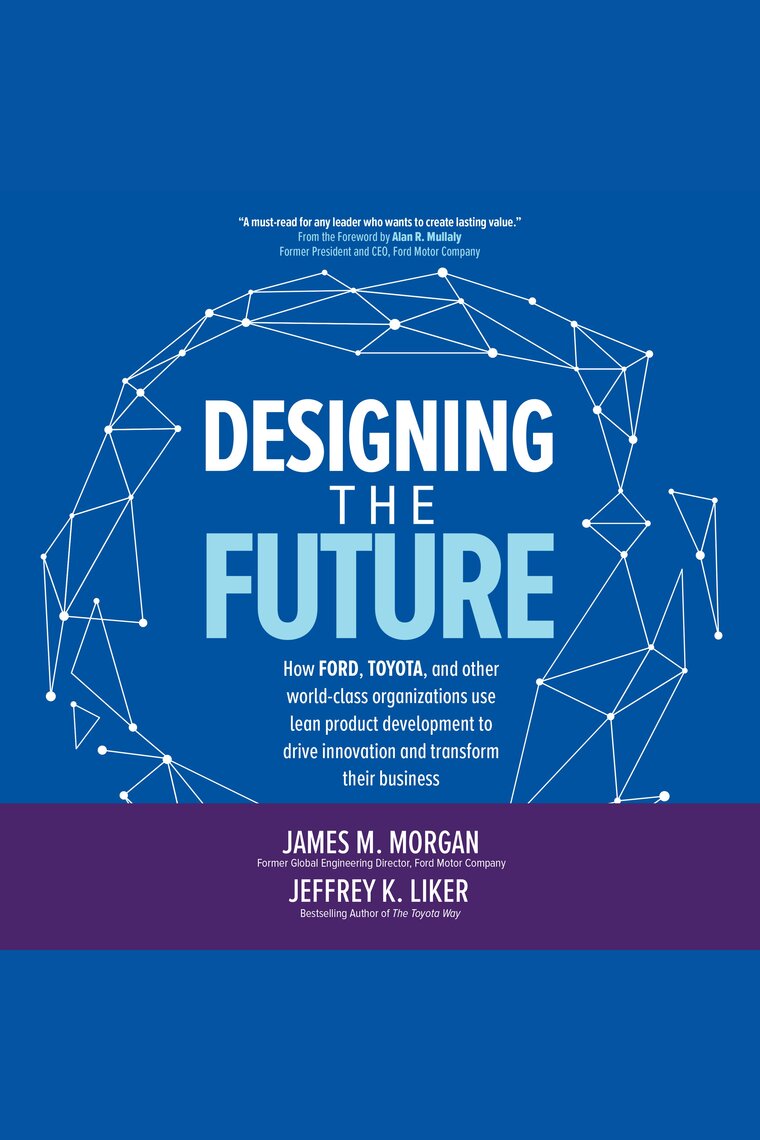
Federal and state government logistics jobs are available in both part time and full time capacities. These jobs offer many benefits to job seekers. They can provide stable income and great benefits. You can also get experience in government jobs.
For example, the Logistics Management Specialist oversees coordination of the supply chains. They oversee deliveries and manage contracts with suppliers. They also work to identify deficiencies in supply chains and develop contingency plans. You must have excellent communication skills, great typing skills, and a good understanding of government procurement regulations.
Supply Chain Management Officers can work for the Department of Veterans Affairs or for the Department of Homeland Security. The first requires an in-depth knowledge of the federal government's procurement regulations. While the second position involves managing logistics operations, sourcing supplies and managing supply chain management. Depending on the job, candidates are required to have a bachelor's degree or higher. In addition, applicants are expected to have a solid knowledge of the business culture and regulations of the state they're applying for. Some positions require security clearances. Applicants may also need to go through a background investigation.
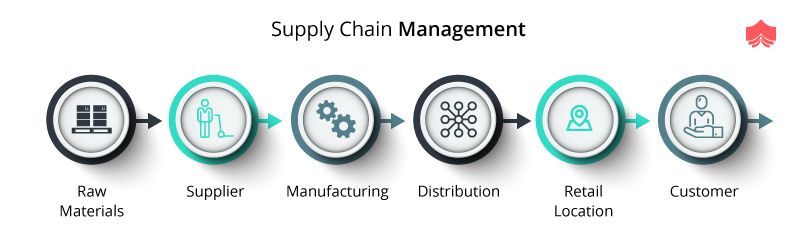
Others jobs for government logistic specialists include deploying materials quickly following an incident. The North Carolina Department of Public Safety, for example, offers a role in distribution of disaster logistics. Candidates should have at least four years of relevant experience. The position requires the candidate to be able manage people under stress.
Logistics Management Specialists are also needed at the departmental level. The Federal Aviation Administration is the typical logistic management specialist role. You will need to have an advanced degree, experience in operations and project management, as well as a background in logistics.
