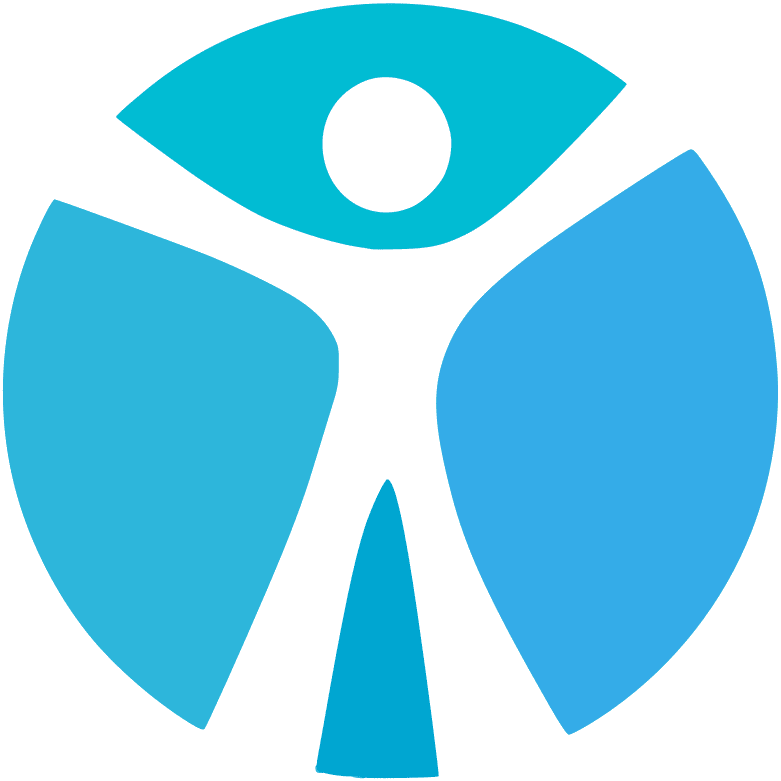
CEVA Logistics is a company providing logistics services. These logistics companies offer many benefits to employees, whether you are looking for a career change or simply want to find a new job. Here's how you can apply to a logistics job at one of these companies. First, you can look for jobs by location.
Job description
CEVA Logistics has many job openings for people with varied education and work experiences. The company's core values revolve around customer service and prompt delivery. The company seeks people who are passionate about logistics, and who are willing work hard. When applying for a job, candidates with prior experience in logistics will be preferred. Candidates who are positive and have a positive attitude would also be considered.
CEVA Logistics needs a Process/Industrial Manager to develop new processes and improve efficiency. The ideal candidate must be self-motivated, energetic, and able work well with others. Their duties include designing and implementing process layouts, managing projects, and using analytical and modeling skills. They should also be skilled in robotics and other manufacturing processes, which will increase quality and efficiency.
Education required
CEVA Logistics has many career options for those who are interested in working there. These include warehouse manager and sales rep. They may also be eligible to become operations supervisors. These positions involve managing the day-today operations of CEVA Logistics, such as scheduling and inventory management, customer service, and customer support. These positions usually have a team. Candidates for these positions usually have a bachelor’s degree in logistics, supervisory and strong leadership and management skills.
