
Logistics is an integral component of any supply chain. Product movement must take place from start to finish. Logistics is an essential part of any company's operations in today's fast-paced economy. A highly trained workforce is essential for effective logistics. Logistic supply chains include the efficient and timely movement and information of goods, resources, and information. But what exactly does logistics mean? This article will discuss some important aspects of logistic supply chain.
Logistics is the movement and storage of products from one point to another.
The process of moving goods from point A to B is called logistics. These activities are overseen and managed by logistics managers. They must consider numerous details when moving products from one point to another. They have to decide which shipping method is best for each product, weigh it and consider recyclability, as well as ensure that the final cost of shipment covers the entire load. They must also keep in mind customer satisfaction and warehousing needs, which all contribute to fully loaded costs.
It is an essential component of a supply chain
The logistics process involves identifying problem areas within the supply chain and resolving them. These areas can lead to high costs and waste. It is possible for a product to be ordered in large quantities and then remain on a stock shelf for several hours. Transport providers can also be subject to high transportation costs. Overproduction can lead to problems as companies produce more than they use. This leads to wasted resources that can adversely impact the market price.
It requires a well-trained workforce
It is vital to have a skilled workforce for logistics supply chains. A skilled workforce can give a company an advantage and help ensure that logistics facilities run smoothly. It is important to reward employees for exceeding their expectations. Total Logistics Solutions consultants actually work in warehouses to understand how the process works from the user's point of view. It is also beneficial to be familiar with your competitors. This is why Total Logistics Solutions consultants are recommended.
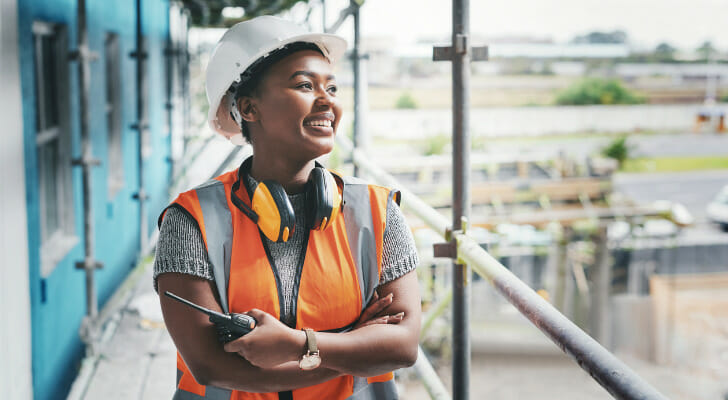
It requires technology
The logistics industry must be competitive. Technological advances are changing not only the industry's landscape but also how it operates. The logistics industry is changing with the advent of advanced analytics, additive manufacturing, automation, and other technological advances. As a result, autonomous vehicles will increase in warehouses. Warehouse management and warehousing strategies will also undergo significant changes. These advances will ultimately make logistics easier and more cost-effective.
FAQ
How is a production manager different from a producer planner?
A production planner is more involved in the planning phase of the project than a project manger.
What are my options for learning more about manufacturing
Hands-on experience is the best way to learn more about manufacturing. However, if that's not possible, you can always read books or watch educational videos.
What is the difference in Production Planning and Scheduling, you ask?
Production Planning (PP), or production planning, is the process by which you determine what products are needed at any given time. This is accomplished by forecasting the demand and identifying production resources.
Scheduling is the process that assigns dates to tasks so they can get completed within a given timeframe.
Can some manufacturing processes be automated?
Yes! Yes. Automation has been around since ancient time. The Egyptians invent the wheel thousands of year ago. Nowadays, we use robots for assembly lines.
Actually, robotics can be used in manufacturing for many purposes. These include:
-
Automated assembly line robots
-
Robot welding
-
Robot painting
-
Robotics inspection
-
Robots that produce products
There are many other examples of how manufacturing could benefit from automation. 3D printing, for example, allows us to create custom products without waiting for them to be made.
What are the 7 Rs of logistics?
The acronym 7R's for Logistics stands to represent the seven basic principles in logistics management. It was developed by the International Association of Business Logisticians (IABL) and published in 2004 as part of its "Seven Principles of Logistics Management" series.
The acronym consists of the following letters:
-
Responsible - ensure that actions are in compliance with legal requirements and do not cause harm to others.
-
Reliable - You can have confidence that you will fulfill your promises.