A career as a logistics coordinator for government agencies will require you to have experience managing large volumes of international travel. You will also need experience in managing suppliers bids and procurement negotiations. Candidates should have at the very least two years of relevant work experience.
The federal government has many other supply-chain management roles you can apply to. Those positions are in the areas of air transport, road transport, warehousing, and distribution. Nearly one quarter of these jobs are offered by federal government. The states offer another eight percent.
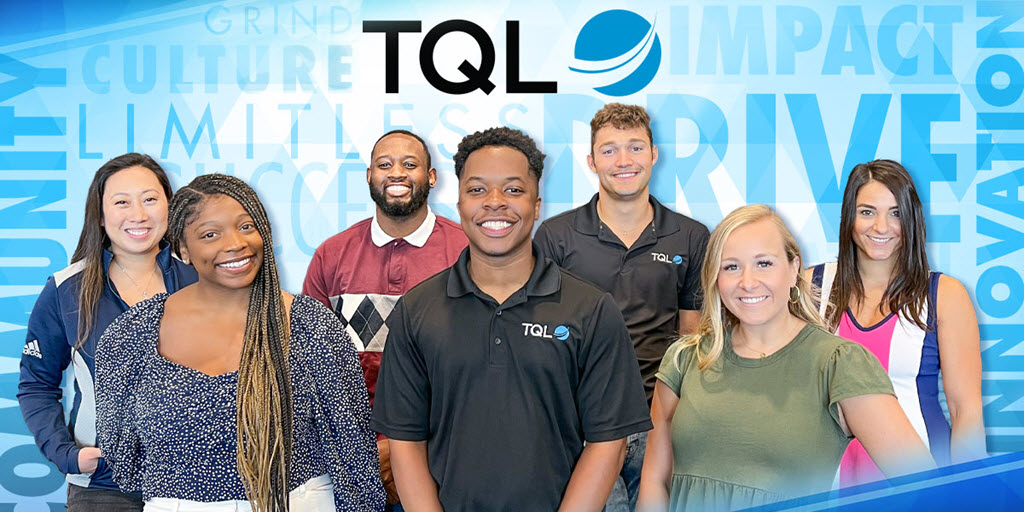
You can search the USAJOBS website for a variety of jobs. You can also search for a title or degree type. While most of these jobs require at minimum a bachelor's degree in order to be eligible, some may require a masters. Supply chain specialists can also be found at smaller organizations. For most supply chain professionals, a minimum of one year of specialized work experience is required before they can apply to a position.
There are many positions available for data scientists. Data Scientists help in the development of strategic plans and support government programs.
FAQ
Why should you automate your warehouse?
Automation has become increasingly important in modern warehousing. With the rise of ecommerce, there is a greater demand for faster delivery times as well as more efficient processes.
Warehouses should be able adapt quickly to new needs. In order to do this, they need to invest in technology. Automating warehouses has many benefits. Here are some benefits of investing in automation
-
Increases throughput/productivity
-
Reduces errors
-
Improves accuracy
-
Boosts safety
-
Eliminates bottlenecks
-
Allows companies scale more easily
-
It makes workers more efficient
-
Provides visibility into everything that happens in the warehouse
-
Enhances customer experience
-
Improves employee satisfaction
-
Reduces downtime and improves uptime
-
Quality products delivered on time
-
Eliminates human error
-
It ensures compliance with regulations
What is the role of a manager in manufacturing?
Manufacturing managers must ensure that manufacturing processes are efficient, effective, and cost-effective. They should also be aware of any problems within the company and act accordingly.
They must also be able to communicate with sales and marketing departments.
They should be informed about industry trends and be able make use of this information to improve their productivity and efficiency.
What are the products and services of logistics?
Logistics refers to the movement of goods from one place to another.
They include all aspects of transport, including packaging, loading, transporting, unloading, storing, warehousing, inventory management, customer service, distribution, returns, and recycling.
Logisticians ensure that the product is delivered to the correct place, at the right time, and under safe conditions. They assist companies with their supply chain efficiency through information on demand forecasts. Stock levels, production times, and availability.
They coordinate with vendors and suppliers, keep track of shipments, monitor quality standards and perform inventory and order replenishment.
What is production plan?
Production Planning is the creation of a plan to cover all aspects, such as scheduling, budgeting. Location, crew, equipment, props and other details. This document aims to ensure that everything is planned and ready when you are ready to shoot. This document should also include information on how to get the best result on set. This includes shooting schedules, locations, cast lists, crew details, and equipment requirements.
The first step is to decide what you want. You may have already chosen the location you want, or there are locations or sets you prefer. Once you have identified your locations and scenes, you can start working out which elements you require for each scene. Perhaps you have decided that you need to buy a car but aren't sure which model. In this case, you could start looking up cars online to find out what models are available and then narrow your choices by choosing between different makes and models.
