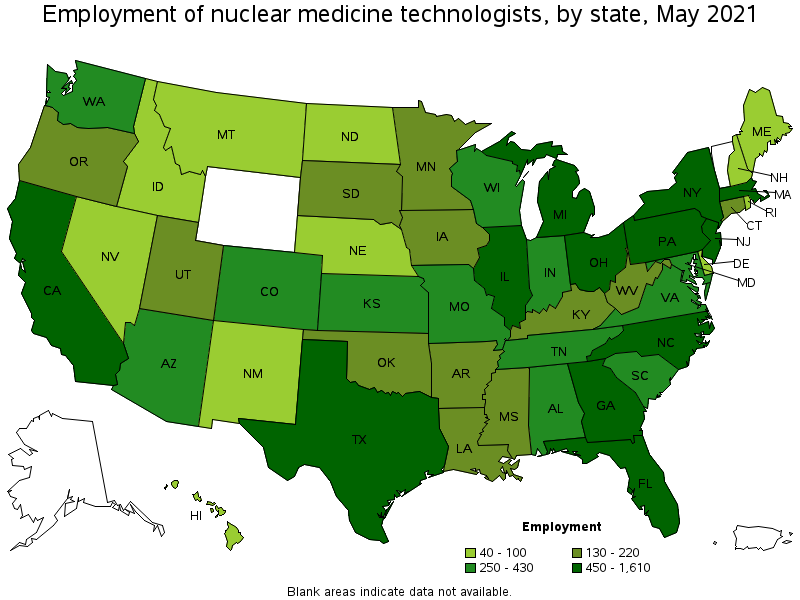
What salary is a robot engineer earning? Continue reading to find out about the job responsibilities and average salary for this profession. Find out how much it costs to live in different places and what experience is required to become a robot engineer. A robotic engineer can enjoy many benefits.
Average salary of a robotics engineer
Your experience, seniority and salary will all impact the average salary for a robot engineer. Engineers generally earn more as they move up in the hierarchy. Robotics engineers are the most highly paid tech workers and they enjoy their work. Robotics engineers will need to be creative problem solvers in order to keep up with the changing field. Robotics engineering requires an array of skills, as well a solid understanding of mathematics.
According to National Careers Service, an average robotic engineer's salary is PS27.500 per year. But, the starting salary for a position that focuses on maintenance or operation can be lower than this. The company's size is another factor that can impact starting salaries. Companies with larger budgets tend to offer higher starting wages.
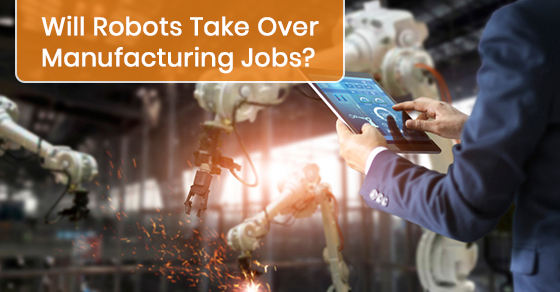
Robotics engineers have specific job responsibilities
A robotics engineer's job involves developing and writing algorithms and programming code. They are also involved in research and development of robotics technology. They develop and test new robotic systems. They may also design robotic systems for military defense or high-throughput operations. They will need to be proficient in communication and mathematical concepts.
A robotics engineer must have a high level of skill and be innovative. They should be able anticipate future robotic requirements and collaborate well with others. They must be able collaborate well with engineers.
Cost of living in various cities
If you're searching for a job with robotic engineering, you should look into cities that offer high salaries. Boston, for instance has a strong record in robotics, and is more affordable than other robotics cities. Boston is home to several robotics companies including Boston Dynamics, iRobot, and iRobot.
An average salary for a robotics engineering engineer is $94,310 per the year. This means you can live comfortably even during your mid-career. Some cities have higher living costs than others.
