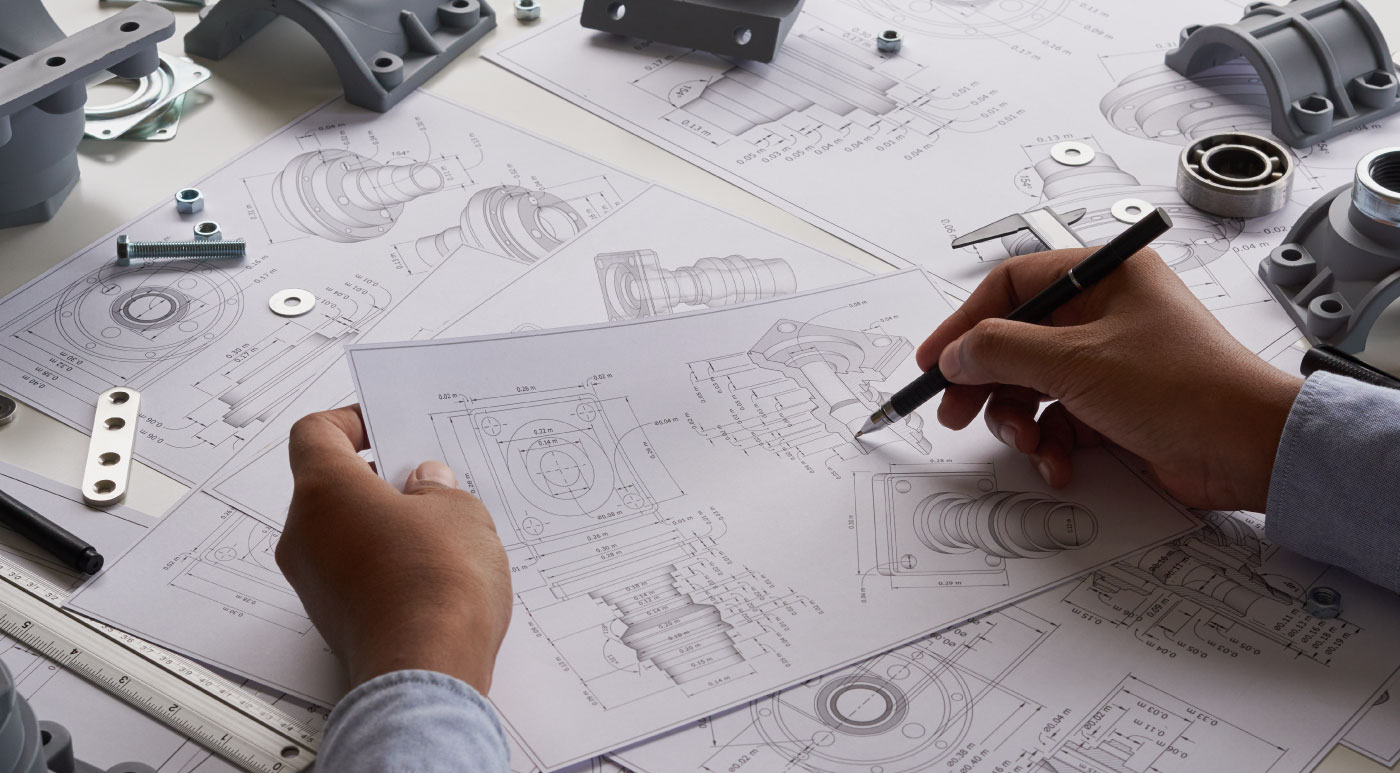
Manufacturing fails can be caused by a number of things, including poor design, cost-cutting initiatives, lack of quality control and more. There are a number of ways to avoid problems and improve product quality.
In many cases, companies that implement lean practices are very successful. These companies have been able to reduce waste and improve cycles times among other benefits. But they have to do it through a lot trial and errors and failure.
Most lean experts will agree that senior management and ownership are the primary reasons for failures in implementation. The people in charge of the company are usually not aware of how to implement lean.
This can make it very difficult to get employees on board and to achieve the expected results, which are why it's important to begin a skills assessment well in advance of implementing lean practices. By identifying those who are able and willing to assist in your goal-achieving and those who need to be let go, you can remove much ambiguity.
