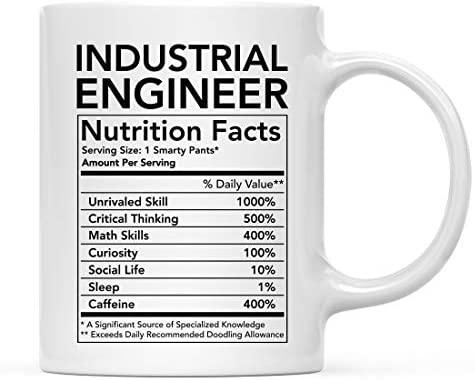
They are responsible for all aspects of purchasing, including sourcing and coordination. They deal with suppliers, buyers, and other agents. They must be knowledgeable about the company's purchasing process and how to improve it. They must also know how to negotiate the best deal for the company.
Purchaser managers must also keep accurate and current purchasing records. They are responsible for analyzing customer needs and evaluating vendor capabilities. They coordinate purchasing activities with other departments. They may be required to work overtime if the company needs supplies from international markets.
Coordinate and manage inventory, logistics and other activities. They decide the best purchase method and ensure all purchases meet company quality standards. They help to manage budgets and coordinate with their staff to ensure that purchases can be made at the most affordable price. They are also able to negotiate contracts and find the best suppliers.
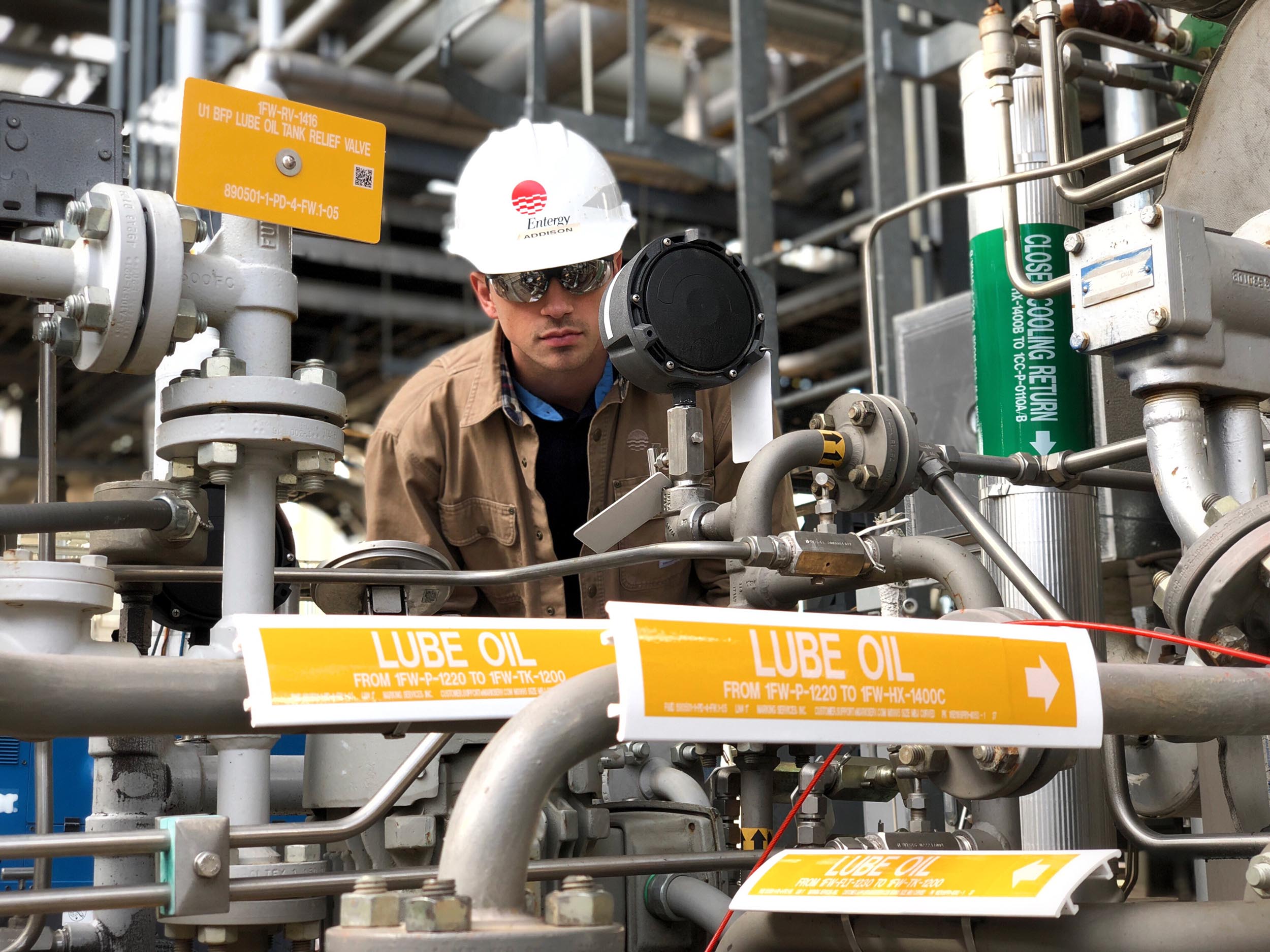
All purchasing employees must be monitored and managed by Purchasing managers. They also evaluate the quality of goods purchased, their speed of delivery and how much they cost. They meet with suppliers and buyers and visit their distribution facilities. They also make sure that suppliers comply with the terms of the contract. They may also be responsible for disciplinary matters and team building.
