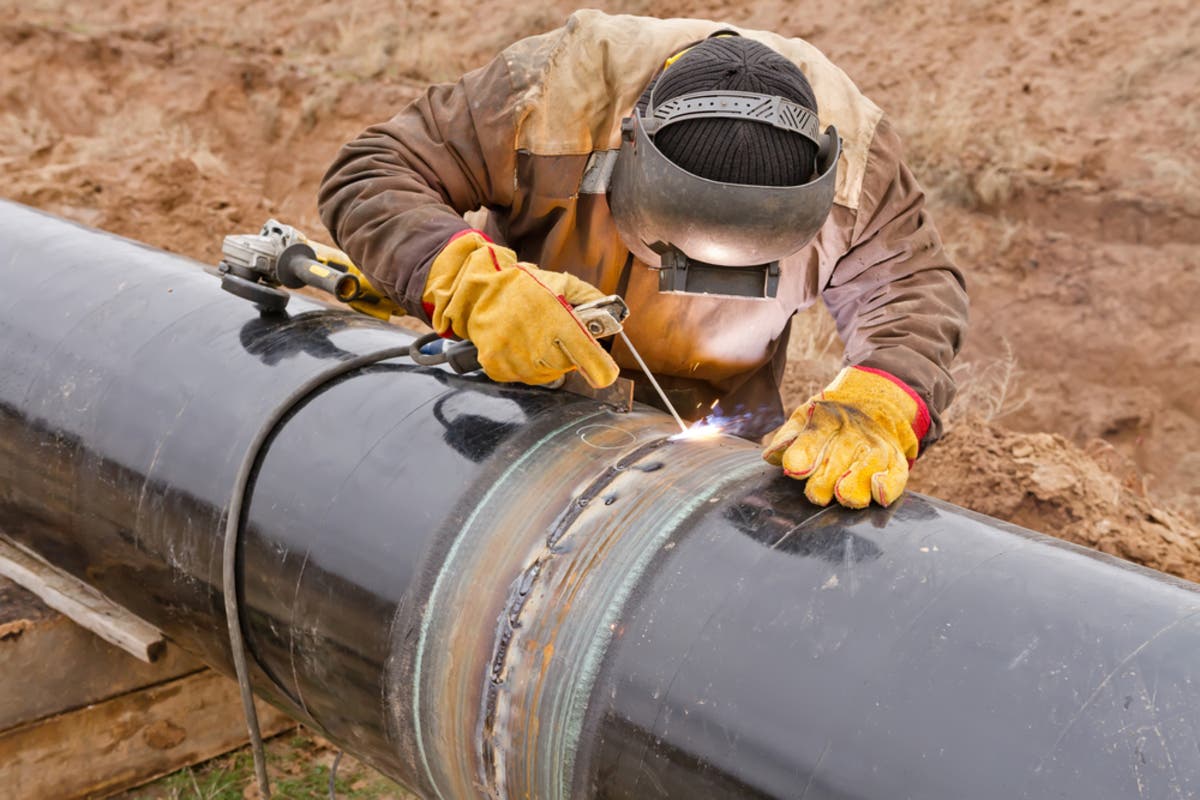
A chemical engineer refers to a person with expertise in the fields of chemistry or engineering. These engineers create and operate equipment and processes that convert raw material into products. They are responsible to oversee the entire production process from design of plant layouts to operation of equipment. Whatever your interests, a chemical engineering degree could be lucrative and highly rewarding. Here are some career options within the field of chemical engineering. They are a valuable asset to every industry that they work in.
Aerospace engineering ranks as the most difficult major.
This major in aerospace engineering requires high levels of discipline. You won't find much room for college parties with this major. You will be expected to spend hours learning and doing course-related work. This is often called rocket science. Aerospace engineering deals with the design and construction of spacecraft. This includes both the aeronautical and astronautical branches. Students will need to be able to handle a lot of mathematical work and fluid dynamics.
The easiest major is chemical engineering
The first step to pursuing a career in chemical engineering is to achieve a high high school grade point average (GPA). Colleges expect chemical engineering majors at high school to be able to handle rigorous coursework. Taking AP classes can make you stand out to admissions officers. AP classes also give students a solid academic foundation. Chemical engineers can expect a well-paying job with an average salary of $96,300 by 2020.