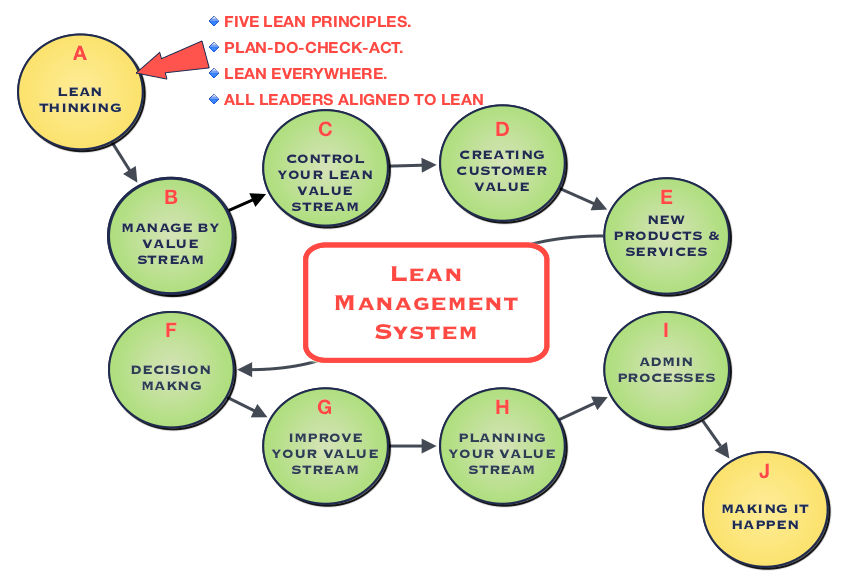
Online applications are accepted from interested applicants. To apply online, candidates first need to create a profile with the company's career portal. To connect to their LinkedIn profile, they can attach their resumes and other relevant information. After creating their profile, they can choose the desired country or region and get in touch to a recruiter.
Salary range
The first step in applying for a CEVA Logistics job is to create an online profile through the company's Career Portal. This allows you connect with LinkedIn and to upload your resume. You can also manually enter information about your skills and experience. Next, you will need to choose the region or country in which you want to work. After this step, you will be provided with contact information by a recruiter from that region.
CEVA Logistics has a variety of salaries. These vary depending on your job title, work experience, and geographic location. The salary of the Vice President of CEVA Logistics is $166,000 while that of an Air Break Bulk specialist is $24,000. However, the economic situation in each location can impact the salary.
Locations
If you're looking for a great career in logistics, consider a position with CEVA Logistics. There are many positions available at different locations. Each position has different responsibilities and requirements. To apply for a position, type the job title into the search box. Also, enter your location. You can search for Edison job listings. You must have driving experience and the ability to communicate well with clients and employees.
There are many career opportunities at CEVA Logistics, including supervisory positions. Supervisors are responsible for the company's day to day operations. They are responsible for managing inventory, scheduling, and supervising employees. A supervisor of operations typically has a team that reports to him. They usually need a bachelor's degree, or another related experience. Leadership and management skills are essential.
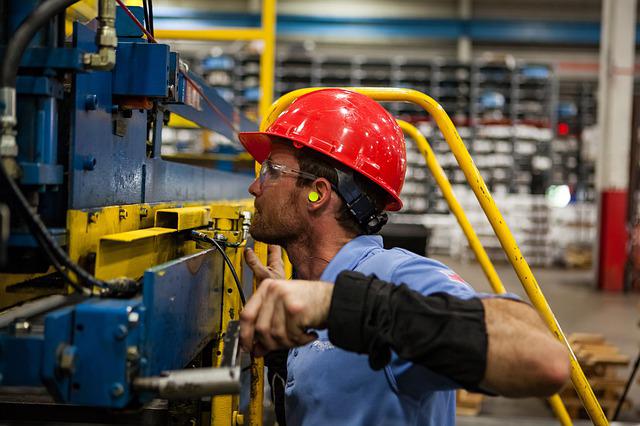
Apply online
CEVA Logistics is an online job board for those looking for jobs in the logistics sector. Ceva Logistics is an international company that was created in 2006 through the merger two Australian and Texan logistics companies. Today, its operations span more than 950 locations in 170 countries. Job seekers are eligible to apply for either full-time or partial-time positions.
Although some positions at CEVA may require some experience in order to be successful, many are entry-level. Other positions require little or no experience. Customer service representative, dispatcher, and admin clerk are some of the entry-level jobs.
FAQ
What's the difference between Production Planning & Scheduling?
