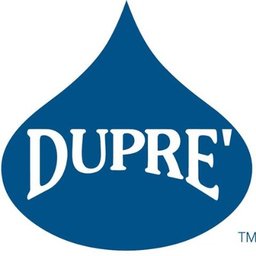
Do you have a passion for asset protection and Walmart? Read on to discover how much these positions pay and the important safety procedures involved. If you're convinced that Walmart is right for you, then apply today. Learn more about Walmart's Asset Protection Associate Salary, Compensation and Safety Procedures. Learn more about this job and the benefits it offers. To find out more, complete the online application. To get started, an account is necessary.
Walmart asset protection associates can expect a range of salaries
Walmart Asset Protection Associate earns an average salary of Rs 1.8 Lakhs to RS 2.2 Lakhs per annum. This figure is based upon statistical methods and the actual salaries of six employees at Walmart Asset Protection Associates. For more information on this job, please see the following. The salary estimates are based upon 6 anonymous salaries submitted to Glassdoor.com by Asset Protection Associates. This information does NOT include bonuses, overtime, and other compensation.
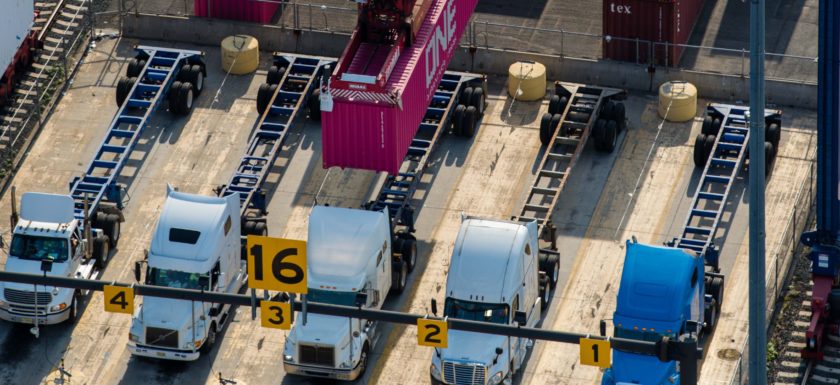
This job is ideal for people who have criminal records and a background in loss prevention. Whether you are looking for a career in retail loss prevention or criminal justice, Walmart offers numerous career paths and salary ranges for asset protection associates. Walmart Careers provides job descriptions that can be accessed by interested applicants. You will find more information about the job and responsibilities. Simply sign the disclosures to apply and create a profile. If you're applying for an AP Manager position, then you can fill out a job application and upload a resume.
Safety procedures
Walmart is one of the most diverse and largest retailers in the world and has many safety and security concerns. Listed below are the top priorities and safety procedures for Walmart's Asset Protection program. Mike Lamb, vice president of Walmart US's asset protection and safety department, explains how these policies help protect Walmart's assets, while addressing the most common problems and opportunities. This program is designed to help associates safeguard the company's assets while keeping customers and employees safe.
Associate: Walmart Asset Protection program Associates help store managers and employees prevent theft and fraud. Although entry-level positions are not required, managers must possess a Bachelor’s degree or Loss Prevention Qualified Certificate. For entry-level roles, however, a Loss Prevention Qualified Certificate or a degree relating to criminal justice are required.
Compensation
The average Walmart Asset Protection compensation is $33,000 per year, based on the salaries of 974 people with this job title. This figure includes tips, taxes, bonuses, and wages. It can vary depending upon education and experience. This information is anonymous and does not reflect the actual salary of Walmart Asset Protection employees. It is a good starting point to determine the salary you are entitled to.
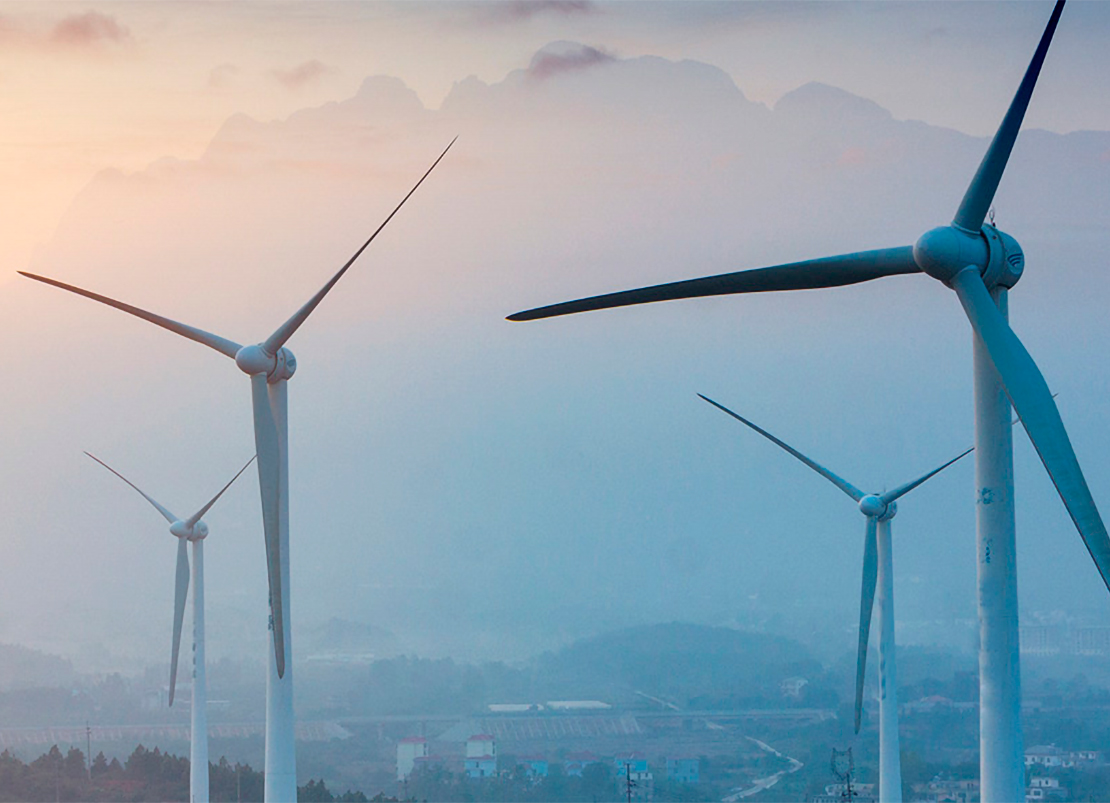
Wal-Mart will continue to give bonuses to store managers that can be tied to store performance. Walmart also knows that long-term employees are more likely receive raises than newer employees. Associates with years of experience can request raises up to twice a year. The average hourly wage range is between $12 and $16. The following table shows you the typical Walmart Ap Host salary. Visit the official Walmart website for more information.
FAQ
What does the term manufacturing industries mean?
Manufacturing Industries refers to businesses that manufacture products. Consumers are people who purchase these goods. These companies employ many processes to achieve this purpose, such as production and distribution, retailing, management and so on. They produce goods from raw materials by using machines and other machinery. This includes all types manufactured goods such as clothing, building materials, furniture, electronics, tools and machinery.
What are the responsibilities of a logistic manager?