-
It is reasonable to use resources efficiently and not waste them.
-
Realistic – consider all aspects of operations, from cost-effectiveness to environmental impact.
-
Respectful – Treat others fairly and equitably.
-
Responsive - Look for ways to save time and increase productivity.
-
Recognizable: Provide customers with value-added service
How can manufacturing avoid production bottlenecks
To avoid production bottlenecks, ensure that all processes run smoothly from the moment you receive your order to the time the product ships.
This includes planning for capacity requirements as well as quality control measures.
Continuous improvement techniques like Six Sigma are the best way to achieve this.
Six Sigma is a management system used to improve quality and reduce waste in every aspect of your organization.
It seeks to eliminate variation and create consistency in your work.
Statistics
- According to a Statista study, U.S. businesses spent $1.63 trillion on logistics in 2019, moving goods from origin to end user through various supply chain network segments. (netsuite.com)
- In the United States, for example, manufacturing makes up 15% of the economic output. (twi-global.com)
- It's estimated that 10.8% of the U.S. GDP in 2020 was contributed to manufacturing. (investopedia.com)
- According to the United Nations Industrial Development Organization (UNIDO), China is the top manufacturer worldwide by 2019 output, producing 28.7% of the total global manufacturing output, followed by the United States, Japan, Germany, and India.[52][53] (en.wikipedia.org)
- Many factories witnessed a 30% increase in output due to the shift to electric motors. (en.wikipedia.org)
External Links
How To
How to Use lean manufacturing in the Production of Goods
Lean manufacturing is a management system that aims at increasing efficiency and reducing waste. It was developed in Japan during the 1970s and 1980s by Taiichi Ohno, who received the Toyota Production System (TPS) award from TPS founder Kanji Toyoda. The first book published on lean manufacturing was titled "The Machine That Changed the World" written by Michael L. Watkins and published in 1990.
Lean manufacturing is often defined as a set of principles used to improve the quality, speed, and cost of products and services. It emphasizes eliminating waste and defects throughout the value stream. Lean manufacturing can be described as just-in–time (JIT), total productive maintenance, zero defect (TPM), or even 5S. Lean manufacturing is about eliminating activities that do not add value, such as inspection, rework, and waiting.
Lean manufacturing is a way for companies to achieve their goals faster, improve product quality, and lower costs. Lean manufacturing can be used to manage all aspects of the value chain. Customers, suppliers, distributors, retailers and employees are all included. Lean manufacturing is widely practiced in many industries around the world. Toyota's philosophy, for example, is what has enabled it to be successful in electronics, automobiles, medical devices, healthcare and chemical engineering as well as paper and food.
Five fundamental principles underlie lean manufacturing.
-
Define Value: Identify the social value of your business and what sets you apart.
-
Reduce waste - Get rid of any activity that does not add value to the supply chain.
-
Create Flow - Make sure work runs smoothly without interruptions.
-
Standardize & Simplify - Make processes as consistent and repeatable as possible.
-
Develop Relationships: Establish personal relationships both with internal and external stakeholders.
Lean manufacturing, although not new, has seen renewed interest in the economic sector since 2008. Many businesses have adopted lean manufacturing techniques to help them become more competitive. Many economists believe lean manufacturing will play a major role in economic recovery.
Lean manufacturing, which has many benefits, is now a standard practice in the automotive industry. These include higher customer satisfaction levels, reduced inventory levels as well as lower operating costs.
You can apply Lean Manufacturing to virtually any aspect of your organization. It is especially useful for the production aspect of an organization, as it ensures that every step in the value chain is efficient and effective.
There are three main types of lean manufacturing:
-
Just-in-Time Manufacturing (JIT): This type of lean manufacturing is commonly referred to as "pull systems." JIT is a process in which components can be assembled at the point they are needed, instead of being made ahead of time. This method reduces lead times, increases availability, and decreases inventory.
-
Zero Defects Manufacturing - ZDM: ZDM focuses its efforts on making sure that no defective units leave a manufacturing facility. If a part needs to be fixed during the assembly line, it should be repaired rather than scrapped. This is also true for finished products that require minor repairs before shipping.
-
Continuous Improvement: Continuous Improvement aims to improve efficiency by continually identifying problems and making adjustments to eliminate or minimize waste. Continuous improvement involves continuous improvement of processes and people as well as tools.