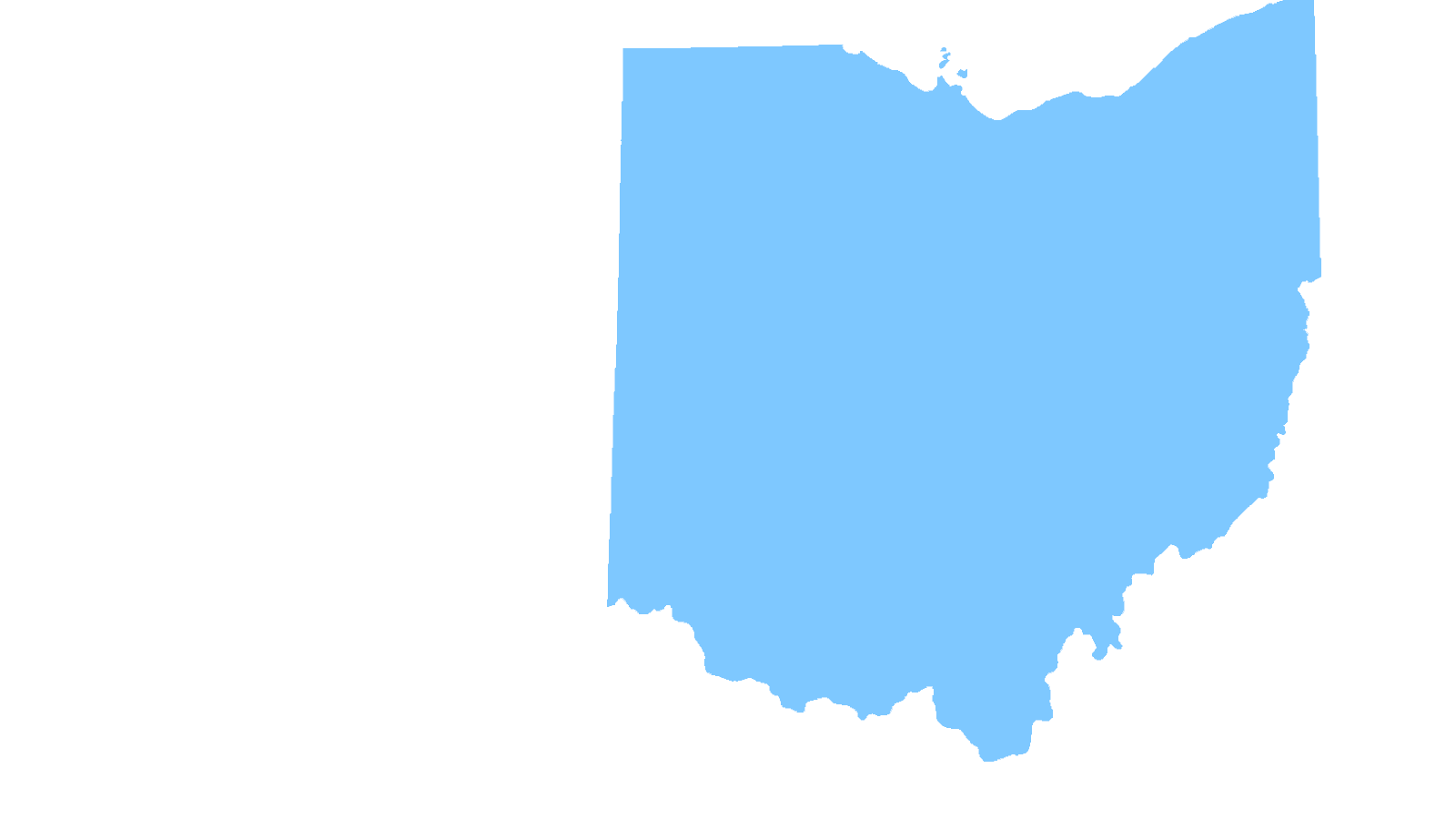
Why do manufacturers fail to meet expectations?
Some manufacturing mistakes are caused because the manufacturer used the wrong material or didn't implement proper quality assurance measures. Other defects are caused by manufacturing errors, which are when a product is made in a way that it's not designed to be. These mistakes can be expensive to fix and can even result in loss of revenue for the company.
This can lead to costly problems for both the consumer and the manufacturer. To prevent such problems, it is important that companies are able to detect and correct manufacturing errors as early as they can.