Excellent communication skills and analytical abilities are essential for purchasing managers. They also need to be strategic thinkers. They should be able analyze the impact of different products on the company. They should also know how to manage suppliers. They must also be able to make business decisions and increase sales. They must also be capable of handling complicated purchases. They must be able to evaluate new vendors, analyze their capabilities, and select the best vendor for the company.
The majority of purchasing managers need to have a bachelor's in business or another related field. A bachelor's degree in business or a related field is helpful. They must be proficient in Microsoft Office and other computer software programs.
The best purchasing manager should be capable of finding the best deals, and negotiating the most favorable contracts. They should be able to coordinate all purchases, manage inventories, and keep track on supplier and vendor performance. They should also possess the ability to manage a small team of purchasing agents.

A job description for the purchase manager should include a mention of how important purchasing is to the company. It should also include how vital it is for the company that they stay ahead of their competitors. It should also reflect how much the company values its employees' personal and professional lives. It should also contain a call-to-action to encourage applicants.
Sometimes, the Purchasing Manager may be required to work overtime in order to purchase equipment and materials for an international marketplace. They might also need to meet with sellers and vendors or attend trade shows.
FAQ
Why automate your warehouse
Modern warehousing has seen automation take center stage. E-commerce has increased the demand for quicker delivery times and more efficient processes.
Warehouses must adapt quickly to meet changing customer needs. They must invest heavily in technology to do this. Automating warehouses is a great way to save money. These are just a few reasons to invest in automation.
-
Increases throughput/productivity
-
Reduces errors
-
Increases accuracy
-
Safety Boosts
-
Eliminates bottlenecks
-
This allows companies to scale easily
-
It makes workers more efficient
-
The warehouse can be viewed from all angles.
-
Enhances customer experience
-
Improves employee satisfaction
-
It reduces downtime, and increases uptime
-
Quality products delivered on time
-
Removes human error
-
Assure compliance with regulations
What is the responsibility of a production planner?
Production planners ensure that all project aspects are completed on time, within budget and within the scope. A production planner ensures that the service and product meet the client's expectations.
How can manufacturing avoid production bottlenecks
You can avoid bottlenecks in production by making sure that everything runs smoothly throughout the production cycle, from the moment you receive an order to the moment the product is shipped.
This includes planning for both capacity requirements and quality control measures.
Continuous improvement techniques like Six Sigma are the best way to achieve this.
Six Sigma Management System is a method to increase quality and reduce waste throughout your organization.
It seeks to eliminate variation and create consistency in your work.
What does warehouse refer to?
A warehouse is an area where goods are stored before being sold. It can be an outdoor or indoor area. It could be one or both.
What are the requirements to start a logistics business?
A successful logistics business requires a lot more than just knowledge. To communicate effectively with clients and suppliers, you must be able to communicate well. You need to understand how to analyze data and draw conclusions from it. You must be able and able to handle stress situations and work under pressure. To increase efficiency and creativity, you need to be creative. You will need strong leadership skills to motivate and direct your team members towards achieving their organizational goals.
You should also be organized and efficient to meet tight deadlines.
What skills does a production planner need?
Production planners must be flexible, organized, and able handle multiple tasks. Effective communication with clients and colleagues is essential.
What is production planning?
Production Planning refers to the development of a plan for every aspect of production. It is important to have everything ready and planned before you start shooting. This document should also include information on how to get the best result on set. This includes shooting schedules, locations, cast lists, crew details, and equipment requirements.
It is important to first outline the type of film you would like to make. You may already know where you want the film to be shot, or perhaps you have specific locations and sets you wish to use. Once you've identified the locations and scenes you want to use, you can begin to plan what elements you need for each scene. You might decide you need a car, but not sure what make or model. If this is the case, you might start searching online for car models and then narrow your options by selecting from different makes.