Production Planning (PP), or production planning, is the process by which you determine what products are needed at any given time. This is done through forecasting demand and identifying production capacities.
Scheduling is the process of assigning specific dates to tasks so they can be completed within the specified timeframe.
Why is logistics important for manufacturing?
Logistics are essential to any business. They are essential to any business's success.
Logistics play an important role in reducing costs as well as increasing efficiency.
How can we improve manufacturing efficiency?
First, we need to identify which factors are most critical in affecting production times. We then need to figure out how to improve these variables. If you don’t know how to start, look at which factors have the greatest impact upon production time. Once you've identified them, try to find solutions for each of those factors.
Is automation important in manufacturing?
Automating is not just important for manufacturers, but also for service providers. It enables them to provide services faster and more efficiently. They can also reduce their costs by reducing human error and improving productivity.
Statistics
- You can multiply the result by 100 to get the total percent of monthly overhead. (investopedia.com)
- It's estimated that 10.8% of the U.S. GDP in 2020 was contributed to manufacturing. (investopedia.com)
- In 2021, an estimated 12.1 million Americans work in the manufacturing sector.6 (investopedia.com)
- (2:04) MTO is a production technique wherein products are customized according to customer specifications, and production only starts after an order is received. (oracle.com)
- Job #1 is delivering the ordered product according to specifications: color, size, brand, and quantity. (netsuite.com)
External Links
How To
How to use the Just In-Time Production Method
Just-in time (JIT), is a process that reduces costs and increases efficiency in business operations. It's a way to ensure that you get the right resources at just the right time. This means that your only pay for the resources you actually use. Frederick Taylor, a 1900s foreman, first coined the term. After observing how workers were paid overtime for late work, he realized that overtime was a common practice. He realized that workers should have enough time to complete their jobs before they begin work. This would help increase productivity.
The idea behind JIT is that you should plan ahead and have everything ready so you don't waste money. You should also look at the entire project from start to finish and make sure that you have sufficient resources available to deal with any problems that arise during the course of your project. If you anticipate that there might be problems, you'll have enough people and equipment to fix them. This will ensure that you don't spend more money on things that aren't necessary.
There are many JIT methods.
-
Demand-driven: This JIT is where you place regular orders for the parts/materials that are needed for your project. This will allow for you to track the material that you have left after using it. This will let you know how long it will be to produce more.
-
Inventory-based: This is a type where you stock the materials required for your projects in advance. This allows you to forecast how much you will sell.
-
Project-driven: This approach involves setting aside sufficient funds to cover your project's costs. Knowing how much money you have available will help you purchase the correct amount of materials.
-
Resource-based JIT: This is the most popular form of JIT. This is where you assign resources based upon demand. For example, if there is a lot of work coming in, you will have more people assigned to them. If you don’t have many orders you will assign less people to the work.
-
Cost-based: This approach is very similar to resource-based. However, you don't just care about the number of people you have; you also need to consider how much each person will cost.
-
Price-based: This approach is very similar to the cost-based method except that you don't look at individual workers costs but the total cost of the company.
-
Material-based - This is a variant of cost-based. But instead of looking at the total company cost, you focus on how much raw material you spend per year.
-
Time-based JIT: A variation on resource-based JIT. Instead of worrying about how much each worker costs, you can focus on how long the project takes.
-
Quality-based JIT: Another variation on resource-based JIT. Instead of focusing on the cost of each worker or how long it takes, think about how high quality your product is.
-
Value-based JIT : This is the newest type of JIT. In this case, you're not concerned with how well the products perform or whether they meet customer expectations. Instead, you're focused on how much value you add to the market.
-
Stock-based: This inventory-based approach focuses on how many items are being produced at any one time. It is used when production goals are met while inventory is kept to a minimum.
-
Just-in-time (JIT) planning: This is a combination of JIT and supply chain management. It's the process of scheduling delivery of components immediately after they are ordered. It's important as it reduces leadtimes and increases throughput.