better understanding about how logistics works.
What is it like to manage a logistics company?
A successful logistics business requires a lot more than just knowledge. For clients and suppliers to be successful, you need to have excellent communication skills. You need to understand how to analyze data and draw conclusions from it. You need to be able work under pressure and manage stressful situations. To increase efficiency and creativity, you need to be creative. To motivate and guide your team towards reaching organizational goals, you must have strong leadership skills.
It is important to be organized and efficient in order to meet tight deadlines.
What are the goods of logistics?
Logistics refers to the movement of goods from one place to another.
They include all aspects of transport, including packaging, loading, transporting, unloading, storing, warehousing, inventory management, customer service, distribution, returns, and recycling.
Logisticians ensure the product reaches its destination in the most efficient manner. They help companies manage their supply chain efficiency by providing information on demand forecasts, stock levels, production schedules, and availability of raw materials.
They monitor shipments in transit, ensure quality standards, manage inventories, replenish orders, coordinate with suppliers and other vendors, and offer support services for sales, marketing, and customer service.
What are the 4 types of manufacturing?
Manufacturing is the process that transforms raw materials into useful products. It includes many different activities like designing, building and testing, packaging, shipping and selling, as well as servicing.
How can I find out more about manufacturing?
Experience is the best way for you to learn about manufacturing. You can read books, or watch instructional videos if you don't have the opportunity to do so.
What are the 7 R's of logistics?
The 7R's of Logistics is an acronym for the seven basic principles of logistics management. It was published in 2004 by the International Association of Business Logisticians as part of their "Seven Principles of Logistics Management" series.
The acronym is made up of the following letters:
-
Responsible - ensure that actions are in compliance with legal requirements and do not cause harm to others.
-
Reliable - have confidence in the ability to deliver on commitments made.
-
Reasonable - use resources efficiently and don't waste them.
-
Realistic – consider all aspects of operations, from cost-effectiveness to environmental impact.
-
Respectful – Treat others fairly and equitably.
-
You are resourceful and look for ways to save money while increasing productivity.
-
Recognizable - provide customers with value-added services.
Statistics
- [54][55] These are the top 50 countries by the total value of manufacturing output in US dollars for its noted year according to World Bank.[56] (en.wikipedia.org)
- Job #1 is delivering the ordered product according to specifications: color, size, brand, and quantity. (netsuite.com)
- According to a Statista study, U.S. businesses spent $1.63 trillion on logistics in 2019, moving goods from origin to end user through various supply chain network segments. (netsuite.com)
- It's estimated that 10.8% of the U.S. GDP in 2020 was contributed to manufacturing. (investopedia.com)
- In 2021, an estimated 12.1 million Americans work in the manufacturing sector.6 (investopedia.com)
External Links
How To
How to use 5S in Manufacturing to Increase Productivity
5S stands for "Sort", 'Set In Order", 'Standardize', & Separate>. Toyota Motor Corporation created the 5S methodology in 1954. This methodology helps companies improve their work environment to increase efficiency.
This approach aims to standardize production procedures, making them predictable, repeatable, and easily measurable. Cleaning, sorting and packing are all done daily. Workers can be more productive by knowing what to expect.
Implementing 5S involves five steps: Sort, Set in Order, Standardize Separate, Store, and Each step involves a different action which leads to increased efficiency. By sorting, for example, you make it easy to find the items later. When you set items in an order, you put items together. After you have divided your inventory into groups you can store them in easy-to-reach containers. Make sure everything is correctly labeled when you label your containers.
Employees will need to be more critical about their work. Employees need to be able understand their motivations and discover alternative ways to do them. To implement the 5S system, employees must acquire new skills and techniques.
The 5S Method not only improves efficiency, but it also helps employees to be more productive and happier. Once they start to notice improvements, they are motivated to keep working towards their goal of increasing efficiency.