After you have chosen the right car, you will be able to begin thinking about accessories. Are you looking for people to sit in the front seats? Maybe you need someone to move around in the back. Perhaps you would like to change the interior colour from black to white. These questions can help you decide the right look for your car. The type of shots that you are looking for is another thing to consider. Will you be filming close-ups or wide angles? Perhaps you want to show the engine or the steering wheel? This will allow you to determine the type of car you want.
Once you have determined all of the above, you can move on to creating a schedule. You will know when you should start and when you should finish shooting. Each day will include the time when you need to arrive at the location, when you need to leave and when you need to return home. Everyone will know what they need and when. Book extra staff ahead of time if you need them. There is no point in hiring someone who won't turn up because you didn't let him know.
It is important to calculate the amount of filming days when you are creating your schedule. Some projects may only take a couple of days, while others could last for weeks. When you are creating your schedule, you should always keep in mind whether you need more than one shot per day or not. Multiple shots at the same location can increase costs and make it more difficult to complete. It is better to be cautious and take fewer shots than you risk losing money if you are not sure if multiple takes are necessary.
Budget setting is an important part of production planning. As it will allow you and your team to work within your financial means, setting a realistic budget is crucial. You can always lower the budget if you encounter unexpected problems. However, it is important not to overestimate the amount that you will spend. You'll end up with less money after paying for other things if the cost is underestimated.
Production planning is a very detailed process, but once you understand how everything works together, it becomes easier to plan future projects.
Statistics
- It's estimated that 10.8% of the U.S. GDP in 2020 was contributed to manufacturing. (investopedia.com)
- Many factories witnessed a 30% increase in output due to the shift to electric motors. (en.wikipedia.org)
- (2:04) MTO is a production technique wherein products are customized according to customer specifications, and production only starts after an order is received. (oracle.com)
- According to a Statista study, U.S. businesses spent $1.63 trillion on logistics in 2019, moving goods from origin to end user through various supply chain network segments. (netsuite.com)
- In 2021, an estimated 12.1 million Americans work in the manufacturing sector.6 (investopedia.com)
External Links
How To
How to Use the Just-In-Time Method in Production
Just-in-time is a way to cut costs and increase efficiency in business processes. It allows you to get the right amount resources at the right time. This means that you only pay the amount you actually use. Frederick Taylor was the first to coin this term. He developed it while working as a foreman during the early 1900s. He saw how overtime was paid to workers for work that was delayed. He then concluded that if he could ensure that workers had enough time to do their job before starting to work, this would improve productivity.
JIT teaches you to plan ahead and prepare everything so you don’t waste time. The entire project should be looked at from start to finish. You need to ensure you have enough resources to tackle any issues that might arise. If you expect problems to arise, you will be able to provide the necessary equipment and personnel to address them. You won't have to pay more for unnecessary items.
There are many JIT methods.
-
Demand-driven: This is a type of JIT where you order the parts/materials needed for your project regularly. This will let you track the amount of material left over after you've used it. This will allow to you estimate the time it will take for more to be produced.
-
Inventory-based : You can stock the materials you need in advance. This allows one to predict how much they will sell.
-
Project-driven: This approach involves setting aside sufficient funds to cover your project's costs. Once you have an idea of how much material you will need, you can purchase the necessary materials.
-
Resource-based JIT is the most widespread form. Here you can allocate certain resources based purely on demand. For example, if there is a lot of work coming in, you will have more people assigned to them. If you don’t have many orders you will assign less people to the work.
-
Cost-based: This is the same as resource-based except that you don't care how many people there are but how much each one of them costs.
-
Price-based: This approach is very similar to the cost-based method except that you don't look at individual workers costs but the total cost of the company.
-
Material-based: This is very similar to cost-based but instead of looking at total costs of the company you are concerned with how many raw materials you use on an average.
-
Time-based JIT is another form of resource-based JIT. Instead of worrying about how much each worker costs, you can focus on how long the project takes.
-
Quality-based JIT is another variant of resource-based JIT. Instead of worrying about the costs of each employee or how long it takes for something to be made, you should think about how quality your product is.
-
Value-based JIT is the newest form of JIT. This is where you don't care about how the products perform or whether they meet customers' expectations. Instead, your focus is on the value you bring to the market.
-
Stock-based: This inventory-based approach focuses on how many items are being produced at any one time. It is used when production goals are met while inventory is kept to a minimum.
-
Just-intime planning (JIT), is a combination JIT/sales chain management. It is the process that schedules the delivery of components within a short time of their order. It is essential because it reduces lead-times and increases throughput.