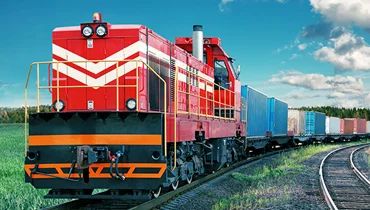
It requires math, physics, and chemistry
Most undergraduate degrees in chemical engineering are four-year long and require 120 to 130 credits. Students will learn to create, manufacture, analyze, and process chemical products and equipment. The chemical engineering program offers students the opportunity to take courses in math and physics as well as cooperative education and internships. Some programs offer doctoral degrees. To qualify for a PhD, you'll need to have at least a bachelor's degree in chemical engineering.
It is a stable industry
There are many kinds of jobs in chemical engineering. Although many chemical engineers work in labs and offices, some spend time on the job. They also manage operations and solve issues on site. While they work long hours to meet deadlines. They might also be available at short notice. This field requires knowledge of many complex topics. To design the best process, a chemical engineer might use computer aided design software.
It pays well
You have many options if you are a recent college grad looking for an entry-level position. An internship is an option if a job has not been advertised. ExxonMobil may have positions open at their company. You can find jobs in engineering, finance and operations. Focus on your expertise in operations, geophysics or information technology.
It's a relatively new subject
Chemistry is an exciting and challenging subject. As a student of chemical engineering, you will learn about the many applications of this subject. You will learn how to design and build industrial processes with complex operations. Learn about unit operations in chemical plants as well as the consequences of changing the variables. Innovative approaches have been applied throughout the history in chemical engineering to increase student understanding and participation.
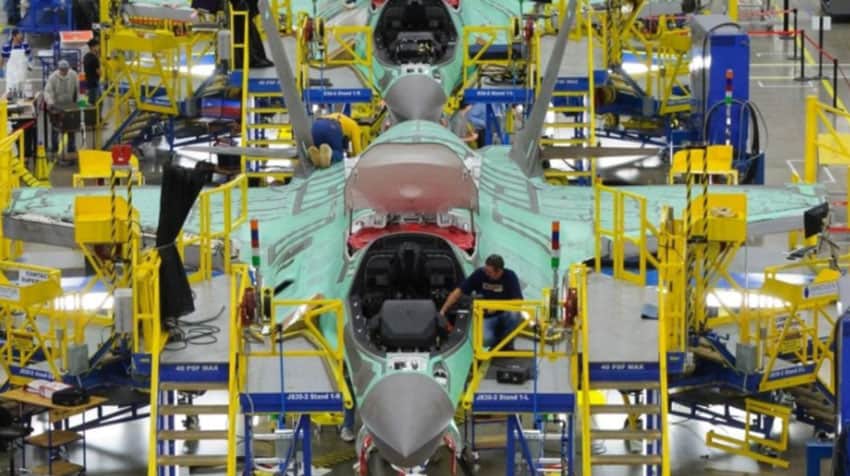
It is a good fit for students who want to be in the field
If you are interested in a career in the chemical industry, there are several reasons to major in chemical engineering. Chemical engineering is not only a specialist field, but it also integrates with other disciplines like electrical and mechanical engineering. Chemical engineers are skilled in solving problems related to the manufacture, use, or transportation of chemicals. Some of the chemicals that are produced and used today include fuel, drugs, and food. Depending upon your interests, you might choose to specialize in a subset of the field, like environmental or biotechnology.
FAQ
How can manufacturing prevent production bottlenecks?
The key to avoiding bottlenecks in production is to keep all processes running smoothly throughout the entire production cycle, from the time you receive an order until the time when the product ships.
This includes planning for capacity requirements as well as quality control measures.
Continuous improvement techniques like Six Sigma are the best way to achieve this.
Six Sigma can be used to improve the quality and decrease waste in all areas of your company.
It focuses on eliminating variation and creating consistency in your work.
What is the responsibility of a manufacturing manager?
A manufacturing manager must ensure that all manufacturing processes are efficient and effective. They should also be aware and responsive to any company problems.
They should also know how to communicate with other departments such as sales and marketing.
They should be informed about industry trends and be able make use of this information to improve their productivity and efficiency.
What is the difference in Production Planning and Scheduling, you ask?
Production Planning (PP), is the process of deciding what production needs to take place at any given time. This is done through forecasting demand and identifying production capacities.
Scheduling refers the process by which tasks are assigned dates so that they can all be completed within the given timeframe.
What is the best way to learn about manufacturing?
Hands-on experience is the best way to learn more about manufacturing. However, if that's not possible, you can always read books or watch educational videos.
How can manufacturing overproduction be reduced?
The key to reducing overproduction lies in developing better ways to manage inventory. This would reduce the time spent on unproductive activities like purchasing, storing and maintaining excess stock. This would allow us to use our resources for more productive tasks.