Logistics managers make sure all goods are delivered on schedule and without damage. This is done using his/her knowledge of the company's products. He/she must also ensure sufficient stock to meet the demand.
What are the jobs in logistics?
Logistics can offer many different jobs. Some examples are:
-
Warehouse workers: They load and unload trucks, pallets, and other cargo.
-
Transportation drivers – These drivers drive trucks and wagons to transport goods and pick up the goods.
-
Freight handlers, - They sort out and pack freight in warehouses.
-
Inventory managers: They are responsible for the inventory and management of warehouses.
-
Sales representatives: They sell products to customers.
-
Logistics coordinators – They plan and coordinate logistics operations.
-
Purchasing agents - They purchase goods and services needed for company operations.
-
Customer service agents - They answer phone calls and respond to emails.
-
Shipping clerks: They process shipping requests and issue bills.
-
Order fillers: They fill orders based off what has been ordered and shipped.
-
Quality control inspectors: They inspect outgoing and incoming products for any defects.
-
Others - There are many types of jobs in logistics such as transport supervisors and cargo specialists.
How can manufacturing efficiency improved?
First, we need to identify which factors are most critical in affecting production times. Then we need to find ways to improve these factors. If you don't know where to start, then think about which factor(s) have the biggest impact on production time. Once you've identified them, try to find solutions for each of those factors.
Statistics
- [54][55] These are the top 50 countries by the total value of manufacturing output in US dollars for its noted year according to World Bank.[56] (en.wikipedia.org)
- Many factories witnessed a 30% increase in output due to the shift to electric motors. (en.wikipedia.org)
- Job #1 is delivering the ordered product according to specifications: color, size, brand, and quantity. (netsuite.com)
- According to a Statista study, U.S. businesses spent $1.63 trillion on logistics in 2019, moving goods from origin to end user through various supply chain network segments. (netsuite.com)
- (2:04) MTO is a production technique wherein products are customized according to customer specifications, and production only starts after an order is received. (oracle.com)
External Links
How To
Six Sigma: How to Use it in Manufacturing
Six Sigma is "the application statistical process control (SPC), techniques for continuous improvement." Motorola's Quality Improvement Department developed it at their Tokyo plant in Japan in 1986. Six Sigma is a method to improve quality through standardization and elimination of defects. Since there are no perfect products, or services, this approach has been adopted by many companies over the years. The main goal of Six Sigma is to reduce variation from the mean value of production. It is possible to measure the performance of your product against an average and find the percentage of time that it differs from the norm. If it is too large, it means that there are problems.
The first step toward implementing Six Sigma is understanding how variability works in your business. Once you have this understanding, you will need to identify sources and causes of variation. These variations can also be classified as random or systematic. Random variations happen when people make errors; systematic variations are caused externally. If you make widgets and some of them end up on the assembly line, then those are considered random variations. It would be considered a systematic problem if every widget that you build falls apart at the same location each time.
After identifying the problem areas, you will need to devise solutions. That solution might involve changing the way you do things or redesigning the process altogether. To verify that the changes have worked, you need to test them again. If they fail, you can go back to the drawing board to come up with a different plan.