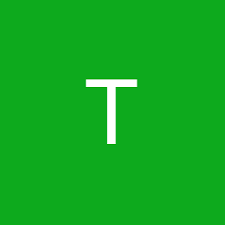
For robotics engineers, you need to have the required experience
You will be a robotics engineer and use computer software for detailed design and testing of robotic systems. You will need to be analytical and able make compromises in order for the robots to function properly. Robotic engineers must also have excellent communication skills and be able to solve problems.
Engineers will often work in a group environment and collaborate on software development. Engineers must be able to communicate with experts in their field and have strong communication skills. The job requires you to regularly deliver reports to investors or other stakeholders. Robotics engineers will need to have strong teamwork skills, because there are many risks involved in developing a robot. An entire system can be affected by a single error.
FAQ
How can I learn about manufacturing?
Practical experience is the best way of learning about manufacturing. But if that is not possible you can always read books and watch educational videos.
Why automate your warehouse
Modern warehousing has seen automation take center stage. E-commerce has brought increased demand for more efficient and quicker delivery times.
Warehouses must adapt quickly to meet changing customer needs. Technology investment is necessary to enable warehouses to respond quickly to changing demands. Automation warehouses can bring many benefits. These are just a few reasons to invest in automation.
-
Increases throughput/productivity
-
Reduces errors
-
Accuracy is improved
-
Safety increases
-
Eliminates bottlenecks
-
Allows companies scale more easily
-
It makes workers more efficient
-
This gives you visibility into what happens in the warehouse
-
Enhances customer experience
-
Improves employee satisfaction
-
Reduces downtime and improves uptime
-
High quality products delivered on-time
-
Removing human error
-
Helps ensure compliance with regulations
How does a Production Planner differ from a Project Manager?
A production planner is more involved in the planning phase of the project than a project manger.
How can manufacturing avoid production bottlenecks
To avoid production bottlenecks, ensure that all processes run smoothly from the moment you receive your order to the time the product ships.
This includes planning for both capacity requirements and quality control measures.
Continuous improvement techniques such Six Sigma can help you achieve this.
Six Sigma Management System is a method to increase quality and reduce waste throughout your organization.
It emphasizes consistency and eliminating variance in your work.
What is the job of a logistics manger?
A logistics manager ensures that all goods are delivered on time and without damage. This is done using his/her knowledge of the company's products. He/she also needs to ensure adequate stock to meet demand.
What does "warehouse" mean?
A warehouse or storage facility is where goods are stored before they are sold. It can be an outdoor or indoor area. Sometimes, it can be both an indoor and outdoor space.
Statistics
- In the United States, for example, manufacturing makes up 15% of the economic output. (twi-global.com)
- It's estimated that 10.8% of the U.S. GDP in 2020 was contributed to manufacturing. (investopedia.com)
- You can multiply the result by 100 to get the total percent of monthly overhead. (investopedia.com)
- In 2021, an estimated 12.1 million Americans work in the manufacturing sector.6 (investopedia.com)
- (2:04) MTO is a production technique wherein products are customized according to customer specifications, and production only starts after an order is received. (oracle.com)
External Links
How To
How to Use the 5S to Increase Productivity In Manufacturing
5S stands to stand for "Sort", “Set In Order", “Standardize", and "Store". Toyota Motor Corporation developed the 5S method in 1954. This methodology helps companies improve their work environment to increase efficiency.
This method has the basic goal of standardizing production processes to make them repeatable. Cleaning, sorting and packing are all done daily. Workers can be more productive by knowing what to expect.
Five steps are required to implement 5S: Sort, Set In Order, Standardize. Separate. Each step is a different action that leads to greater efficiency. If you sort items, it makes them easier to find later. Once you have placed items in an ordered fashion, you will put them together. After you have divided your inventory into groups you can store them in easy-to-reach containers. Labeling your containers will ensure that everything is correctly labeled.
This process requires employees to think critically about how they do their job. Employees should understand why they do the tasks they do, and then decide if there are better ways to accomplish them. To be successful in the 5S system, employees will need to acquire new skills and techniques.
The 5S Method not only improves efficiency, but it also helps employees to be more productive and happier. They feel more motivated to work towards achieving greater efficiency as they see the results.