Kanban systems are one way to achieve this. A Kanban board, a visual display to show the progress of work, is called a Kanban board. In a Kanban system, work items move through a sequence of states until they reach their final destination. Each state represents a different priority.
As an example, if work is progressing from one stage of the process to another, then the current task is complete and can be transferred to the next. It is possible to keep a task in the beginning stages until it gets to the end.
This keeps work moving and ensures no work is lost. Managers can see how much work has been done and the status of each task at any time with a Kanban Board. This information allows managers to adjust their workflow based off real-time data.
Lean manufacturing is another option to control inventory levels. Lean manufacturing is about eliminating waste from all stages of the production process. Waste includes anything that does not add value to the product. Some common types of waste include:
-
Overproduction
-
Inventory
-
Unnecessary packaging
-
Materials in excess
These ideas can help manufacturers improve efficiency and reduce costs.
Statistics
- It's estimated that 10.8% of the U.S. GDP in 2020 was contributed to manufacturing. (investopedia.com)
- In the United States, for example, manufacturing makes up 15% of the economic output. (twi-global.com)
- According to the United Nations Industrial Development Organization (UNIDO), China is the top manufacturer worldwide by 2019 output, producing 28.7% of the total global manufacturing output, followed by the United States, Japan, Germany, and India.[52][53] (en.wikipedia.org)
- According to a Statista study, U.S. businesses spent $1.63 trillion on logistics in 2019, moving goods from origin to end user through various supply chain network segments. (netsuite.com)
- In 2021, an estimated 12.1 million Americans work in the manufacturing sector.6 (investopedia.com)
External Links
How To
How to Use Lean Manufacturing in the Production of Goods
Lean manufacturing (or lean manufacturing) is a style of management that aims to increase efficiency, reduce waste and improve performance through continuous improvement. It was developed by Taiichi Okono in Japan, during the 1970s & 1980s. TPS founder Kanji Takoda awarded him the Toyota Production System Award (TPS). Michael L. Watkins published the "The Machine That Changed the World", the first book about lean manufacturing. It was published in 1990.
Lean manufacturing is often described as a set if principles that help improve the quality and speed of products and services. It emphasizes the elimination and minimization of waste in the value stream. Just-in-time (JIT), zero defect (TPM), and 5S are all examples of lean manufacturing. Lean manufacturing is about eliminating activities that do not add value, such as inspection, rework, and waiting.
Lean manufacturing is a way for companies to achieve their goals faster, improve product quality, and lower costs. Lean manufacturing is considered one of the most effective ways to manage the entire value chain, including suppliers, customers, distributors, retailers, and employees. Lean manufacturing is widely practiced in many industries around the world. Toyota's philosophy is the foundation of its success in automotives, electronics and appliances, healthcare, chemical engineers, aerospace, paper and food, among other industries.
Lean manufacturing is based on five principles:
-
Define value - Find out what your business contributes to society, and what makes it different from other competitors.
-
Reduce waste - Stop any activity that isn't adding value to the supply chains.
-
Create Flow – Ensure that work flows smoothly throughout the process.
-
Standardize and simplify - Make your processes as consistent as possible.
-
Building Relationships – Establish personal relationships with both external and internal stakeholders.
Although lean manufacturing has always been around, it is gaining popularity in recent years because of a renewed interest for the economy after 2008's global financial crisis. To increase their competitiveness, many businesses have turned to lean manufacturing. According to some economists, lean manufacturing could be a significant factor in the economic recovery.
Lean manufacturing has many benefits in the automotive sector. These include improved customer satisfaction, reduced inventory levels, lower operating costs, increased productivity, and better overall safety.
It can be applied to any aspect of an organisation. However, it is particularly useful when applied to the production side of an organization because it ensures that all steps in the value chain are efficient and effective.
There are three main types of lean manufacturing:
-
Just-in-Time Manufacturing: Also known as "pull systems", this type of lean manufacturing uses just-in-time manufacturing (JIT). JIT stands for a system where components are assembled on the spot rather than being made in advance. This approach is designed to reduce lead times and increase the availability of components. It also reduces inventory.
-
Zero Defects Manufacturing (ZDM),: ZDM is a system that ensures no defective units are left the manufacturing facility. If a part is required to be repaired on the assembly line, it should not be scrapped. This is true even for finished products that only require minor repairs prior to shipping.
-
Continuous Improvement (CI): CI aims to improve the efficiency of operations by continuously identifying problems and making changes in order to eliminate or minimize waste. Continuous improvement refers to continuous improvement of processes as well people and tools.