After you've found the perfect car, it's time to start thinking about adding extras. Do you have people who need to be seated in the front seat? You might also need someone to help you get around the back. Maybe you want to change the interior color from black to white? These questions will help you determine the exact look and feel of your car. Another thing you can do is think about what type of shots are desired. You will be filming close-ups and wide angles. Maybe you want to show your engine or the steering wheel. All of these things will help you identify the exact style of car you want to film.
Once you've determined the above, it is time to start creating a calendar. You will know when you should start and when you should finish shooting. Every day will have a time for you to arrive at the location, leave when you are leaving and return home when you are done. Everyone will know what they need and when. If you need to hire extra staff, you can make sure you book them in advance. You should not hire anyone who doesn't show up because of your inaction.
When creating your schedule, you will also need to consider the number of days you need to film. Some projects are quick and easy, while others take weeks. When you are creating your schedule, you should always keep in mind whether you need more than one shot per day or not. Multiplying takes in the same area will result both in increased costs and a longer time. It is better to be cautious and take fewer shots than you risk losing money if you are not sure if multiple takes are necessary.
Budget setting is an important part of production planning. Setting a realistic budget is essential as it will allow you to work within your means. If you have to reduce your budget due to unexpected circumstances, you can always lower it later. You shouldn't underestimate the amount you'll spend. If you underestimate how much something costs, you'll have less money to pay for other items.
Planning production is a tedious process. Once you have a good understanding of how everything works together, planning future projects becomes easy.
What does it mean to warehouse?
A warehouse is a place where goods are stored until they are sold. You can have it indoors or outdoors. It may also be an indoor space or an outdoor area.
Statistics
- Job #1 is delivering the ordered product according to specifications: color, size, brand, and quantity. (netsuite.com)
- (2:04) MTO is a production technique wherein products are customized according to customer specifications, and production only starts after an order is received. (oracle.com)
- [54][55] These are the top 50 countries by the total value of manufacturing output in US dollars for its noted year according to World Bank.[56] (en.wikipedia.org)
- In the United States, for example, manufacturing makes up 15% of the economic output. (twi-global.com)
- You can multiply the result by 100 to get the total percent of monthly overhead. (investopedia.com)
External Links
How To
How to use the Just-In Time Method in Production
Just-intime (JIT), which is a method to minimize costs and maximize efficiency in business process, is one way. It's a way to ensure that you get the right resources at just the right time. This means that you only pay for what you actually use. Frederick Taylor was the first to coin this term. He developed it while working as a foreman during the early 1900s. After observing how workers were paid overtime for late work, he realized that overtime was a common practice. He concluded that if workers were given enough time before they start work, productivity would increase.
JIT teaches you to plan ahead and prepare everything so you don’t waste time. Also, you should look at the whole project from start-to-finish and make sure you have the resources necessary to address any issues. If you expect problems to arise, you will be able to provide the necessary equipment and personnel to address them. You won't have to pay more for unnecessary items.
There are several types of JIT techniques:
-
Demand-driven: This is a type of JIT where you order the parts/materials needed for your project regularly. This will allow for you to track the material that you have left after using it. You'll also be able to estimate how long it will take to produce more.
-
Inventory-based: You stock materials in advance to make your projects easier. This allows you to predict how much you can expect to sell.
-
Project-driven: This method allows you to set aside enough funds for your project. Knowing how much money you have available will help you purchase the correct amount of materials.
-
Resource-based JIT : This is probably the most popular type of JIT. Here you can allocate certain resources based purely on demand. You might assign more people to help with orders if there are many. If there aren't many orders, you will assign fewer people.
-
Cost-based: This is the same as resource-based except that you don't care how many people there are but how much each one of them costs.
-
Price-based: This is a variant of cost-based. However, instead of focusing on the individual workers' costs, this looks at the total price of the company.
-
Material-based - This is a variant of cost-based. But instead of looking at the total company cost, you focus on how much raw material you spend per year.
-
Time-based: Another variation of resource-based JIT. Instead of focusing on the cost of each employee, you will focus on the time it takes to complete a project.
-
Quality-based JIT is another variant of resource-based JIT. Instead of looking at the labor costs and time it takes to make a product, think about its quality.
-
Value-based: This is one of the newest forms of JIT. This is where you don't care about how the products perform or whether they meet customers' expectations. Instead, you are focused on adding value to the marketplace.
-
Stock-based: This inventory-based approach focuses on how many items are being produced at any one time. It's used when you want to maximize production while minimizing inventory.
-
Just-intime (JIT), planning is a combination JIT management and supply chain management. It is the process of scheduling components' delivery as soon as they have been ordered. It's important as it reduces leadtimes and increases throughput.