In order to accomplish this goal, manufacturers need to understand the causes of machine failures. This will help them improve their processes and reduce costs.
One of the most common failures is when a manufacturer does not have enough capital. This can be a result of a number different factors. However it is vital that a company has sufficient capital to continue their production and sales for the long-term.
The manufacturer and consumer can both be affected by a lack of funds. This can cause a number of problems, including a delay in the delivery or a lower price for the product.
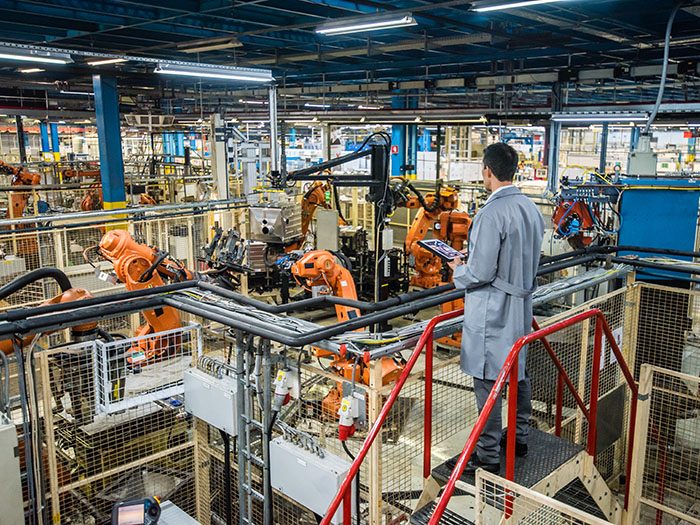
This can cause injury for the consumer if the product is being used in an unsafe manner. The manufacturer may be held responsible if, for example, someone breaks a bone while playing with a match which starts a blaze.
It can be very dangerous, especially for young children who have not been exposed to hazardous materials. For the manufacturer it can be very expensive to fix this issue but is crucial for any business to survive.
FAQ
What is the role and responsibility of a Production Planner?
Production planners ensure all aspects of the project are delivered within time and budget. A production planner ensures that the service and product meet the client's expectations.
What skills should a production planner have?
You must be flexible and organized to become a productive production planner. Effective communication with clients and colleagues is essential.
How is a production manager different from a producer planner?
The major difference between a Production Planner and a Project Manager is that a Project Manager is often the person responsible for organizing and planning the entire project. While a Production Planner is involved mainly in the planning stage,
Statistics
- Job #1 is delivering the ordered product according to specifications: color, size, brand, and quantity. (netsuite.com)
- In 2021, an estimated 12.1 million Americans work in the manufacturing sector.6 (investopedia.com)
- It's estimated that 10.8% of the U.S. GDP in 2020 was contributed to manufacturing. (investopedia.com)
- According to a Statista study, U.S. businesses spent $1.63 trillion on logistics in 2019, moving goods from origin to end user through various supply chain network segments. (netsuite.com)
- (2:04) MTO is a production technique wherein products are customized according to customer specifications, and production only starts after an order is received. (oracle.com)
External Links
How To
Six Sigma: How to Use it in Manufacturing
Six Sigma is defined as "the application of statistical process control (SPC) techniques to achieve continuous improvement." Motorola's Quality Improvement Department developed it at their Tokyo plant in Japan in 1986. The basic idea behind Six Sigma is to improve quality by improving processes through standardization and eliminating defects. In recent years, many companies have adopted this method because they believe there is no such thing as perfect products or services. Six Sigma's main objective is to reduce variations from the production average. If you take a sample and compare it with the average, you will be able to determine how much of the production process is different from the norm. If the deviation is excessive, it's likely that something needs to be fixed.
Understanding the dynamics of variability within your business is the first step in Six Sigma. Once you understand that, it is time to identify the sources of variation. It is important to identify whether the variations are random or systemic. Random variations happen when people make errors; systematic variations are caused externally. You could consider random variations if some widgets fall off the assembly lines. If however, you notice that each time you assemble a widget it falls apart in exactly the same spot, that is a problem.
Once you identify the problem areas, it is time to create solutions. This could mean changing your approach or redesigning the entire process. After implementing the new changes, you should test them again to see if they worked. If they don't work you need to rework them and come up a better plan.